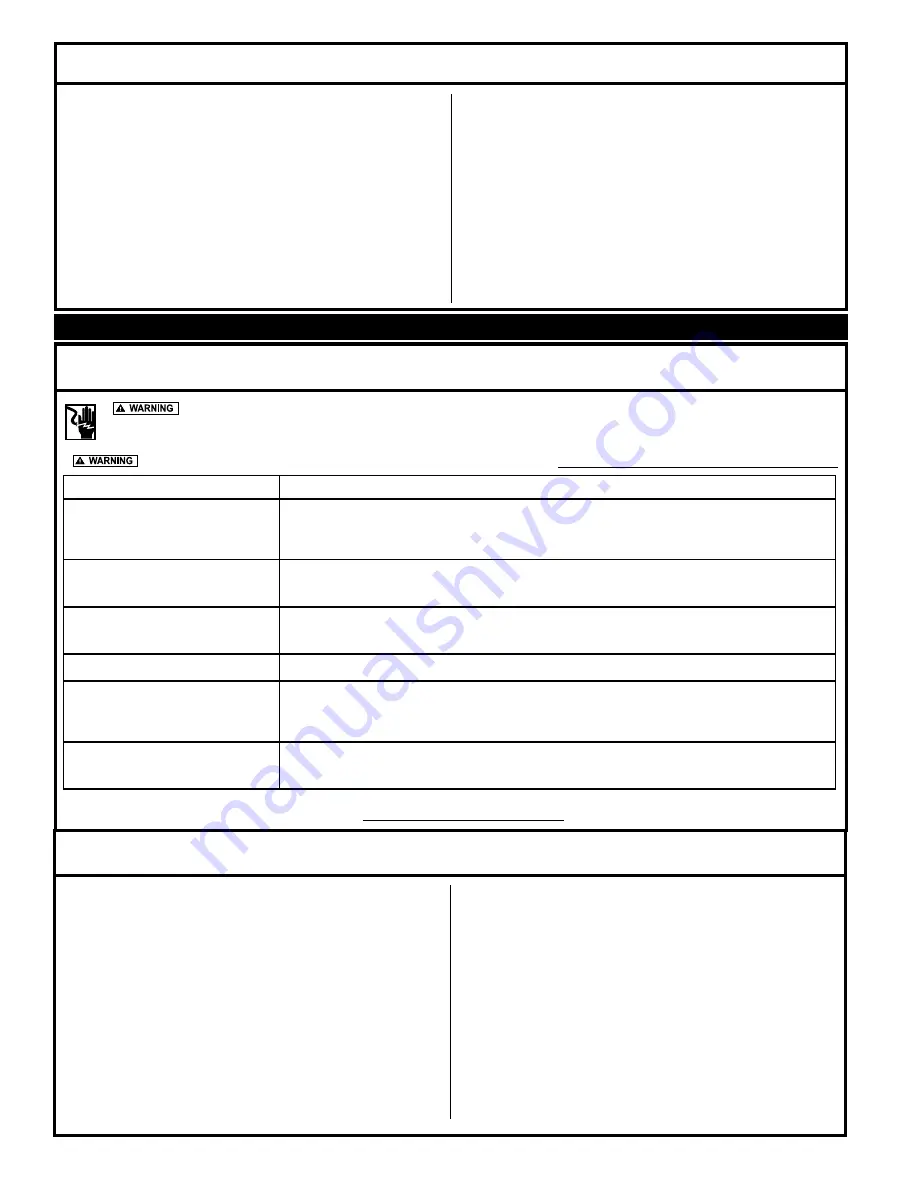
2
© Copyright 2015 Zoeller
®
Co. All rights reserved.
in lieu of all other warranties expressed or implied; and we do not authorize any representative or
other person to assume for us any other liability in connection with our products.
Contact Manufacturer at, 3649 Cane Run Road, Louisville, Kentucky 40211, Attention: Customer
Service Department to obtain any needed repair or replacement of part(s) or additional information
pertaining to our warranty.
MANUFACTURER EXPRESSLY DISCLAIMS LIABILITY FOR SPECIAL, CONSEQUENTIAL OR
INCIDENTAL DAMAGES OR BREACH OF EXPRESSED OR IMPLIED WARRANTY; AND ANY
IMPLIED WARRANTY OF FITNESS FOR A PARTICULAR PURPOSE AND OF MERCHANTABILITY
SHALL BE LIMITED TO THE DURATION OF THE EXPRESSED WARRANTY.
Some states do not allow limitations on the duration of an implied warranty, so the above limitation may
not apply to you. Some states do not allow the exclusion or limitation of incidental or consequential
damages, so the above limitation or exclusion may not apply to you.
This warranty gives you specific legal rights and you may also have other rights which vary from
state to state.
LIMITED WARRANTY
Manufacturer warrants, to the purchaser and subsequent owner during the warranty period, every
new product to be free from defects in material and workmanship under normal use and service,
when properly used and maintained, for a period of three years from the date of original manufacture.
