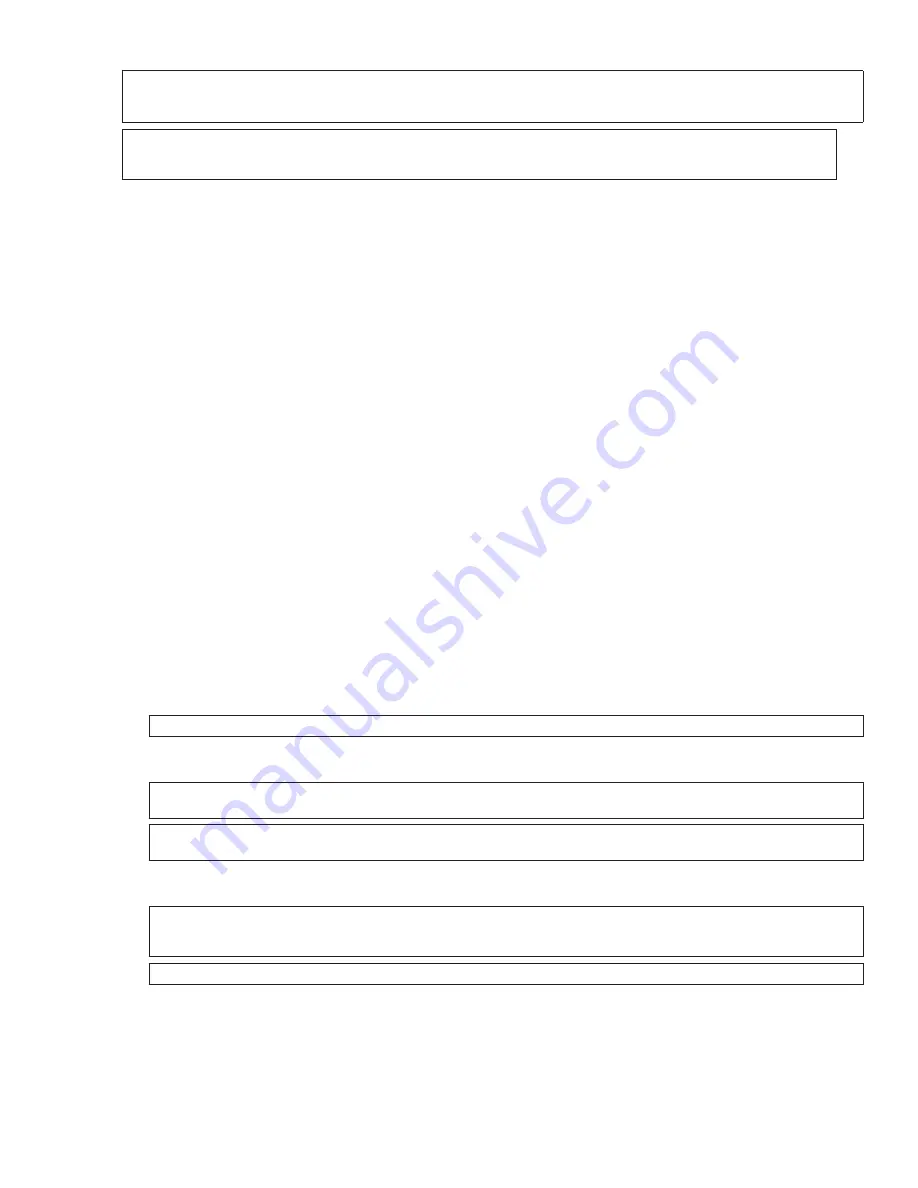
13
3.0 INSTALLATION
;
The Flexiguard SafRig FAS must be installed by a Qualified Person and the installation must be certified by a
Qualified Person as meeting the criteria for a Certified Anchorage, or capable of supporting the potential forces that
could be encountered during a fall.
;
Labels and markings present on the
SafRig FAS should be accessible to the user at all times. If inaccessible
after installation, it is recommended that labels and markings be documented with additional markings near the
installation site.
3.1 PLANNING:
Plan your fall protection system prior to installation of the Flexiguard SafRig FAS Fall Arrest System
(SafRig FAS). Account for all factors that may affect your safety before, during, and after a fall. Consider all requirements,
limitations, and specifications defined in Section 2 and Table 1. Refer to Figure 2 for identification of SafRig system
components.
3.2 SYSTEM SETUP - COUNTERWEIGHT BASE:
Figure 7 illustrates the setup of the SafRig FAS:
1. Install the Offset Arm on the Vertical Mast:
See Figure 7 (1). Bolt the Offset Arm to the Vertical Mast with the
supplied hardware. Torque hardware to 81 N-m (60 ft-lb).
