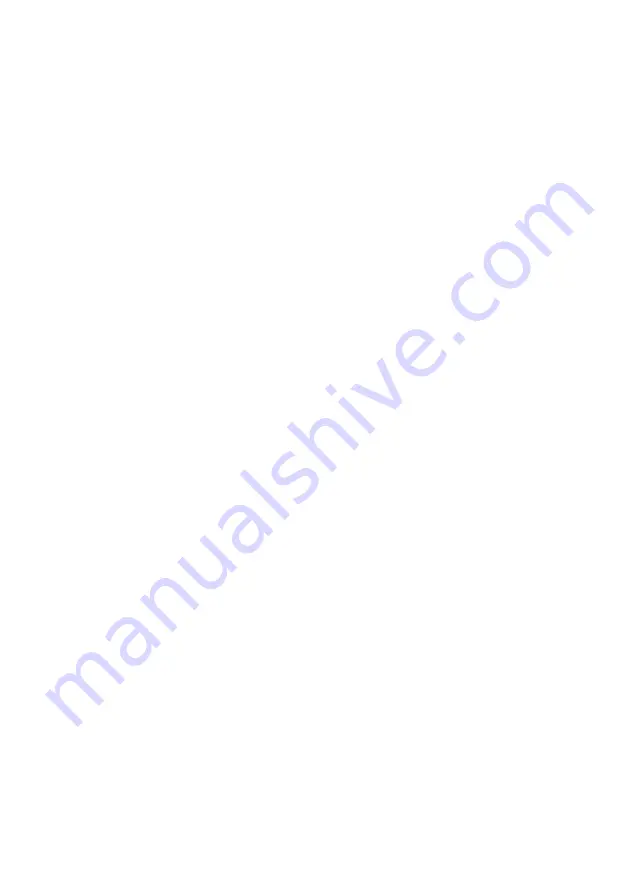
Thoroughly clean off all traces of jointing compound from face edges of the timing cover
and crankcase and then smear both faces with new jointing compound, which leave till
tacky and then re-fit the cover to the crankcase. ("Wellseal" recommended.)
The whole operation of timing the ignition will be found quite simple if the foregoing
instructions are carefully followed.
NOTE—The sparking plug high tension cable for the off-side cylinder is that connected
to the rear pick-up on the magneto.
TO RE-TIME T H E I G N I T I O N (ALTERNATOR T W I N S )
First refer to Electrical Section paragraph "Coil Ignition Standard Twins", to understand
the principle of the distributor, then remove the distributor cover.
Release the clamp bolt securing the distributor, check the contact gap which should be
between ·014 and ·016". (See Electrical Section.)
Position the engine as described for the Magneto Models. If the distributor has been
removed, the distributor shaft with the rotor fitted when replaced should be in the
approximate position as shown in illustration 20, which is the firing position for the
left-hand cylinder. From the near side of the machine turn the rotor in a clockwise
direction (fully advanced position). Whilst retaining this position turn the distributor
body until the contact points are just about to break (see method described for Magneto
Models).
Re-tighten the clamp bolt and re-check the timing.
VALVE TIMING—ALL T W I N MODELS
Inlet valve opens
37° before top dead centre.
Inlet valve closes
77° after bottom dead centre
Exhaust valve opens 73° before bottom dead centre.
Exhaust valve closes 43° after top dead centre.
(Check valve timing with ·012" rocker clearance.)
Upon removing the timing gear cover (secured by 10 screws and 1 nut) and the pump
plate assembly it will be observed the valve timing gears are marked to facilitate correct
assembly. (The nut is not used on standard Twins.)
One tooth gap of the mainshaft small pinion is marked with one centre punch dot and a
tooth of the idle pinion, into which it meshes, is similarly marked. With these two marks
coinciding it will be seen that a tooth on each side of the intermediate pinion is marked
with two centre punch dots which also coincide with a similarly marked tooth gap on
each of the camshaft driving gear wheels.
During assembly it is only necessary to mesh the gears with these various marks coinciding
to ensure correct valve timing.
The dynamo and magneto drive pinions are not marked. The dynamo does not need
"timing" and if, for any reason, the magneto timing has been disturbed, it is re-set as
described later.
Removal of gears
When completely dismantling the engine there is no necessity to remove the small
timing pinion from the crankshaft before splitting the crankcase because the complete
crankshaft can be taken away with the pinion still in position.
If, however, it is desired to remove the pinion without completely dismantling the engine
a special extractor is required (part number 015273). This consists of a nut, threaded
externally and internally. The external threads enable it to be screwed into the threaded
centre of the pinion and the internal threads accommodate a specially designed and
hardered bolt which, upon screwing down, pulls off the pinion. This same tool is used
for the removal of the magneto gear.
The intermediate gear needs no extractor.
42
Summary of Contents for 16
Page 2: ......
Page 21: ...Illustration 8 Cross section of engine showing oil galleries oil passages and release valve 19...
Page 47: ...Illustration 22 Carburetter details in assembly order 45...
Page 59: ...Exploded view of Teledraulic Forks Illustration 29 57...
Page 73: ...71...
Page 74: ...72...
Page 87: ...Illustration 48 Wiring diagram Singles SINGLE CYLINDER MODELS 85...
Page 88: ...Illustration 49 Wiring diagram Magneto Twins TWIN CYLINDER MODELS 86...
Page 89: ...Illustration 50 Wiring diagram Alternator Twins 87...
Page 99: ...Illustration 52 TOOL KIT 97...
Page 103: ......
Page 104: ......