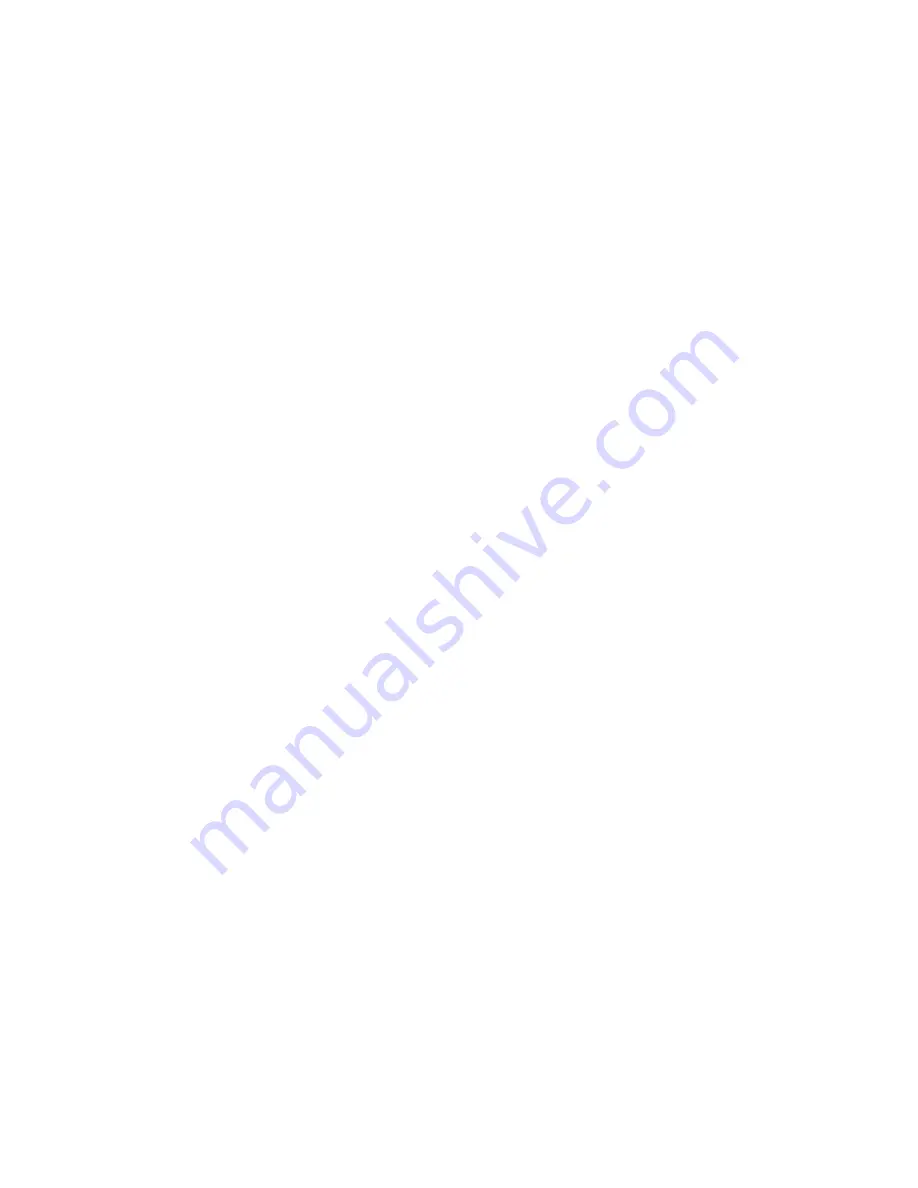
5
1. GENERAL
1.1 Description of the appliance
Construction and fitting out of the storage appliance
comply with the European Standard for gas fired hot
water storage appliances for sanitary use (EN89). The
appliance thereby satisfies the requirements of the
European Directive for Gas Appliances, and is therefore
entitled to bear the CE mark.
The BFM appliance is an enclosed appliance with a
fan in the air inlet ( appliance category C13 or C33 ). The
appliance is designed for a concentric flue
configuration. A diaphragm, across which the pressure
difference can be measured, is fitted in the air inlet
system. When the control thermostat calls for heat, the
burner control unit carries out a zero position check. The
fan is subsequently switched on and, at a signal from
the pressure difference switch, the pre-ventilation
period (minimally 30 seconds) commences. Following
the pre-ventilation period the burner control unit
switches on the ignition transformer whereby the first
gas valve (the pilot) opens. On receiving an ionisation
signal from the ignition burner, the second (main
burner) gas valve opens. The appliance is now in
operation.
Technically this appliance falls into gas category
II2L3P; the appliance is therefore suitable for natural
gas as well as propane and butane gases. The storage
appliance is suitable for working pressures to 8 bar. A
connection is provided for the optional fitting of an extra
safety feature, the temperature and pressure valve. The
interior of the tank is enamelled for corrosion protection,
and a number of magnesium anodes are fitted to the
tank for the same purpose.
A thick polyurethane insulating layer between the tank
and its steel casing prevents unnecessary heat loss. If
the storage appliance is completely filled with water it is
under continual mains pressure. When hot water is
tapped off the appliance, cold water is immediately
introduced. Turbulence strips are placed in the fire tu-
bes for the efficient transfer of heat. The flue gases pass
their heat to the water by conduction and radiation. The
flue gases are led to the flue via the top box. The burner
bed consists of a number of bar burners. An injector is
screwed into the manifold ahead of each burner, which
ensures correct mixing of gas and primary air through
injection into the burner inlet venturi. Secondary air is
drawn between the bar burners. An air distribution plate,
which also functions as a radiant heat shield, is fitted
below the burners. Any condensation water produced is
captured beneath the combustion chamber and led
away via a siphon (see illustration 1).