2. Fill the Counterweight Base with Concrete:
See Figure 7 (2A). Fill the Counterweight Base with 4,000 psi
concrete. (Contact 3M Technical Services for specific concrete requirements).
3. Install Leveling Jacks:
See Figure 7 (3A). If the optional Leveling Jack Kit (8530563) was purchased with your
Counterweight Base, install the Leveling Jacks on the Counterweight Base as instructed in the Installation Instructions
included with the Leveling Jack Kit.
3.3 SYSTEM SETUP - STEEL OUTRIGGER BASE:
Figure 7 illustrates the setup of the SafRig FAS:
1. Install the Offset Arm on the Vertical Mast:
See Figure 7 (1). Bolt the Offset Arm to the Vertical Mast with the
supplied hardware. Torque hardware to 81 N-m (60 ft-lb).
2. Assemble Steel Outrigger Base:
See Figure 7 (2B). Position the center section of the base. Set the two outriggers
in place and attach with the supplied hardware. Torque hardware to 81 N-m (60 ft-lb).
3. Drive Over Guards:
See Figure 7 (3B). Position the drive over guards. Attach with the supplied hardware. Torque
hardware to 61 N-m (45 ft-lb).
3.4 INSTALL THE MAST:
Figure 8 illustrates installation of the assembled Vertical Mast and Offset Arm on the Counterweight
Base.
1. Lubricate the Hitch Ball:
Liberally grease the Hitch Ball on the Hitch Ball Post.
2. Position the Vertical Mast over the Base:
Lift the assembled Vertical Mast with a Lifting Sling and Forklift or
Crane. Position the Vertical Mast so the Mounting Socket in the bottom of the Vertical Mast is directly over the Hitch
Ball Post.
3. Lower the Vertical Mast onto the Base:
Lower the Vertical Mast onto the Base until the Hitch Ball fully seats in the
Vertical Mast mounting socket.
3.5 TRANSPORT AND POSITION THE SYSTEM:
Transport and position the SafRig FAS as illustrated in Figure 9:
1. Rotate and lock the Mast and Arm:
Remove the Rotation Lock Pin (A). Rotate the Vertical Mast and Offset Arm (B)
for best clearance during transport and then reinsert the Rotation Lock Pin.
;
Never transport the system without the Rotation Lock Pin inserted.
2. Transport the System:
Transport the SafRig FAS to the desired work location using a Forklift or Pallet Jack and the
Lifting Channels.
;
Do not transport at speeds exceeding 8 kph (5 mph). Never transport the system on slopes greater than 10°.
Excessive speeds or slopes may cause system and transport vehicle tip-overs resulting in serious injury or death.
;
When transporting the SafRig System, be aware of overhead obstructions and electrical hazards which may
result in serious injury or death.
3. Place the System:
Place the SafRig FAS near the work area on a surface with 1° or less of slope. Use the Slope
Indicators on the Counterweight Base to verify that the system is level.
;
Leveling Jacks may be installed in the Leveling Jack Mounts on the Counterweight Base for purposes of leveling
the system on a surface that is not level. Extend the Leveling Jacks until they contact the ground. Crank the
Leveling Jacks up or down as needed until all Slope Indicators indicate less than 1° of slope.
;
Personnel shall not be attached to the SafRig FAS while it is being positioned.
4. Rotate and lock the Mast and Arm:
Rotate the Vertical Mast and Offset Arm to the desired work position and then
set the Rotation Limits. The Mast can be locked at 11° rotation increments with the Rotation Lock Pin Mechanism or
allowed to rotate through a range defined by two Rotation Limiters:
• No Rotation (A):
Insert the Rotation Lock Pin through the inside Pin Hole and aligned hole in the Rotation Plate
to prevent the Jib Boom from rotating.
• Rotation Range (B):
Insert the Rotation Lock Pin through the outside Pin Hole and then move the Rotation
Limiters to the desired limits on the Rotation Plate. Insert the Rotation Limiter Pegs through the desired holes in
the Rotation Plate to define the rotation range.
Summary of Contents for DBI SALA FlexiGuard SafRig
Page 2: ...2 2 B A E F G G H G G F C I I I I K K K J J J D L L L L N M O ...
Page 4: ...4 7 1 2A 2B 3B 8 1 2 3 3A ...
Page 5: ...5 9 1 2 3 1 4 Ï ÏóÏ A B A B ...
Page 6: ...6 10 A A ...
Page 8: ...8 ...