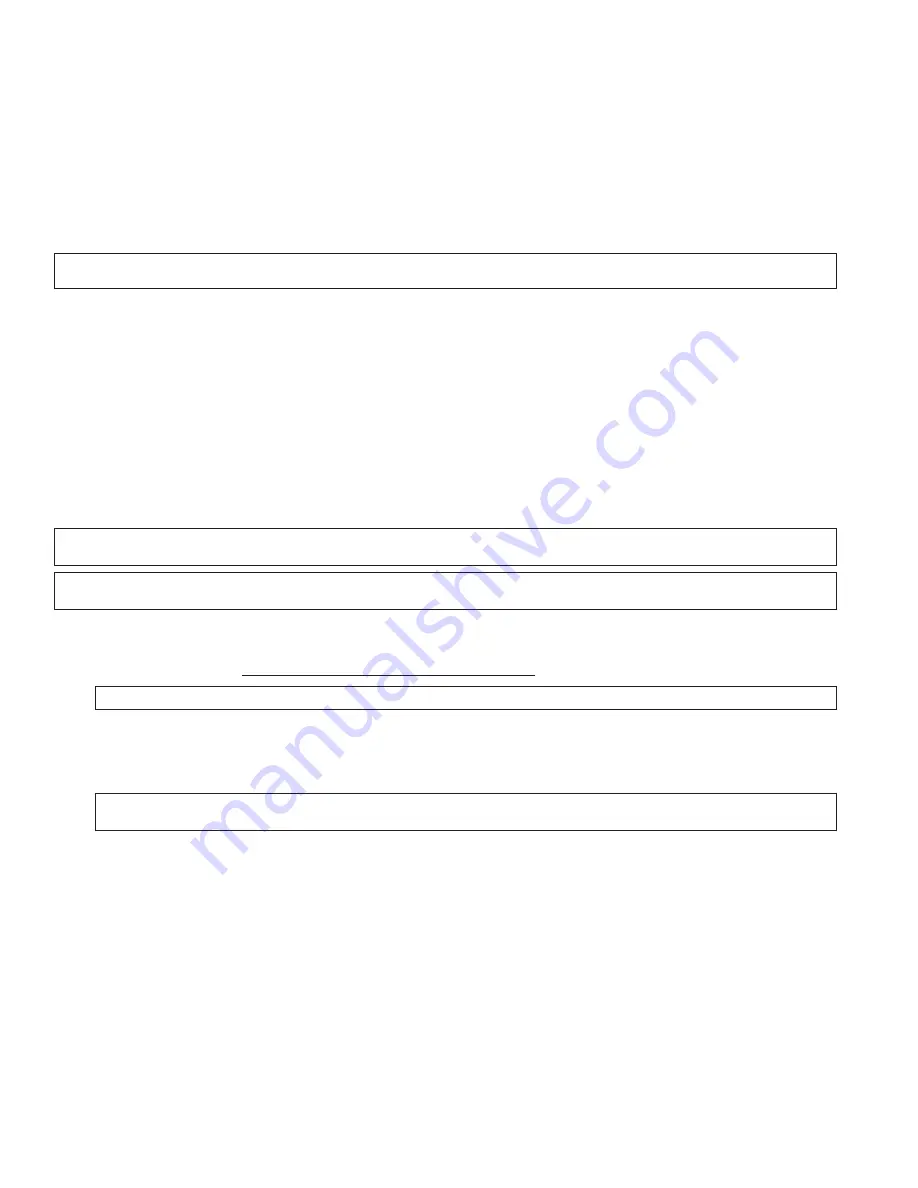
16
4.0 USE
4.1
BEFORE EACH USE:
Verify that your work area and Fall Protection system meet all criteria defined in these instructions.
Verify that a formal Rescue Plan is in place. Inspect the product per the points of the
“Inspection and Maintenance Log”
.
If inspection reveals an unsafe or defective condition, or if any doubt should arise about its condition for safe use, remove
the product from service immediately. Clearly tag the system “DO NOT USE”. See Section 5 for more information.
4.2
MAKING CONNECTIONS:
When using a hook to connect to an anchorage or when coupling components of the system
together, ensure roll-out cannot occur. Roll-out occurs when interference between the hook and mating connector causes
the hook gate to unintentionally open and release. Self-locking snap hooks and carabiners should be used to reduce the
possibility of roll-out. Do not use hooks or connectors that will not completely close over the attachment object. See
subsystem manufacturer’s instructions for more information on making connections.
5.0 INSPECTION
;
After equipment has been removed from service, it may not be returned to service until a Competent Person confirms in
writing that it is acceptable to do so.
5.1
INSPECTION FREQUENCY:
The product shall be inspected by the user before each use and, additionally, by a
Competent Person other than the user at intervals of no longer than one year. A higher frequency of equipment use
and harsher conditions may require increasing the frequency of Competent Person inspections. The frequency of these
inspections should be determined by the Competent Person per the specific conditions of the worksite.
5.2
INSPECTION PROCEDURES:
Inspect this product per the procedures listed in the
“Inspection and Maintenance Log”
.
Documentation of each inspection should be maintained by the owner of this equipment. An inspection and maintenance
log should be placed near the product or be otherwise easily accessible to users. It is recommended that the product is
marked with the date of next or last inspection.
5.3 DEFECTS:
If the product cannot be returned to service because of an existing defect or unsafe condition, then the
product must be either destroyed or sent to 3M for replacement.
5.4
PRODUCT LIFE:
The functional life of the product is determined by work conditions and maintenance. As long as the
product passes inspection criteria, it may remain in service.
6.0 MAINTENANCE, SERVICE, and STORAGE
;
Equipment that is in need of maintenance or scheduled for maintenance should be tagged “DO NOT USE”. These
equipment tags should not be removed until maintenance is performed.
;
Do not clean or disinfect the product by any method other than described in the following cleaning instructions. Other
methods may have adverse effects on the product or user.
6.1 CLEANING:
3M Full Body Harnesses must be cleaned in accordance with 3M instructions. To clean the harness, wash in
a mild, bleach-free detergent and then rinse. The harness should afterwards be hung to air-dry. Water used for cleaning
and temperatures used to air-dry must never exceed 130
°
F (54.4
°
C). For more information, please refer to the technical
bulletin on our website:
http://www.3M.com/FallProtection/WebCleaning
;
For any questions about cleaning procedures, please contact 3M Technical Services.
6.2 SERVICE:
This equipment cannot be repaired. Upon permanent removal from service, cut the harness straps or otherwise
render the harness unusable before disposing of it.
6.3
STORAGE AND TRANSPORT:
Store and transport the product in a cool, dry, clean environment out of direct sunlight.
Avoid areas where chemical vapors may exist. Thoroughly inspect components after extended storage.
;
It is recommended that the user limit exposure of the product to UV light. Prolonged exposure to UV light could
cause webbing material to degrade at a faster rate.