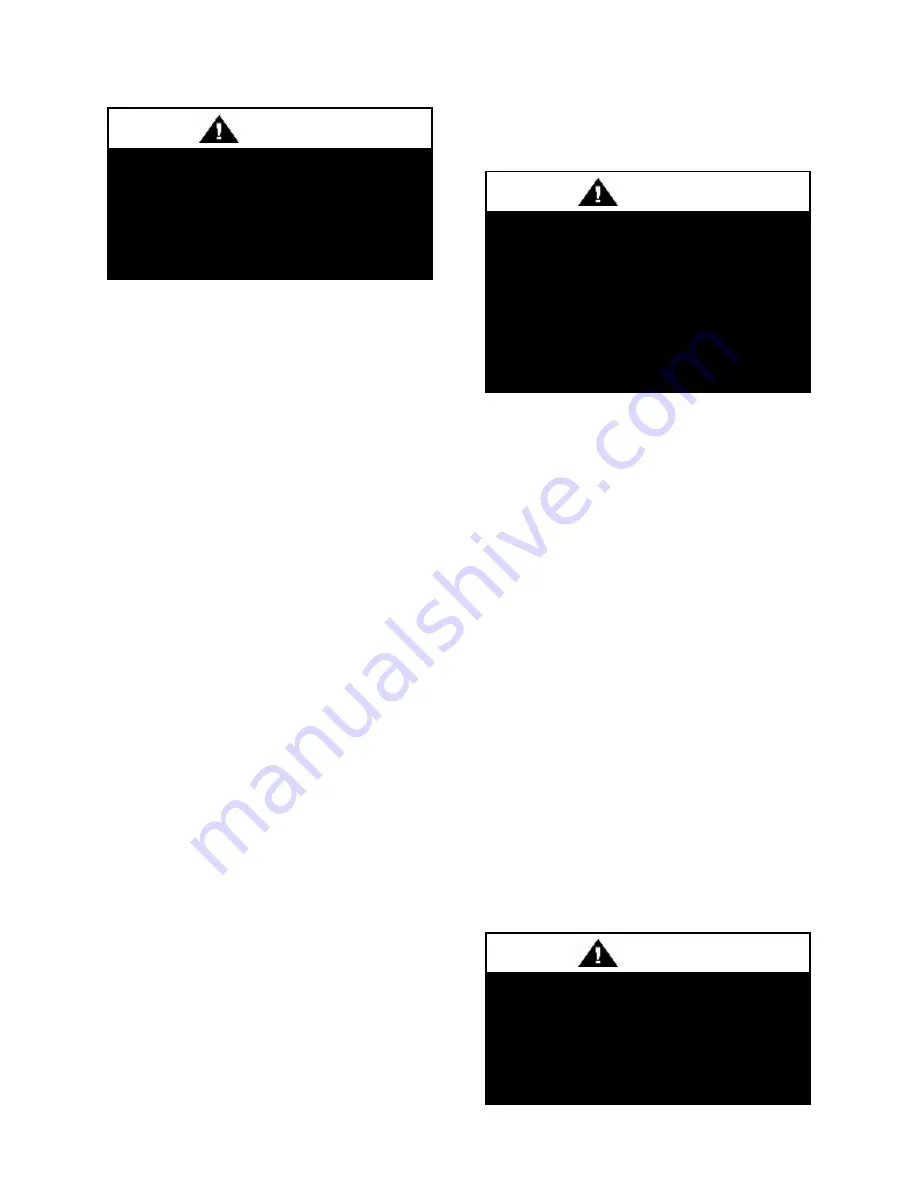
33
Piping systems should not exceed 10 ft/sec
fluid velocity to ensure tube wall integrity
and reduce noise.
Brazed Plate Heat Exchanger Cleaning
Because of a normally high degree of
turbulence in brazed plate heat exchangers,
for many applications the heat exchanger
channels are self cleaning. For applications
that are not self cleaning (i.e. hard water at
high temperatures, etc.) or applications
where additional cleaning is desired, it is
possible to clean the brazed plate heat
exchanger by circulating a cleaning liquid.
Use a tank with weak acid, 5% phosphoric
acid (H
3
PO
4
) or, if the exchanger is
frequently
cleaned,
5%
oxalic
acid
(H
2
C
2
O
4
). Pump the cleaning liquid through
the exchanger. For optimum cleaning, the
cleaning solution flow rate should be a
minimum of 1.5 times the normal flow rate,
preferably in a back-flush mode. After
cleaning, the heat exchanger must be rinsed
with clean water. A solution of 1-2% sodium
hydroxide (NaOH) or sodium bicarbonate
(NaHCO) before the last rinse ensures that
all acid is neutralized.
Electrical
Verify the unit name plate agrees with
power supply. SA Series units are provided
with single point power wiring connections.
Connection terminations are made to the
main terminal block. A complete set of unit
specific wiring diagrams, showing factory
and field wiring are laminated in plastic and
located inside the controls compartment
door.
All units require field supplied electrical
overcurrent and short circuit protection.
Device must not be sized larger than the
Maximum Overcurrent Protection (MOP)
shown on the unit nameplate.
Codes may require a disconnect switch be
within sight of the unit.
It is recommended that the field installed
overcurrent protection or disconnect switch
not be installed on the unit.
Electrical supply can enter through the
bottom or side of the controls compartment.
Entry must be field cut into panels of the
unit.
A single point connection to a terminal
block is provided. Split units may require
connection between the units. High voltage
conductors should enter the control panel in
a separate opening and separate conduit than
24V low voltage conductors.
Do
not
exceed
recommended
condenser fluid flow rates shown in
above table. Serious damage to or
erosion of the heat exchanger tubes
could occur.
CAUTION
Disconnect
all
electrical
power
sources before servicing the unit.
More than one power source may be
provided. Failure to do so may result
in injury or death from electrical
shock or entanglement in moving
parts.
WARNING
The
foam
insulation
releases
dangerous fumes when it is burnt. Do
not cut a foam part with a cutting
torch or plasma cutter. Do not weld to
a foam filled part.
WARNING
Summary of Contents for SA-028
Page 2: ......
Page 20: ...20 Figure 2 One Piece Single Unit Lifting Details...
Page 21: ...21 Figure 3 Two Piece Single Unit Coil Section Lifting Details...
Page 22: ...22 Figure 4 Two Piece Single Unit Fan Section Lifting Details...
Page 23: ...23 Figure 5 One Piece Dual Unit Lifting Details...
Page 24: ...24 Figure 6 Two Piece Dual Unit Coil Section Lifting Details...
Page 25: ...25 Figure 7 Two Piece Dual Unit Fan Section Lifting Details...
Page 28: ...28 Figure 10 Dual unit with splices after being bolted together...
Page 63: ...63...