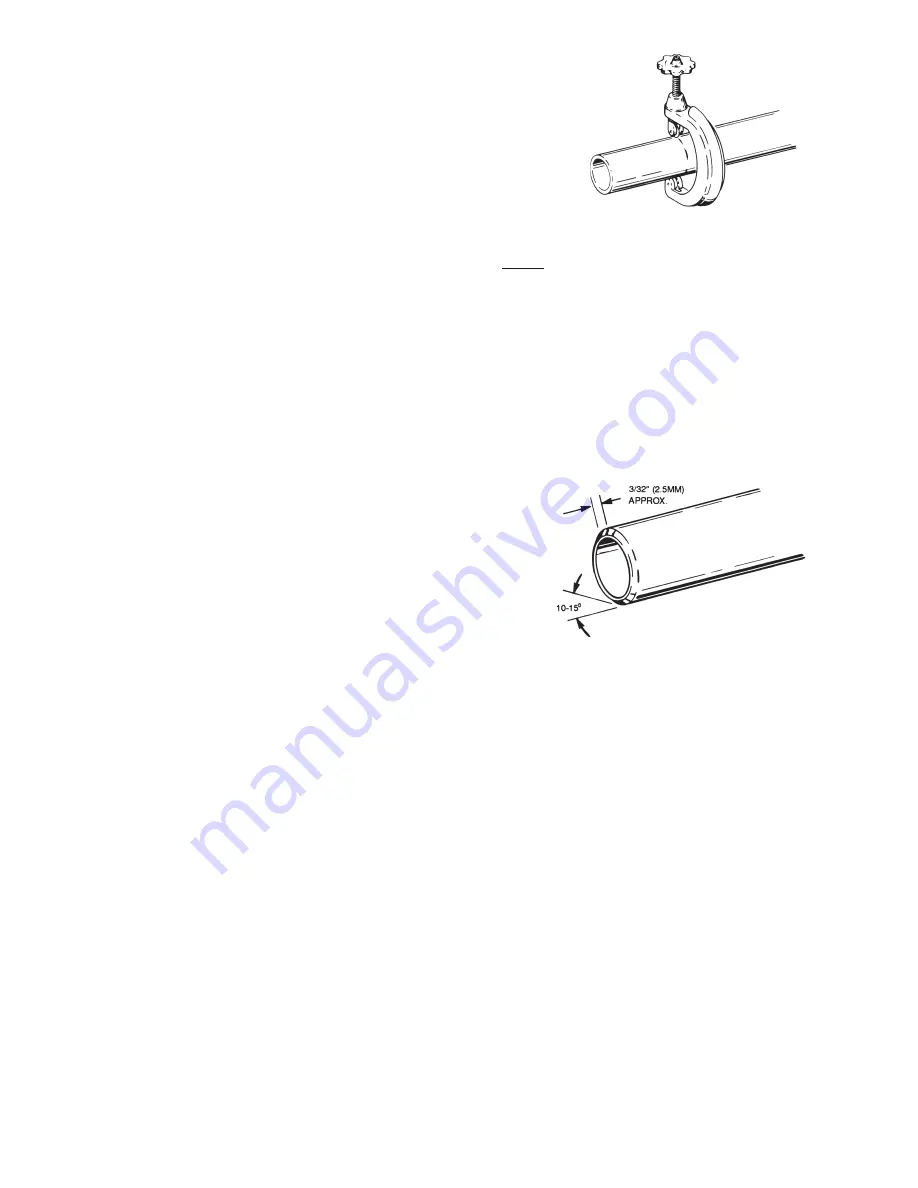
13
F. Contact the manufacturer, supplier, or competent consulting
agency if you have any questions about the application or
installation of PVC and CPVC pipe.
G. Take the time and effort to do a professional job. Shortcuts will
only cause you problems and delays in start-up. By far, the
majority of failures in PVC and CPVC systems are the result
of shortcuts and/or improper joining techniques.
2.
