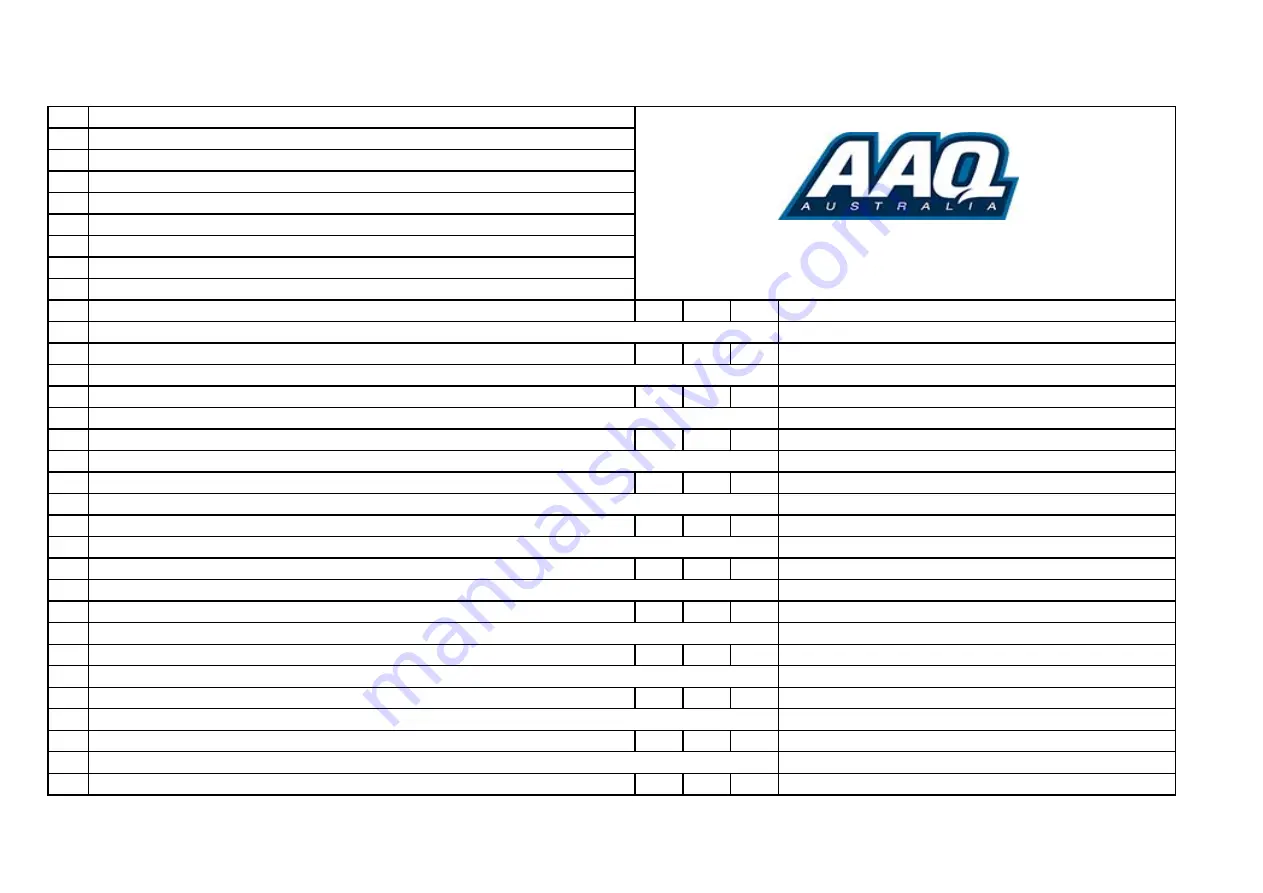
COMMISSIONING REPORT
1. Details of Customer
Customer Name:
Installation Address:
2. Hoist Details
Model No:
Hoist Type:
Installation Date:
3. Commissioning Report
Yes
No
N/A
Comments
Safety devices incorporated into the design of the vehicle to AS/NZS 1418.9
Visual check all welds completed and comply to requirement of AS/NZS 1554
Visual check carried out for leaks
Visual check carried out for leaks
Safety locks tested for correct operation
Checked for good working order
Supplied with the hoist and in good working order
Checked for correct operation
Hoist checked with load for correct operation and speed control tested
Checked wire ropes for correct installation and tension
Concrete floor is a suitable depth for installation
Safety Devices
Welds
Hydraulic Equipment and Controls
Pneumatic Equipment and Controls
Safety Locks
Support Pads
Wheel Stops
Hoist Motion Limits
Load Test and Speed Check
Wire Ropes
Concrete Floor
2 McDonald Crescent
Bassendean WA 6054
P: 08 9279 1663 | E: [email protected]
1