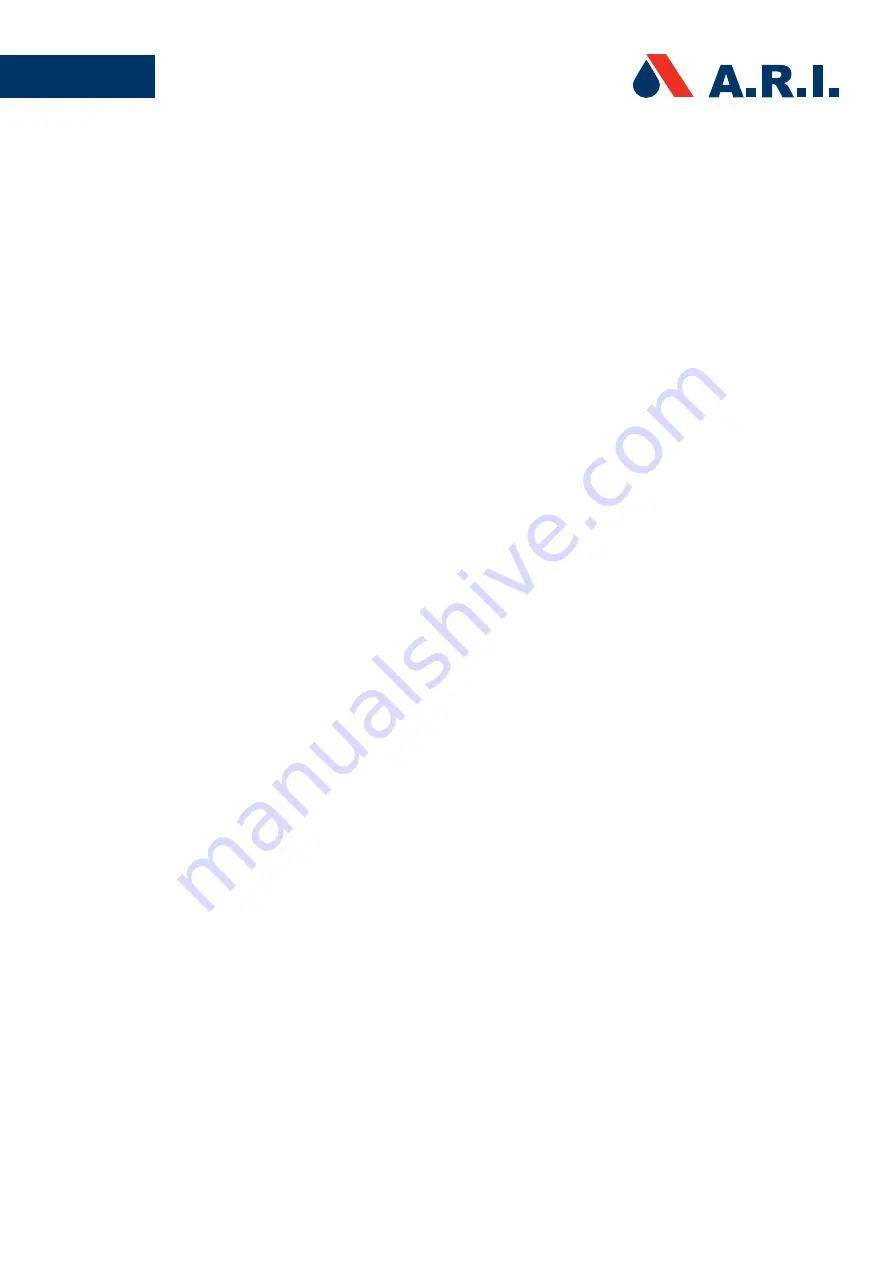
7
IOM
2.3.
Installation Instructions
1.
Flush the system before installing the air valve to avoid any debris or sharp objects getting into the air
valve.
2.
Carefully remove the air valve from the shipping package. Unload all air valves carefully to a sturdy level
surface taking care not to drop them.
3.
Air valves fitted with hoist rings should only be lifted and conveyed using these hoist rings.
4.
Install an isolating valve below the air valve, connected by a Riser to the crown of the pipe.
5.
Mount the air valve carefully on the rubber gaskets of the isolating valve.
6.
Place washers on each of the bolts & nuts that connect the air valve flange to the isolating valve flange.
7.
Tighten all the bolts and nuts using the crossover method.
8.
The closure tightness of the bolts and nuts shall be according to the standard torque for their specific
size.
9.
Use ring wrench keys for the closing and opening of all bolts of the air valve (including the flange bolts).
2.4.
Directions for Discharge Outlet
1.
Recommended to leave the discharge outlet completely open and unhindered:
2.
Avoid directing the discharge outlet opening in the direction of workers, bystanders or animals.
3.
Avoid directing the discharge outlet opening in the direction of vulnerable equipment that can be
damaged, such as electrical equipment, unstable structures, etc.