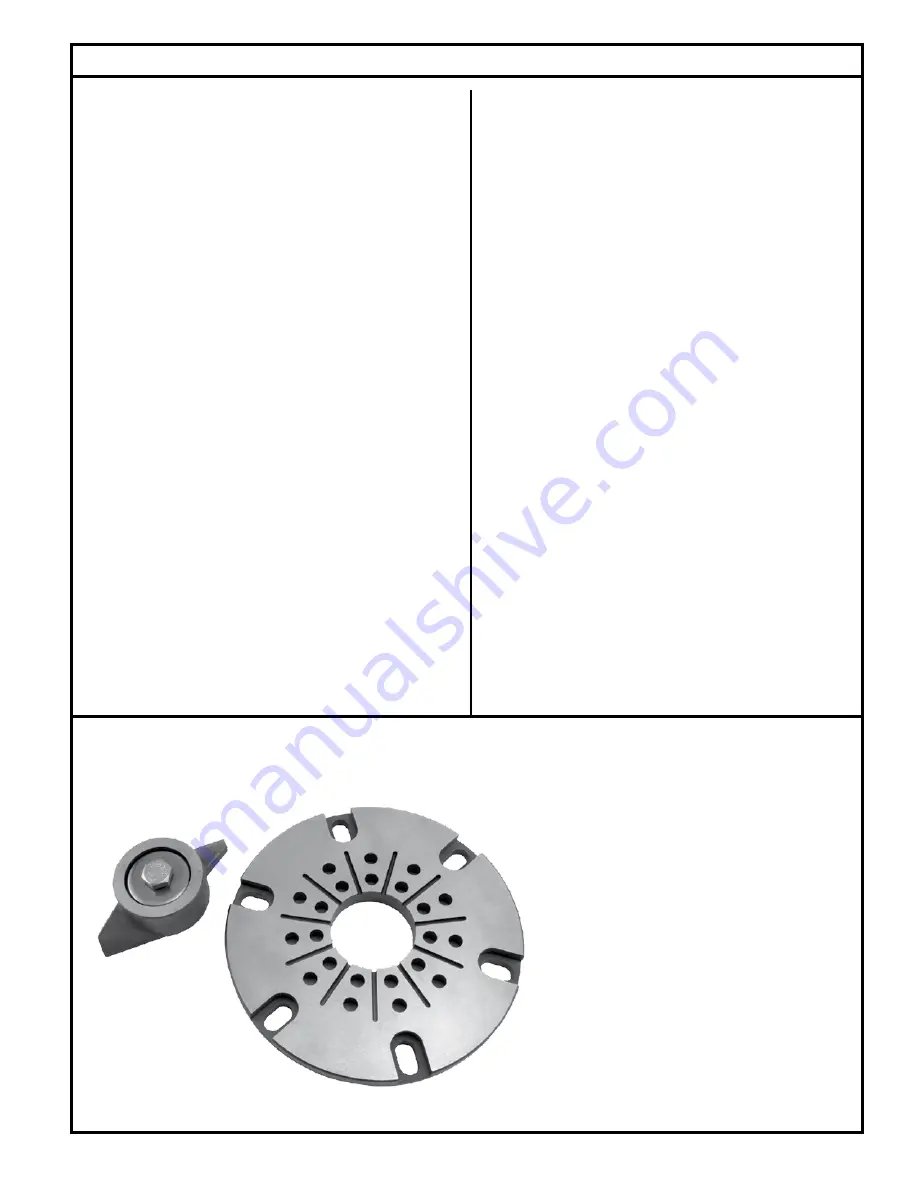
11
© Copyright 2017 Zoeller
®
Co. All rights reserved.
Cutter Maintenance
1.
All power circuits must be disconnected and locked out
before any attempts are made at servicing.
The cutter and
disc can be removed and sharpened by grinding the cutting
faces. Both cutter and disc must be removed from the pump.
Removal of these parts can be accomplished in the field by
removing pump from the sump and positioning horizontally
to access the intake of the pump. If seals or other repairs are
required, the pump must be totally removed and serviced in
a shop by a qualified pump technician or authorized service
center.
2. Remove the three countersunk screws on the ring.
3. Thoroughly clean the cutter and disc assembly. Tilt pump
back to the vertical position to make certain the end play has
been removed. Check and record the clearance between
the cutter and disc with a feeler gage. The correct running
clearance is between 0.004" and 0.008".
4. With pump in horizontal position, heat the hex head bolt in
the center of the cutter with a propane torch. The bolt must
be heated to 350° F to soften the thread lock sealer on the
bolt for ease of removal. Remove the bolt by turning in a
counterclockwise rotation. It will be necessary to use a wood
block to prevent the cutter from turning while removing the
bolt. Pull cutter from the shaft and remove the spacer shims
located behind the cutter.
5. Remove the six cap screws holding the disc and remove disc
from the pump.
6. The disc and cutter can be replaced with new service parts
or resurfaced by grinding. Resurfacing is accomplished by
surface grinding both disc and cutter to a 32 micro finish. Do
not attempt grinding in the field. Send parts to a qualified
machine shop or return to the factory for repair. The disc,
cutter and shims are a matched set. Keep parts together.
Measure disc before and after resurfacing with micrometer
and record measurements.
7. After resurfacing, the disc and cutter must be flat within 0.001".
If the disc has been surface ground, it will be necessary to
remove shims to compensate for the material removed from
the disc. As a starting point, remove shims of the same thick-
ness as the amount machined from the cutter disc (step 6
above). Final running clearance must be between 0.004”
and 0.008”. Be sure pump is in vertical position and all end
play has been removed before measuring.
8. Clean bottom of pump where disc is located and replace
disc and retainer screws. Torque to 63-67 in-lbs. Replace
cutter with the correct shims. Install washer and torque hex
head bolt to 71-75 in.-lbs. Apply Loctite 262 thread-lock
sealant or equal to bolt threads prior to insertion. Check
running clearance with pump in vertical position to remove
end play. Clearance must be between 0.004" and 0.008" to
obtain efficient grinding when pump is put back in service.
9. Replace six cap screws.
10. Check the oil in the motor housing before reinstalling. Contact
the factory if the oil has a milky appearance or burnt smell.
The level should be even with the fill plug when pump is in
the upright position. Add oil if required. Use insulating oil
supplied by the factory.
FIGURE 6.
To remove cutter: Heat the center bolt to 350°F
to loosen Loctite
®
thread sealant.
Grind the Cutter and Disc seen here to a 32
microfinish. Surfaces must be flat to within 0.001"
T.I.R. Gap must be between 0.007" and 0.012" on
these parts.