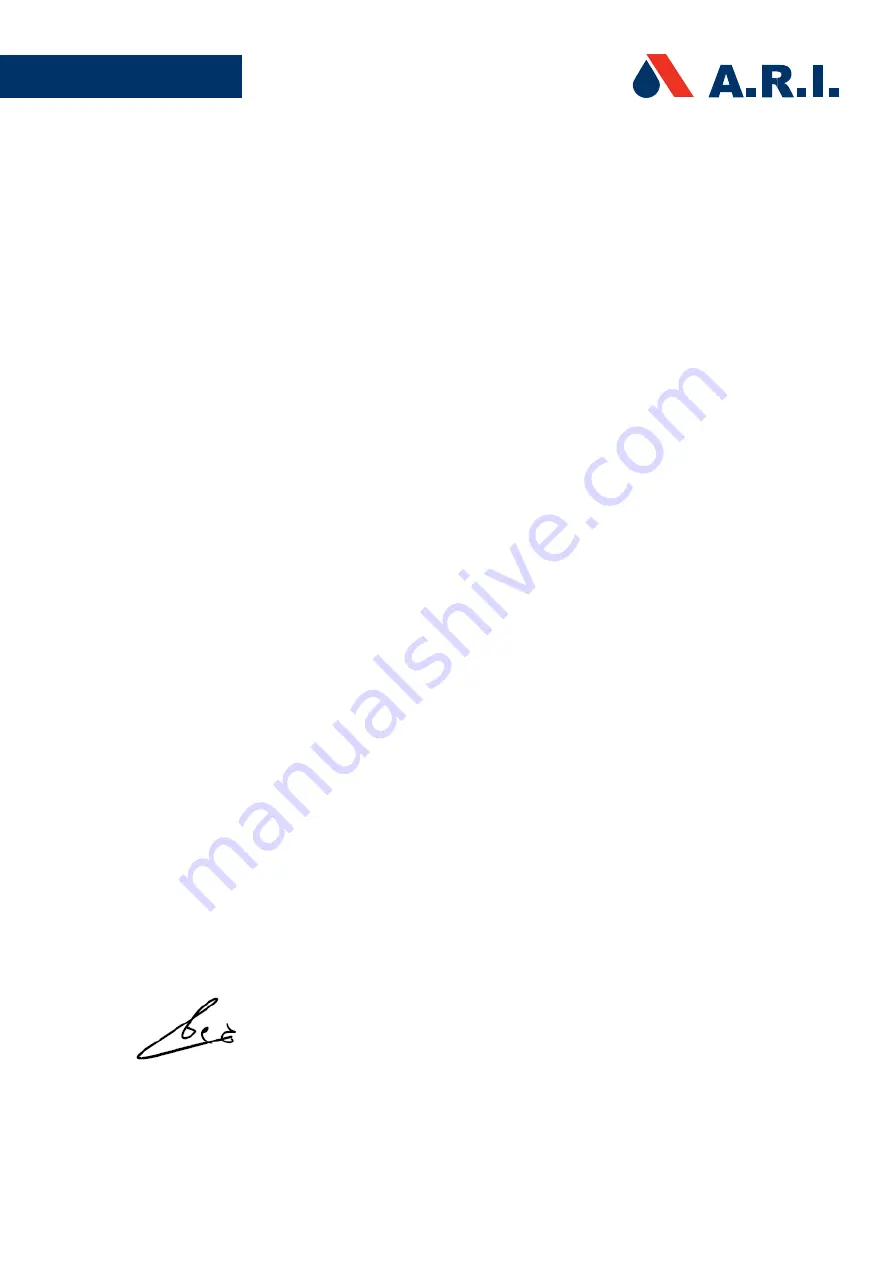
21
IOM D-040L 2”
7. A.R.I. LIMITED WARRANTY
A.R.I. Standard International Warranty
A.R.I. manufactured products are guaranteed to be free from defect in material and/or
workmanship and to perform as advertised when properly installed, used and maintained in
accordance with current instructions, written or verbal.
Should any item prove defective within the time period set forth for that item(s), but in any case not
later than within
12
(twelve) months of that product having left A.R.I.’s premises, and subject to
receipt by A.R.I. or its authorized representative, of written notice thereof from the purchaser
within
30
days of discovery of such defect or failure - A.R.I. will repair or replace or refund the
purchase price, at its sole option, any items proven defective in workmanship or material.
A.R.I. will not be responsible, nor does this warranty extended to any consequential or incidental
damages or expenses of any kind or nature regardless of the nature thereof, including without
limitation, injury to persons or property, loss of use of the products, loss of goodwill, loss of profits
or any other contingent liabilities of any kind or character alleged to be the cause of loss or damage
to the purchaser.
This warranty does not cover damage or failure caused by misuse, abuse or negligence, nor shall it
apply to our products upon which repairs or alterations have been made by other than an
authorized A.R.I. representative.
This warranty does not extend to components, parts or raw materials used by A.R.I. but
manufactured by others, which shall be only to extent warranted by the manufacturer’s warranty.
THERE ARE NO WARRANTIES, EXPRESS OR IMPLIED, EXCEPT THIS WARRANTY WHICH IS GIVEN IN
LIEU OF ANY OTHER WARRANTIES, EXPRESS OR IMPLIED, INCLUDING ANY IMPLIED WARRANTY OF
FITNESS FOR A PARTICULAR PURPOSE.
(R
10822
)
Guy Sagie
C.E.O