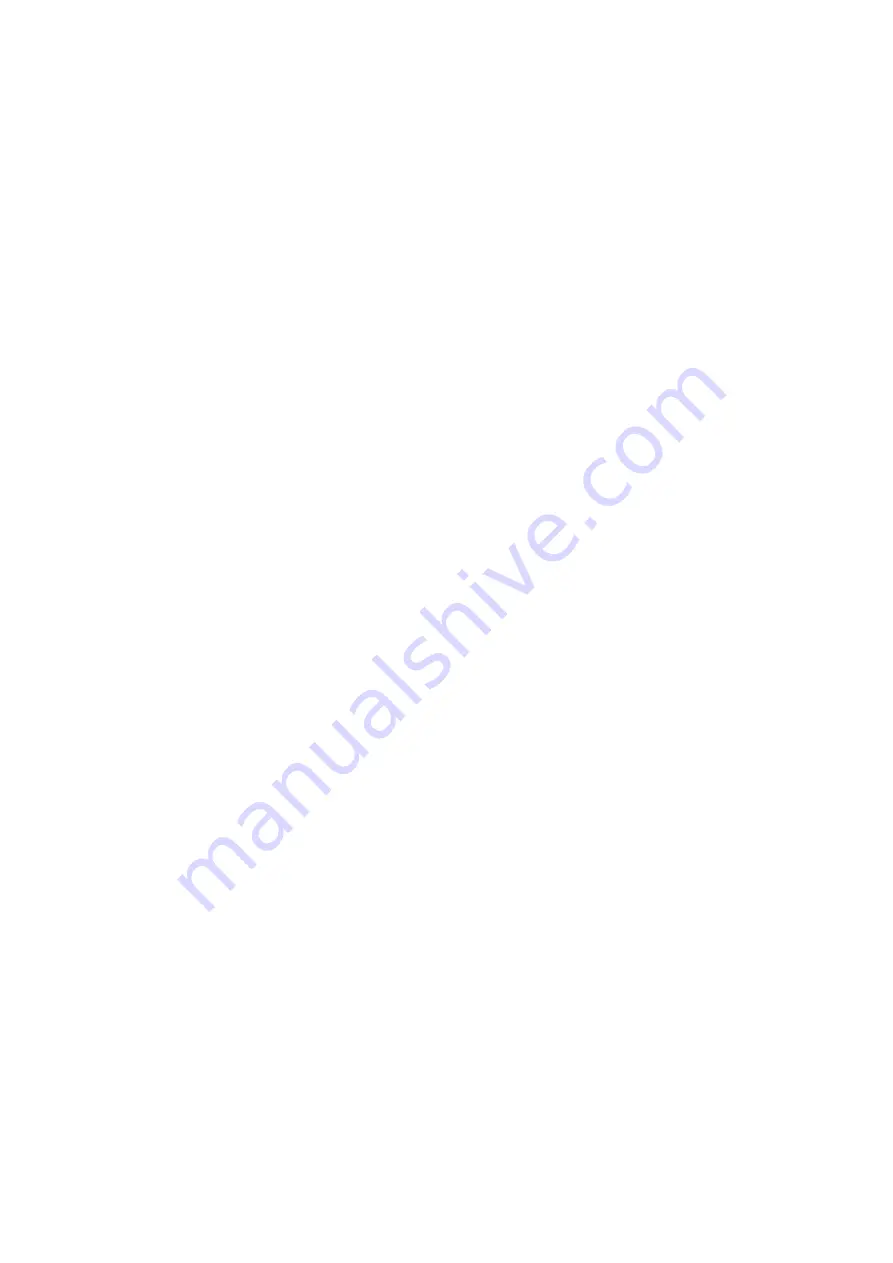
16
3D SYSTEMS, INC
.
PN:80-D48 REV A
RISK RELATING TO GAS BOTTLES
Whenever necessary, compressed air bottles are to be stored outside the buildings in an enclosed and ventilated shelter .
The bottles must be placed vertically in the racks attached to the walls .
Any gas bottles that cannot be attached and that have to be used close to the equipment, must be placed on a suitable
support that makes it impossible for them to tip over .
Remember that there is a risk of asphyxia in small, poorly ventilated, rooms .
Furthermore, an excess-flow shut-off valve must be fitted to the regulator output, upstream of the gas pipe. This valve
starts to operate when the flow exceeds approx. 10% of the flow value used under normal operating conditions.
CHEMICAL RISK
These risks can have several sources:
Laser – material interaction: in this case, the emission, to a greater or lesser extent, is caused by the vaporization and
decomposition of materials during a laser procedure (emission of fumes, aerosols and dust, some of which may be
carcinogenic),
Use of gas to control the sintering atmosphere (Argon Ar, Nitrogen N) – inert gas: anoxia .
The printer rejects filtered inert gases (HEPA filters: 99,97 % of particles dimensions higher than 0,3 µm are filtered). A
connection or exit towards the outside is only necessary if the flow of the premises is lower than 50 m
3
/hour (29 .43 cfm) .
LASER SAFETY
The DMP system contains a fiber laser. The laser itself is designated Class IV. Very brief exposure to a direct—or specularly
or diffusely reflected—laser beam can cause significant burns or eye damage. It can also be a fire hazard.
During normal operations of the DMP system, the laser beam path is wholly contained within the machine . This makes the
entire machine a Class I Laser System . That means the DMP system does not produce damaging emissions under normal
operations .
LASER SAFETY CLASSIFICATIONS
Class I and Class IV are designations established by the U . S . Department of Health and Human Services, Public Health
Service, Food and Drug Administration, Center for Devices and Radiological Health (CDRH), and by IEC 60825 (the
International Electrotechnical Commission’s
Radiation Safety of Laser Products, Equipment Classification Requirements, and
User’s Guide
) . The Class I and Class IV laser designations also comply with DIN VDE 0837/02 .86+A1/07 .90 . You can read more
about laser safety and classifications in ANSI Z136.1-1993 (the American National Standards Institute standard for the safe
use of lasers) .
BIOLOGICAL RISK
The main risk is to the eyes . The laser beam presents a danger in two ways:
•
Direct radiation, where the eyes are in the beam axis . Do not look directly into laser during power burn .
•
Reflected radiation, where the beam hits a surface that does not fully absorb it, results in partial reflection of the
emitted beam .
Specular reflections (due to reflective objects) present exactly the same risk as direct radiation, as not only are they
insidious, but they also contain up to 90% or more of the initial energy content .
Effects due to laser radiation depend on the wavelength; in the near infrared range (700 to 1400 nm), the cornea and lens
are highly transparent to laser radiation, which thus reaches the retina. If the eye receives a significant energy density, the
laser beam may cause small, irreversible lesions with extremely variable consequences depending on the location of the
affected area . This can result in the formation of a hole in the retina with no adverse effect on vision, or in a blind area (or
black spot) due to damage to the macula or even in almost total loss of vision when the fovea is affected .
The laser safety window conforms to standard CE EN207 allowing operators to observe interaction of laser and material
while avoiding the risk of burns and loss of visual acuity .
MECHANICAL RISK
Any machine-tool with digitally-controlled movements are likely to be susceptible to rapid changes in position .
This results from inadvertent movements of the motorized axes:
•
Sintering axis,
•
Supplying axis,
•
Layering system .
And from inadvertent movements of actuators:
•
Opening/closing of the airlock,
•
Scraper .