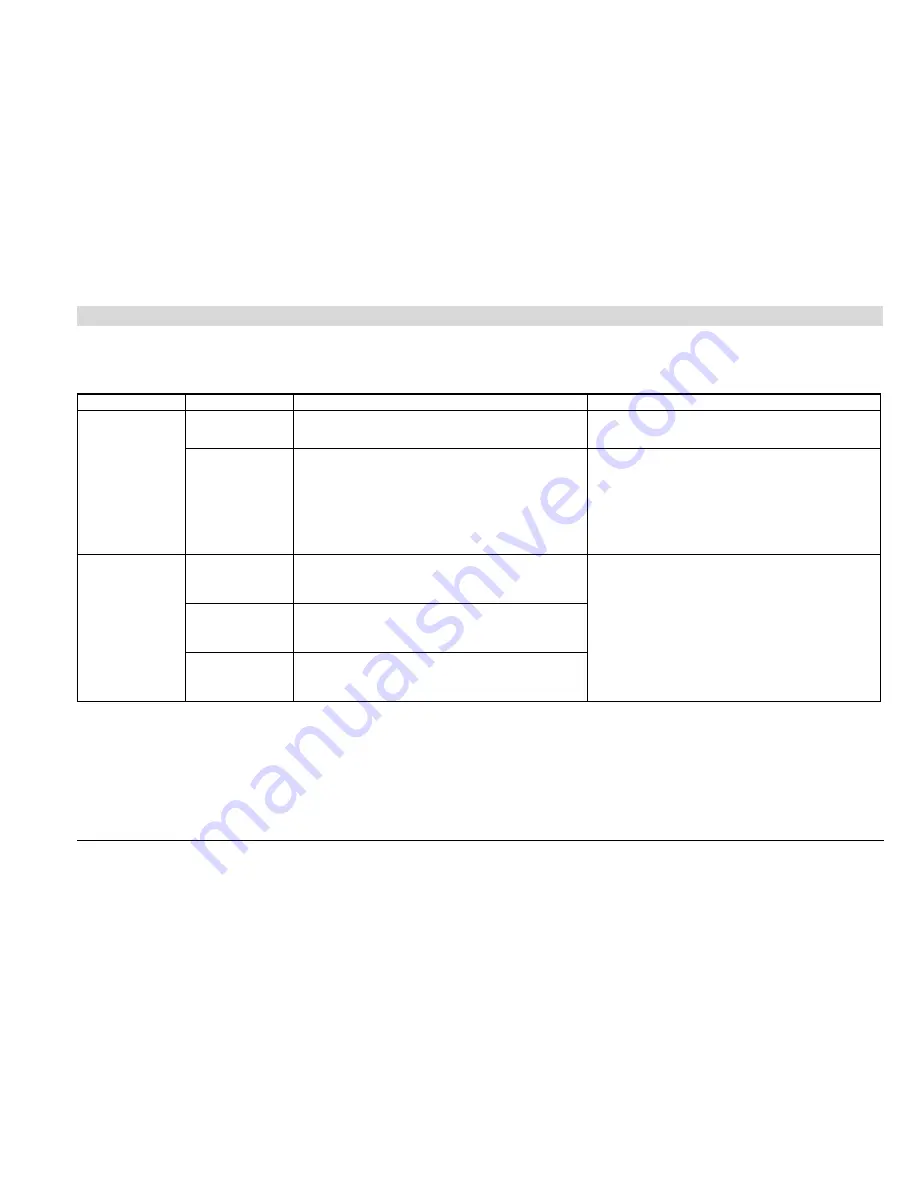
is
Instruction manual GWV
78
Code + description
Cause
Measures to take
Comment
F01 (blocking error)
Defect in power supply
circuit
Live and neutral
connected wrong way
round
Connect live and neutral correctly
(3.10 "Electrical connection")
;
the appliance is phase-sensitive
See the GWV electrical diagram
(17 "Appendices")
Condensation on the
flame probe
1. Disconnect the lead at the flame probe
2. Ignite the appliance three times, with an interrupted ionisation
circuit
3. Reconnect the ionisation lead to the flame probe
4. Ignite the appliance again
5. The repeated ignition attempts will have caused the
condensation to evaporate
If the error persists, contact your installation engineer
F02 (lock out error)
Fan fails to run at
correct speed.
Damaged wiring
1. Check the wiring between the fan and the controller.
2. If any wires are damaged, the wiring harness must be replaced.
3. Reset appliance controller
See the GWV electrical diagram
(17 "Appendices")
To have the wiring replaced and a new fan fitted, you must contact
your installation engineer
Dirty or blocked fan
1. Check if the fan is dirty
2. Check that the rotor can rotate freely
3. Reset appliance controller
Because of a drop in
the supply voltage, the
fan is not running at the
correct speed.
1. Check the supply voltage, this must be 230 VAC (-15%, +10%).
2. Reset appliance controller
Summary of Contents for GWV - 120
Page 2: ...www aosmithinternational com your installer ...
Page 4: ...4 Instruction manual GWV gis ...
Page 8: ...Table of contents 8 Instruction manual GWV ...
Page 12: ...Introduction 12 Instruction manual GWV 1 gis ...
Page 40: ...Installation 40 Instruction manual GWV 3 is ...
Page 42: ...Conversion to a different gas category 42 Instruction manual GWV 4 is ...
Page 46: ...Filling 46 Instruction manual GWV 5 gis ...
Page 58: ...Starting and running 58 Instruction manual GWV 9 gis ...
Page 60: ...Shutting down 60 Instruction manual GWV 10 gis ...
Page 72: ...Service program 72 Instruction manual GWV 12 is ...
Page 86: ...Troubleshooting 86 Instruction manual GWV 13 gis ...
Page 88: ...Maintenance frequency 88 Instruction manual GWV 14 is ...
Page 98: ...Appendices 98 Instruction manual GWV 17 is ...
Page 100: ...Instruction manual GWV 100 ...
Page 102: ...0307 971 4 0 UK Index Instruction manual GWV ...