SELECTION OF MATERIALS
• Cutting Device - Saw or Pipe Cutter
• Deburring Tool, Knife, File, or Beveling Machine (2" (5.1 cm)
and above)
• Brush - Pure Bristle
• Rag - Cotton (Not Synthetic)
• Primer and Cleaner
• Solvent Cement - PVC for PVC Components and CPVC for
CPVC Components
• Containers - Metal or Glass to hold Primer and Cement. Select
the type of PVC or CPVC materials to be used on the basis of
their application with respect to chemical resistance, pressure
rating, temperature characteristics, etc.
• Insertion Tool - Helpful for larger diameter pipe and fittings
(6" (15.2 cm) and above).
PRIMER
It is recommended that Tetrahydrofuran (THF) be used to prepare
the surfaces of pipe and fittings for solvent welding. Do not use
water, rags, gasoline or any other substitutes for cleaning PVC or
CPVC Surfaces. A chemical cleaner such as MEK may be used.
CEMENT
The cement should be a bodied cement of approximately 500 to
1600 centipoise viscosity containing 10-20% (by weight) virgin PVC
material solvated with tetrahydrofuran (THF). Small quantities of
dimethyl formamide (DMF) may be included to act as a retarding
agent to extend curing time. Select the proper cement; Schedule
40 cement should be used for Schedule 40 pipe. Never use all-
purpose cements, commercial glues and adhesives or ABS cement
to join PVC or CPVC pipe and fittings.
SAFETY PRECAUTION: PRIMERS AND CEMENTS ARE
EXTREMELY FLAMMABLE, AND MUST NOT BE STORED OR
USED NEAR HEAT OR OPEN FLAME. ALSO, USE ONLY IN A
WELL-VENTILATED AREA.
APPLICATORS
Select a suitable pure bristle type paint brush. Use a proper width
brush or roller to apply the primer and cement (see chart below).
Speedy application of cement is important due to its fast drying
characteristics. IMPORTANT NOTE: A dauber type applicator
should only be used on pipe sizes 2" (5.1 cm) and below. For
larger diameter pipe, a brush or roller must be used.
3.
MAKING THE JOINT
A. Cutting
Pipe must be squarely cut to allow for the proper interfacing of the
pipe end and the fitting socket bottom. This can be accomplished
with a miter box saw or wheel type cutter. Wheel type cutters are
not generally recommended for larger diameters since they tend
to flare the corner of the pipe end. If this type of cutter is used,
the flare on the end must be completely removed.
STEP A
NOTE:
Power saws should be specifically designed to cut
plastic pipe.
B.
Deburring
Use a knife, plastic pipe deburring tool, or file to remove
burrs from the end of small diameter pipe. Be sure to
remove all burrs from around the inside as well as the
outside of the pipe. A slight chamfer (bevel) of about
10°-15° should be added to the end to permit easier
insertion of the pipe into the end of the fitting. Failure to
chamfer the edge of the pipe may remove cement from
the fitting socket, causing the joint to leak.
STEP B
C
.
Test dry fit of the joint
Tapered fitting sockets are designed so that an interference
fit should occur when the pipe is inserted about 1/3 to
2/3 of the way into the socket. Occasionally, when pipe
fitting dimensions are at the tolerance extremes, it will be
possible to fully insert dry pipe to the bottom of the fitting
socket. When this happens, a sufficient quantity of cement
must be applied to the joint to fill the gap between the
pipe and fitting. The gap must be filled to obtain a strong,
leak-free joint.
D. Inspection, cleaning, priming
Visually inspect the inside of the pipe and fitting sockets and
remove all dirt, grease or moisture with a clean dry rag. If
wiping fails to clean the surfaces, a chemical cleaner must be
used. Check for possible damage such as splits or cracks and
replace if necessary.
Depth-of-entry mark
Marking the depth of entry is a way to check if the pipe has
reached the bottom of the fitting socket in step F. Measure
the fitting depth and mark this distance on the pipe O.D.
You may want to add several inches to the distance and
make a second mark as the primer and cement will most
likely destroy your first one.