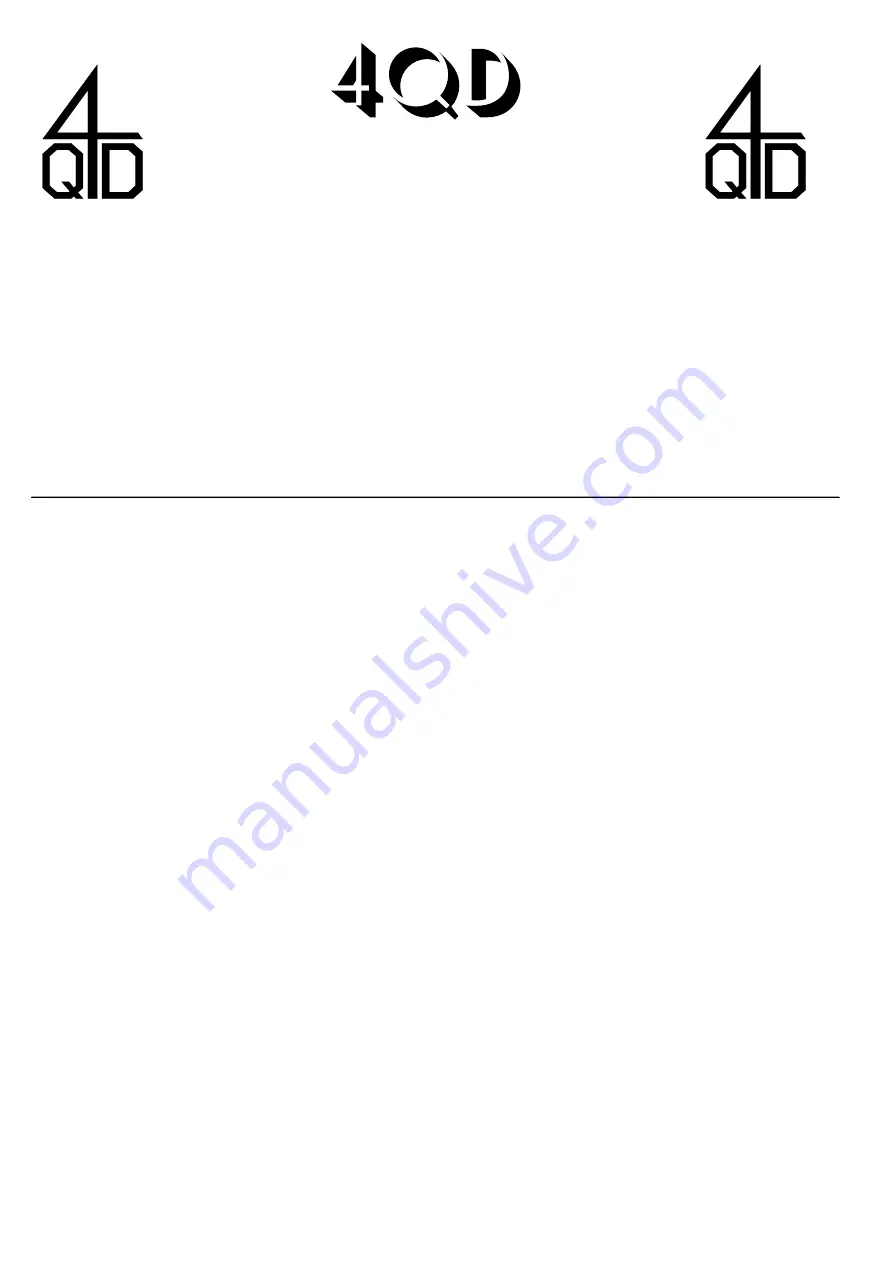
1
Foreword
We have tried to make this manual as readable as we
can. We hope you will read it through before you
start trying to install 4QD’s motor controllers. Even if
you don’t understand everything to start with, reading
it will make you familiar with what we are trying to
say and do. We welcome feedback so if anything is
unclear, please let us know.
This manual describes our standard range of
controllers. Many options are available, so if there
are points you want clarified, or features or
specifications you want altered, please consult the
factory.
In the section ‘Features and Glossary’ we have also
discussed the controllers features, some of the
controls you may wish to fit and the type of
information you may need to make a choice of
controller.
To help to avoid confusion, certain paragraphs are
marked with a bullet ¶. These are more technical
and may be omitted by the less technical reader.
2
Introduction
This manual covers the 4QD-300 series of heavy
duty controllers (up to 300A) for 24v, 36v and 48v
battery operated motors. The controllers are fully
electronic giving control of the motor in all four
‘quadrants’ - that is forward and reverse,
acceleration and braking - so they use no relays or
mechanical switches, increasing reliability. All
internal connections and wiring are rated to carry full
current so the controller continuous ratings are only
limited by external heat dissipation. Moreover the
substantial built-in heatsink is designed so that
additional heat sinking can be added in the unlikely
event it is required.
The controllers use state-of-the-art MOSFET power
transistors which are ‘chopped’ on and off very
rapidly to give ultra-smooth speed control with
minimum losses for best control with minimum
heating in controller, motor and wiring.
During braking a large proportion of the braking
energy is returned to the battery, helping to reduce
battery drain and extend the time between charges.
Power connections are by substantial M8 screw
terminals.
Instruction Manual
4QD series controllers
4QD-300-36 and 4QD-300-48
Issue 17/18 control board and issue 08/09 base board.
Date printed: 27th January 2015
www.4QD.co.uk Email to: [email protected]
“We're in Control”
“We're in Control”
36 Greenfields
Earith
Cambridgeshire
PE28 3QH