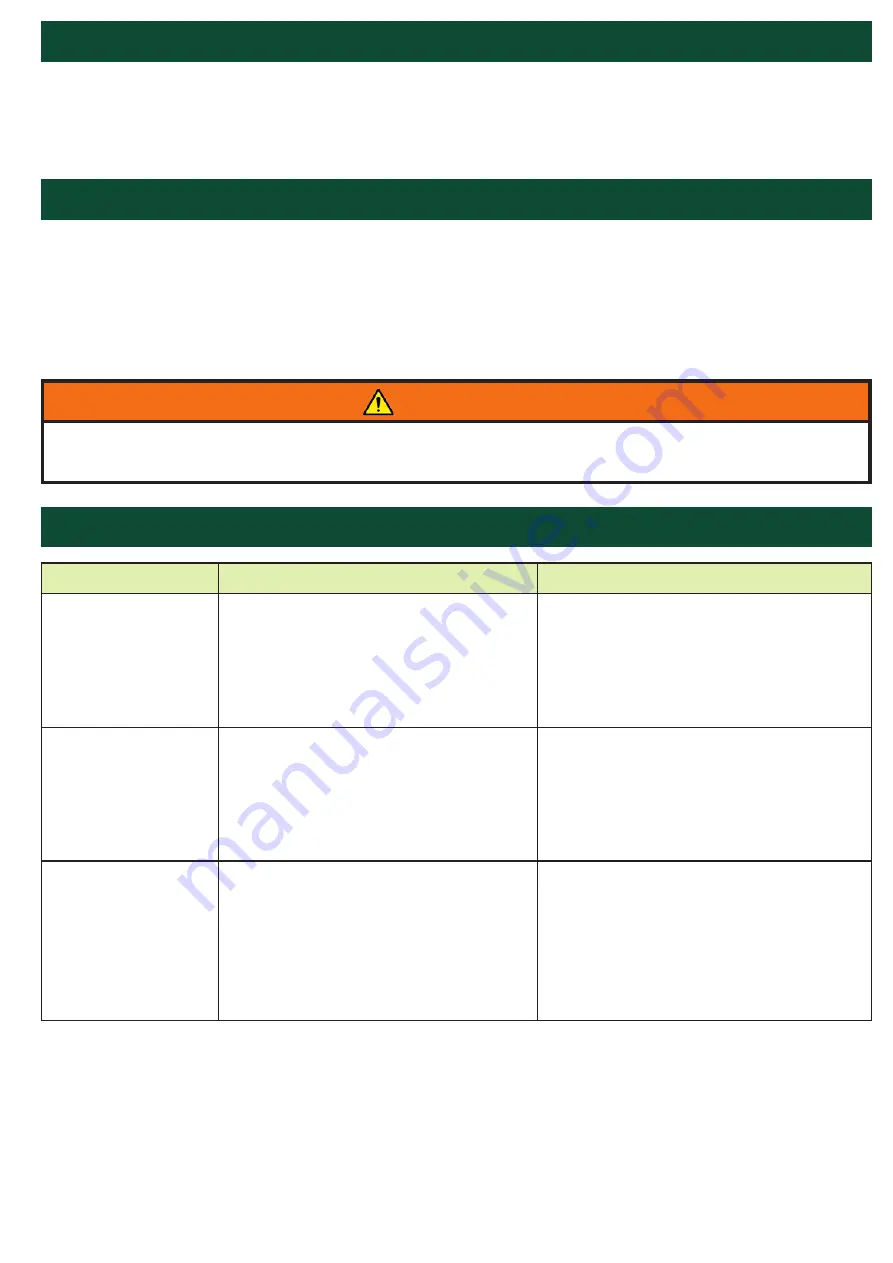
PAGE 17
TROUBLESHOOTING GUIDE
FAULT
CAUSE
REMEDY
LED on alignment
sensor does not
flash
1. Sensor too far away from target
2. Sensor adjustment incorrect
3. Faulty wire connection
4. Object stuck to magnetic face of
the sensor, causing interference
1. Move sensor closer to target
2. Turn sensitivity control clockwise
3. Check wiring
4. Remove object
LED on alignment
sensor flashes
excessively
1. Sensor too close to target
2. Sensor adjustment incorrect
3. Interference in wiring
1. Move sensor away from target
2. Turn sensitivity control counter
clockwise
3. Use shielded cable and rigid
conduit
Sensor will not
calibrate
Wiring issue
1.
Make sure that the YELLOW/
ORANGE wire is connected to the
RED wire
2.
Make sure that the YELLOW/
ORANGE wire is connected to the
correct input on the controller
WARNING
If the system does not alarm as required, then remove the machine from service until the problem
has been diagnosed and corrected.
TESTING AND COMMISSIONING
1. Check that the unit is correctly installed (see standard wiring diagram).
2. Check that the distance between the target and the sensing face of the WDA sensor is within the
minimum distance specified.
3.
Start up machine, the green LED shows the state of the pulsed output and flashes once for each
target detected. The LED should be off when no target is detected, if not, reduce the sensitivity
4. If the sensor is not performing as expected, contact 4B.
SENSOR CALIBRATION
Turn the sensing range adjustment screw fully clockwise while machine is running, the green LED
should flash consistently. Slowly turn the sensing range adjustment screw counter-clockwise until the
flashing becomes irregular. Then turn it slowly clockwise until a regular flashing pattern appears, add an
extra 1/8th turn clockwise for range compensation.