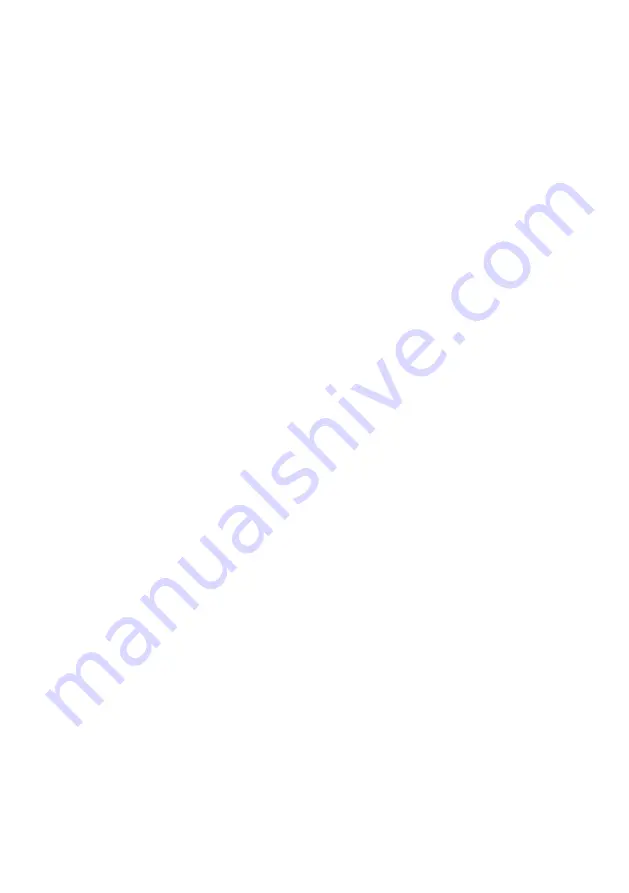
Now carefully apply pressure to the threaded end of the wheel spindle which will eject
from the opposite end of the hub, the washer (7), oil seal (8) and oil seal cup (9), together
with the bearing outer ring (6). The wheel spindle with its two sets of rollers in cages
may now be lifted out leaving in situ only the fixed bearing ring together with the oil
seal, washer and cup for that side bearing.
If it is desired to remove these, pressure is first applied to the visible washer, by which
the assembly is forced inward sufficiently to permit extraction of the retaining circlip
after which through the medium of a mandrel or a piece of tubing of external diameter
a trifle smaller than the hub bore apply pressure to the inner edge of the fixed bearing
ring so that it is forced out of the hub end. As it emerges it will push out the end washer
(2), the oil seal (3) and the oil seal encircling collar (4) and the inner washer (5).
To refit reverse the above procedure remembering that after bearing ring (6), washer (5),
spacer (4), oil seal (3) and washer (2) have been inserted, to refit the circlip (1) snugly
in its groove and to then apply pressure to the inner edge of the bearing ring to force
the assembly tightly back against the retaining circlip.
Finally position the disc when tightening the adjusting ring lock nut so that access to
the grease nipple is possible.
TO DISMANTLE REAR WHEEL BEARINGS
Refer to Illustration
35.
W i t h wheel still in situ first of all slacken the nut (16) securing the speedometer drive
gear box. Then remove the wheel from cycle when the above nut should be removed
and the speedometer gear box withdrawn.
Next, slacken the adjuster sleeve lock nut (13) and completely unscrew the adjuster
sleeve (14) which will come away together with the sleeve upon which speedometer drive
is mounted and also the cover disc. Then withdraw the washer (3) the oil seal (4) and
the oil seal cup (5).
Now turn to the brake side of wheel and using a short bar of 7/8" external diameter apply
pressure to the end of the projecting sleeve, which pressure will force out wheel bearing
ring (7) together with the two taper roller bearings (7) and the spacing sleeve (8), leaving
in situ only the bearing ring on the brake side together with oil seal, washers and retaining
circlip.
If it is desired to remove this spacer bearing ring pressure must be applied to the cup
washer immediately under the circlip until it is possible to extract the circlip. The outer
cup washer (5) the oil seal (4) and the spacer (6), etc., are then free to be withdrawn. The
tearing ring may then be forced out of the end of the hub bore by applying pressure to its
inner edge through the medium of a bar or tube of suitable diameter passed through the
hub bore.
Re-assembly is carried out in exactly reverse order, care being necessary after pressing
in the brake side bearing ring sufficiently far to permit fitting the circlip, to then force
the ring back until cup washer (5) is tightly in contact with the retaining circlip before
proceeding with further assembly.
Final adjustment of the bearings should allow the slightest possible degree of end play
and when correctly adjusted just perceptible rim rock upon refitting the wheel should
be observable.
NOTE—Upon tightening the adjusting ring nut (13) the cover disc must be positioned
to permit application of the gun to the grease nipple, the hole in disc being
provided for that purpose.
FRONT BRAKE COVER PLATE
It is most important the front brake cover plate is correctly positioned.
It is retained to the front wheel spindle by an inside nut (part number 021931) and an
outside nut (part number 018071).
The inside nut must be positioned so that, when the cover plate is applied, the outer face
of the latter lies flush with the hub shell edge.
The outside nut is fitted so that its hexagonal side is against the brake cover plate.
BRAKE DRUMS
The front wheel brake drum is cast in the hub shell.
The rear brake drum is mounted on a separate ball bearing and the drive to rear wheel
is by means of five studs projecting from the hub face which engage with holes in the
drum back face, thereby permitting removal of the rear wheel with the brake drum still
in situ.
66
Summary of Contents for 16
Page 2: ......
Page 21: ...Illustration 8 Cross section of engine showing oil galleries oil passages and release valve 19...
Page 47: ...Illustration 22 Carburetter details in assembly order 45...
Page 59: ...Exploded view of Teledraulic Forks Illustration 29 57...
Page 73: ...71...
Page 74: ...72...
Page 87: ...Illustration 48 Wiring diagram Singles SINGLE CYLINDER MODELS 85...
Page 88: ...Illustration 49 Wiring diagram Magneto Twins TWIN CYLINDER MODELS 86...
Page 89: ...Illustration 50 Wiring diagram Alternator Twins 87...
Page 99: ...Illustration 52 TOOL KIT 97...
Page 103: ......
Page 104: ......