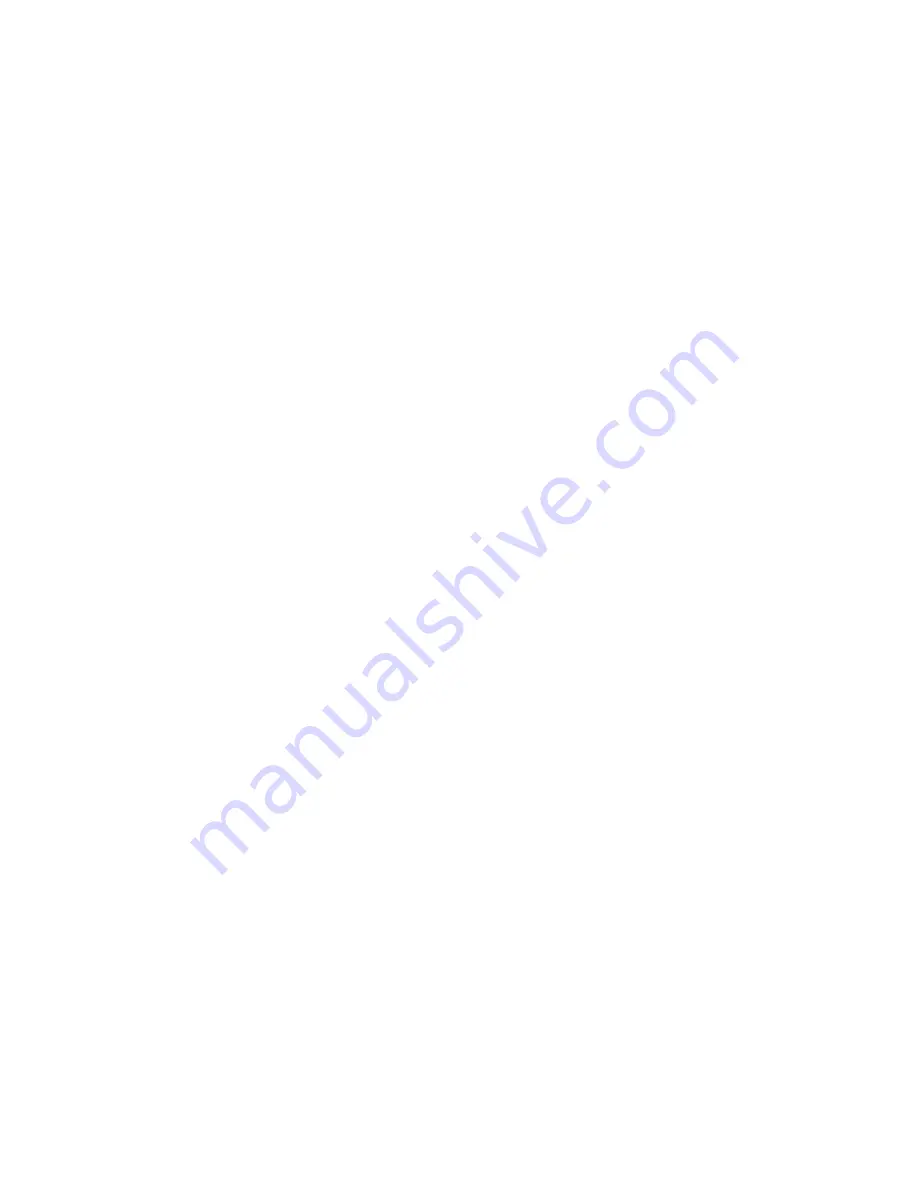
14
Product Use:
All statements, technical information and recommendations contained in this document are based up on
tests or experience that 3M believes are reliable. However, many factors beyond 3M’s control can affect the use and
performance of a 3M product in a particular application, including the conditions under which the 3M
product is used and the time and environmental conditions in which the product is expected to perform. Since these
factors are uniquely within the user’s knowledge and control, it is essential that the user evaluate the 3M product to
determine whether it is fit for a particular purpose and suitable for the user’s method of application.
Warranty and Limited Remedy:
3M warrants this tool against defects in workmanship and materials under normal
operating conditions for One (1) year from the date of purchase. 3M MAKES NO OTHER WARRANTIES, EXPRESS OR
IMPLIED, INCLUDING, BUT NOT LIMITED TO, ANY IMPLIED WARRANTY OF MERCHANTABILITY OR FITNESS FOR A
PARTICULAR PURPOSE OR ANY IMPLIED WARRANTY ARISING OUT OF A COURSE OF DEALING, CUSTOM OR USAGE OF
TRADE. User is responsible for determining whether the 3M tool is fit for a particular purpose and suitable for user’s
application. User must operate the tool in accordance with all applicable operating instructions, safety precautions, and
other procedures stated in the operating manual to be entitled to warranty coverage. 3M shall have no obligation to repair
or replace any tool or part that fails due to normal wear, inadequate or improper maintenance, inadequate cleaning,
non-lubrication, improper operating environment, improper utilities, operator error or misuse, alteration or modification,
mishandling, lack of reasonable care, or due to any accidental cause. If a tool or any part thereof is defective within this
warranty period, your exclusive remedy and 3M’s sole obligation will be, at 3M’s option, to repair or replace the tool or
refund the purchase price.
Limitation of Liability:
Except where prohibited by law, 3M and seller will not be liable for any loss or damage arising
from the 3M product, whether direct, indirect, special, incidental or consequential, regardless of the legal theory
asserted, including warranty, contract, negligence or strict liability.
Submitting a Warranty Claim:
Contact your dealer when submitting a warranty claim in accordance with the restrictions
listed above. Please note that all warranty claims are subject to manufacturer’s approval. Be sure to keep your
sales receipt in a safe place. This must be submitted when filing a warranty claim, within One (1) year from the date of
purchase.
Product Repair after Warranty Has Expired
3M does not offer repair service for product out of warranty.
3M
Abrasive Systems Division
3M Center, Building 223-6N-02
St. Paul, MN 55144-1000
www.3M.com/abrasives
© 3M 2008
3M and Hookit are trademarks of 3M Company
34-8701-9414-8
Summary of Contents for Buffer 8125
Page 13: ...13 ...