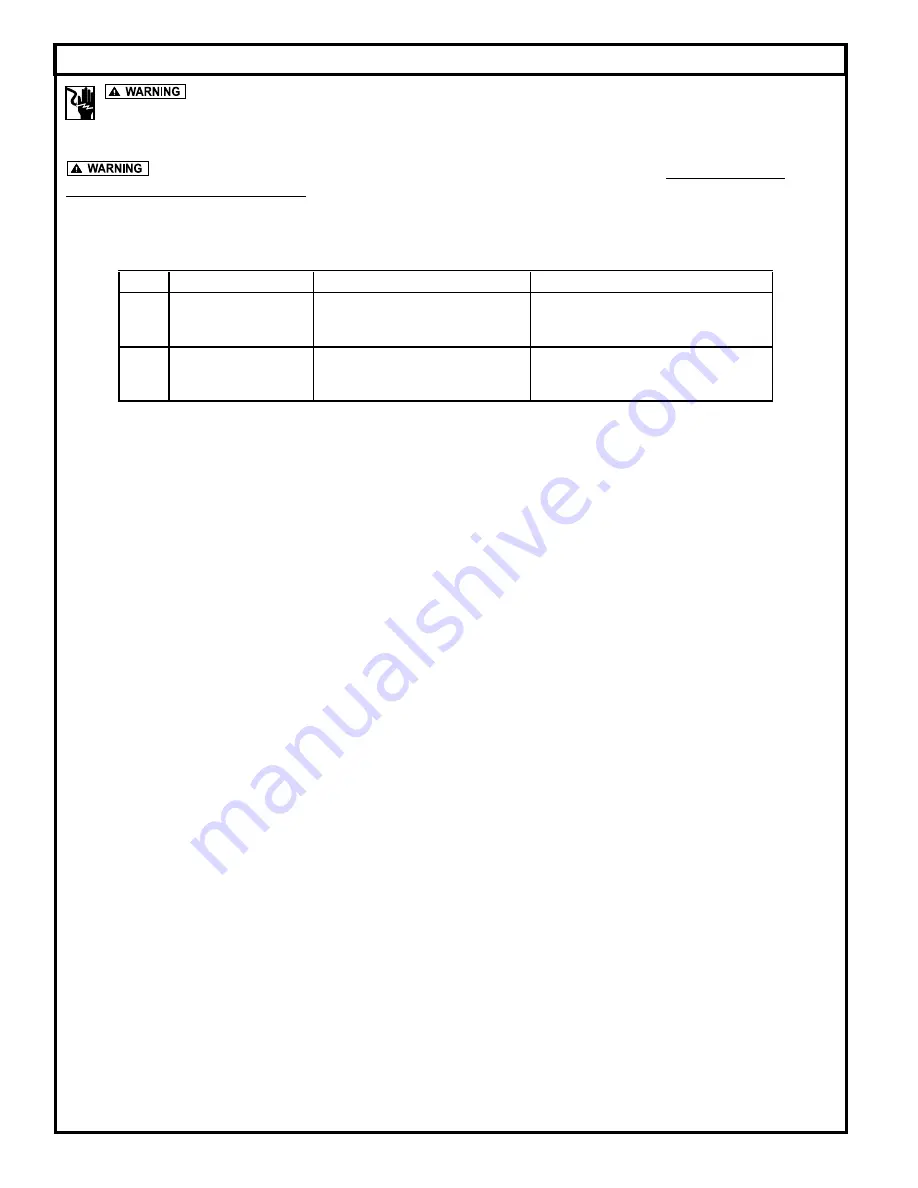
COMMON
CAUSES
B. Motor overheats and trips overload or blows fuse.
- Incorrect Voltage
- Unbalanced power source
- Incorrect motor rotation
- Negative or low head
- Excessive water temperature
- Impeller or seal mechanically bound
- Defective capacitor or relay
- Motor shorted
- Lost one line in a Three Phase unit
C. Pumps starts and stops too often.
- Check valve stuck open
- Level controls out of adjustment
- Temperature sensor tripping
- Thermal overload switch out of
adjustment or defective
- Pit too small
D.
Pump will not shut off.
- Debris under float switch
- Float travel obstructed
- Defective or damaged float switch
- Magnetic starter contacts shorted
- Air lock - check vent hole
E.
Pump operates but delivers little or no water.
- Check for plugged Pump housing, discharge
pipe or sticking check valve
- Vent hole clogged or not drilled
- Discharge head exceeds pumps capacity
- Low or incorrect voltage
- Incorrect motor rotation
- Defective capacitor
F.
Drop in head and/or capacity after a period or use.
- Increase Pipe Friction
- Clogged line or check valve
- Abrasive material & chemical,
deteriorated impeller and pump housing
If the above check list does not uncover the problem, consult the factory - Do not attempt to service or otherwise disassemble pump.
Service Checklist & Trouble Shooting
ELECTRICAL PRECAUTIONS
Before servicing a pump, always shut off the main power breaker to the panel and then
disconnect the pump - making sure you are wearing insulated protective sole shoes and are not standing in water. Under flooded condi-
tions, contact your local electric company or a qualified licensed electrician for disconnecting electrical service prior to pump removal.
Submersible pumps contain oils which become pressurized and hot under operating conditions -
allow 2½ hours after
disconnecting before attempting service.
CONDITION
A. Pump will not start or run.
Steps
Check Voltage At
If No Voltage
If Voltage
No. 1
Line terminals in pump's
control panel
L
1
- L
2
- L
3
(3 Phase).
Check Disconnect switch, line fuse, and/
or circuit breakers in power supply circuit.
Proceed to No. 2.
No. 2
Pump motor terminals in
pump’s control panel
T
1
- T
2
- T
3.
Check for control circuit voltage.
Check
out magnetic starter contacts, thermal
overloads, and float switches.
Check starting relay and capacitor (1 phase
units). Check pump for ground, and binding
impeller.
© Copyright 2014 Zoeller Co. All rights reserved.