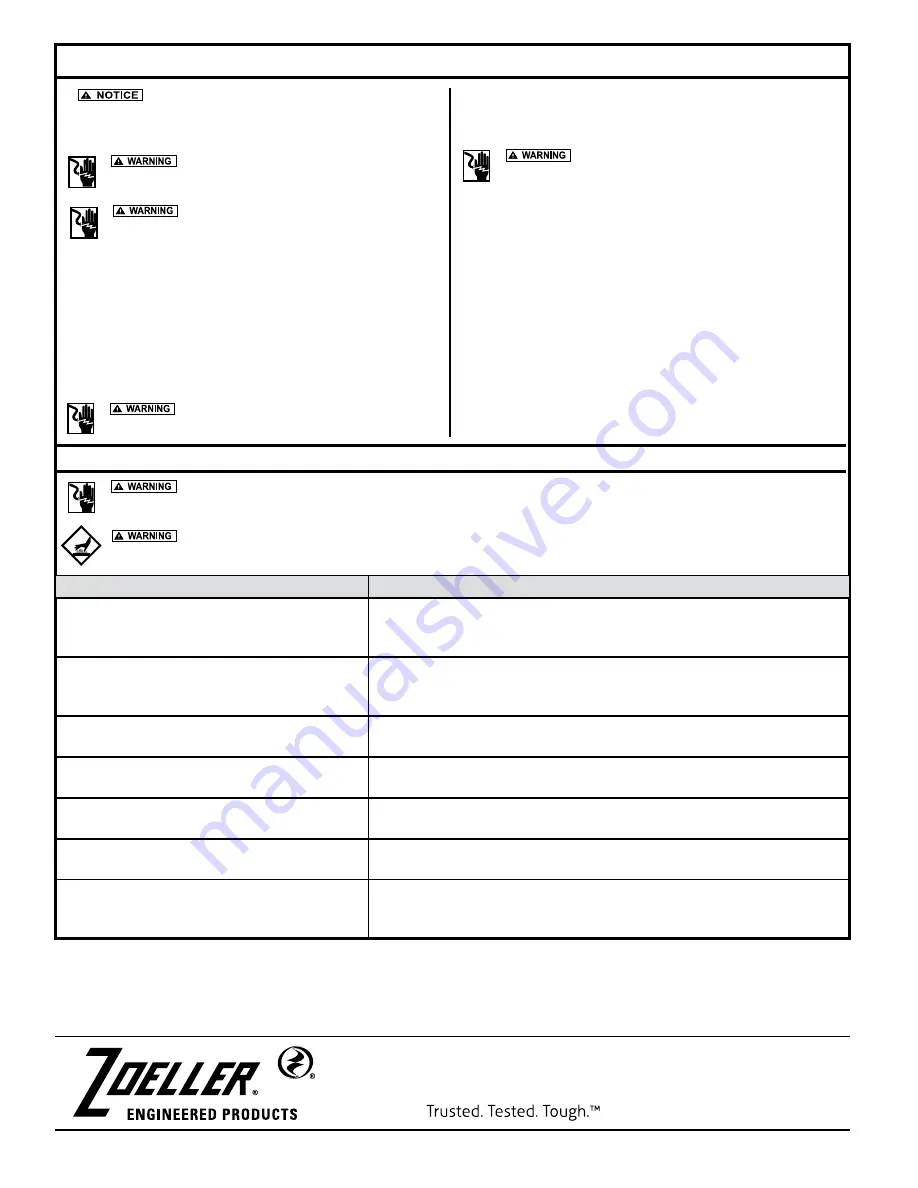
12
© Copyright 2018 Zoeller
®
Co. All rights reserved.
General Maintenance
Repair and service should be performed by a Zoeller
Pump Company Authorized Service Station only.
SAFETY PROCEDURES
For your protection, always disconnect pump
and panel from its power source before handling.
Never enter the basin until it has been properly
vented and tested. Any person entering a basin should be
wearing a harness with safety rope extending to the surface
so that they can be pulled out in case of asphyxiation. Sewage water
gives off methane and hydrogen sulfide gases, both of which can be
highly poisonous.
Installation and checking of electrical circuits and hardware should be
performed by a qualified electrician.
Pump is never to be lifted by power cord.
Unit must be cleaned and disinfected, inside the
pumping chamber and all exterior surfaces, prior to servicing.
GENERAL SYSTEM INSPECTION
Before the system is placed into operation, it should be inspected by
a qualified technician.
Wiring and grounding must be in accordance
with the National Electrical Code and all applicable local codes
and ordinances.
LUBRICATION PROCEDURES
No lubrication is required.
If pumps are to be stored for more than six months, refer to short term
storage procedure in the Operation section.
PREVENTIVE MAINTENANCE
Preventive maintenance is recommended to ensure a long service
life from the product. Provided is a suggested maintenance schedule.
Every six months:
• Check for proper and unobstructed float operation.
• Listen for proper check valve operation.
Every 5 years or 10,000 hours of operation:
• Remove pump, inspect and service using a Zoeller rebuild kit.
• Flush and clean basin.
Service Checklist
Electrical precautions. Before servicing a grinder pump, always shut off the main power circuit. Make sure you are wearing
insulated protective sole shoes and not standing in water. Under flooded conditions, contact your local electric company or a qualified
licensed electrician for disconnecting electrical service to the pump prior to removal.
Grinder pumps contain oil which becomes pressurized and hot under operating conditions. Allow 2-1/2 hours after shut
down before servicing pump.
Condition
Common Causes
A. Pump will not start or run.
Blown panel or circuit breaker fuse, low voltage, thermal overload open, defective capacitor
circuit, cutter or impeller clogged, float switch held down or defective, incorrect wiring in
control panel, water in cap assembly.
B. Motor overheats and trips on overload.
Incorrect voltage, impeller or cutter blocked, negative head (discharge lower than intake
of pump). Defective “off” float. Pump runs continuously at low water level. Low oil level
in motor shell.
C. Pump will not shut off.
Air lock, debris under float assembly, defective switch, incoming sewage exceeds
capacity of pump.
D. Pump operates but delivers little or no water.
Intake clogged with grease or sludge, pump air locked (clear vent hole), low or incorrect
voltage, clogged discharge line, operating near shut-off head.
E. Pump starts and stops too often.
Check valve stuck open or defective. Sump pit too small to handle incoming sewage.
Level control out of adjustment. Thermal overload tripping.
F. Large red flashing light comes on at control box.
High water in pit. Check pump for clogging, or overload trip. On single phase pumps,
check the start capacitor in the control panel. See “A” and “D” above.
G. Grease and solids accumulate in pit around pump. Break up solids and run pump with water running into the pit. Allow level to lower to
the pump intake. Continue until solids are cleared from the pit. Do not drain kitchen
grease down the sink.
MAIL TO:
P.O. BOX 16347 • Louisville, KY 40256-0347
SHIP TO:
3649 Cane Run Road • Louisville, KY 40211-1961
(502) 778-2731 • 1 (800) 928-PUMP •
FAX
(502) 774-3624
visit our web site:
zoellerengprod.com