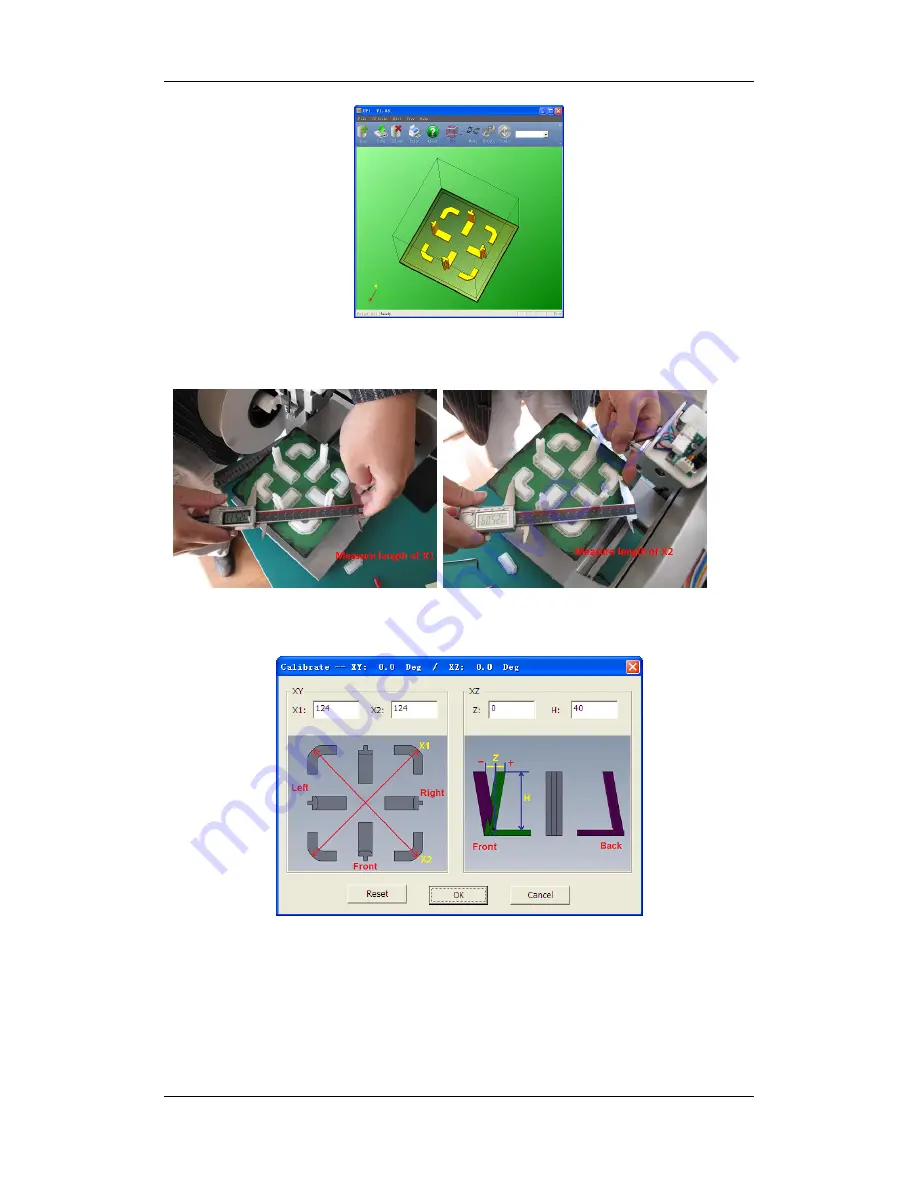
3.Operation
UP! 3D Printer User Manual
34
After the calibration model is printed, measure the X1 and X2 length, as shown in the pictures
below.
Open the “Calibrate” box form the “3D Print” menu and enter the measured X1 and X2 values
into the appropriate boxes.
Next, take down the Front Centre ‘L’ shaped component, and measure its deviation. Put the exact
value into the Z box. If it deviates to the right side, the value to be put into the Z box will be a
positive value. If the deviates to the left, the value to put into the Z box will be a negative value.