Parts that fail within the warranty period, that inspections determine to be defective in material or
workmanship, will be repaired, replaced or remanufactured at Manufacturer's option, provided however,
that by so doing we will not be obligated to replace an entire assembly, the entire mechanism or the
complete unit. No allowance will be made for shipping charges, damages, labor or other charges
that may occur due to product failure, repair or replacement.
This warranty does not apply to and there shall be no warranty for any material or product that has been
disassembled without prior approval of Manufacturer, subjected to misuse, misapplication, neglect,
alteration, accident or act of God; that has not been installed, operated or maintained in accordance
with Manufacturer's installation instructions; that has been exposed to outside substances including
but not limited to the following: sand, gravel, cement, mud, tar, hydrocarbons, hydrocarbon derivatives
(oil, gasoline, solvents, etc.), or other abrasive or corrosive substances, wash towels or feminine
sanitary products, etc. in all pumping applications. The warranty set out in the paragraph above is
If the above checklist does not uncover the problem, consult the factory - Do not attempt to service or otherwise disassemble pump. Service must be
performed by Zoeller Authorized Service Stations. Go to www.zoellerpumps.com/servicestations to find the Authorized Service Station in your area.
ELECTRICAL PRECAUTIONS-
Before servicing a pump, always shut off the main power breaker and then unplug the pump - making sure you are
wearing insulated protective sole shoes and not standing in water. Under flooded conditions, contact your local electric company or a qualified licensed electrician for
disconnecting electrical service prior to pump removal.
Submersible pumps contain oils which becomes pressurized and hot under operating conditions -
allow 2½ hours after disconnecting before attempting service.
SERVICE CHECKLIST
CONDITION
COMMON CAUSES
A. Pump will not start or run.
Check fuse, low voltage, overload open, open or incorrect wiring, open switch, impeller or seal bound mechanically,
defective capacitor or relay when used, motor or wiring shorted. Float assembly held down. Switch defective,
damaged, or out of adjustment.
B. Motor overheats and trips overload
or blows fuse.
Incorrect voltage, negative head (discharge open lower than normal) impeller or seal bound mechanically, defective
capacitor or relay, motor shorted.
C. Pump starts and stops too often.
Float tight on rod, check valve stuck or none installed in long distance line, overload open, level switch(s) defective,
sump pit too small.
D. Pump will not shut off.
Debris under float assembly, float or float rod bound by pit sides or other, switch out of adjustment.
E. Pump operates but delivers little or
no water.
Check strainer housing, discharge pipe, or if check valve is used vent hole must be clear. Discharge head
exceeds pump capacity. Low or incorrect voltage. Incorrect motor rotation. Capacitor defective. Incoming water
containing air or causing air to enter pumping chamber.
F. Drop in head and/or capacity after
a period of use.
Increased pipe friction, clogged line or check valve. Abrasive material and adverse chemicals could possibly
deteriorate impeller and pump housing. Check line. Remove base and inspect.
In those instances where damages are incurred as a result of an alleged pump failure, the homeowner must retain possession of the pump for investigation purposes.
EASY DO’S & DON'T’S FOR INSTALLING A SUMP PUMP
1.
DO
read thoroughly all installation material provided with the pump.
2.
DO
inspect pump for any visible damage caused by shipping. Contact dealer if
pump appears to be damaged.
3.
DO clean all debris from the sump. Be sure that the pump will have a hard, flat
surface beneath it.
DO
NOT
install on sand, gravel or dirt.
4.
DO
be sure that the sump is large enough to allow proper clearance for the level
control switch(es) to operate properly.
5.
DO Always Disconnect Pump From Power Source Before Handling
.
DO
always connect to a separately protected and properly grounded circuit.
DO
NOT
ever cut, splice, or damage power cord (Only splice in a watertight
junction box).
DO
NOT
carry or lift pump by its power cord.
DO
NOT
use an extension cord with a sump pump.
6.
DO
install a union in the discharge line.
DO
NOT
use a discharge pipe smaller than the pump discharge.
7.
DO
NOT
use a sump pump as a trench or excavation pump, or for pumping
sewage, gasoline, or other hazardous liquids.
8.
DO
test pump immediately after installation to be sure that the system is working
properly.
9.
DO
cover sump with an adequate sump cover.
10.
DO
review all applicable local and national codes and verify that the installation
conforms to each of them.
11.
DO consult manufacturer for clarifications or questions.
12.
DO
consider a two pump system with an alarm where an installation may become
overloaded or primary pump failure would result in property damages.
13.
DO
consider a D.C. Backup System where a sump or dewatering pump is
necessary for the prevention of property damages from flooding due to A.C. power
disruptions, mechanical or electrical problems or system overloading.
14.
DO
inspect and test system for proper operations at least every three months.