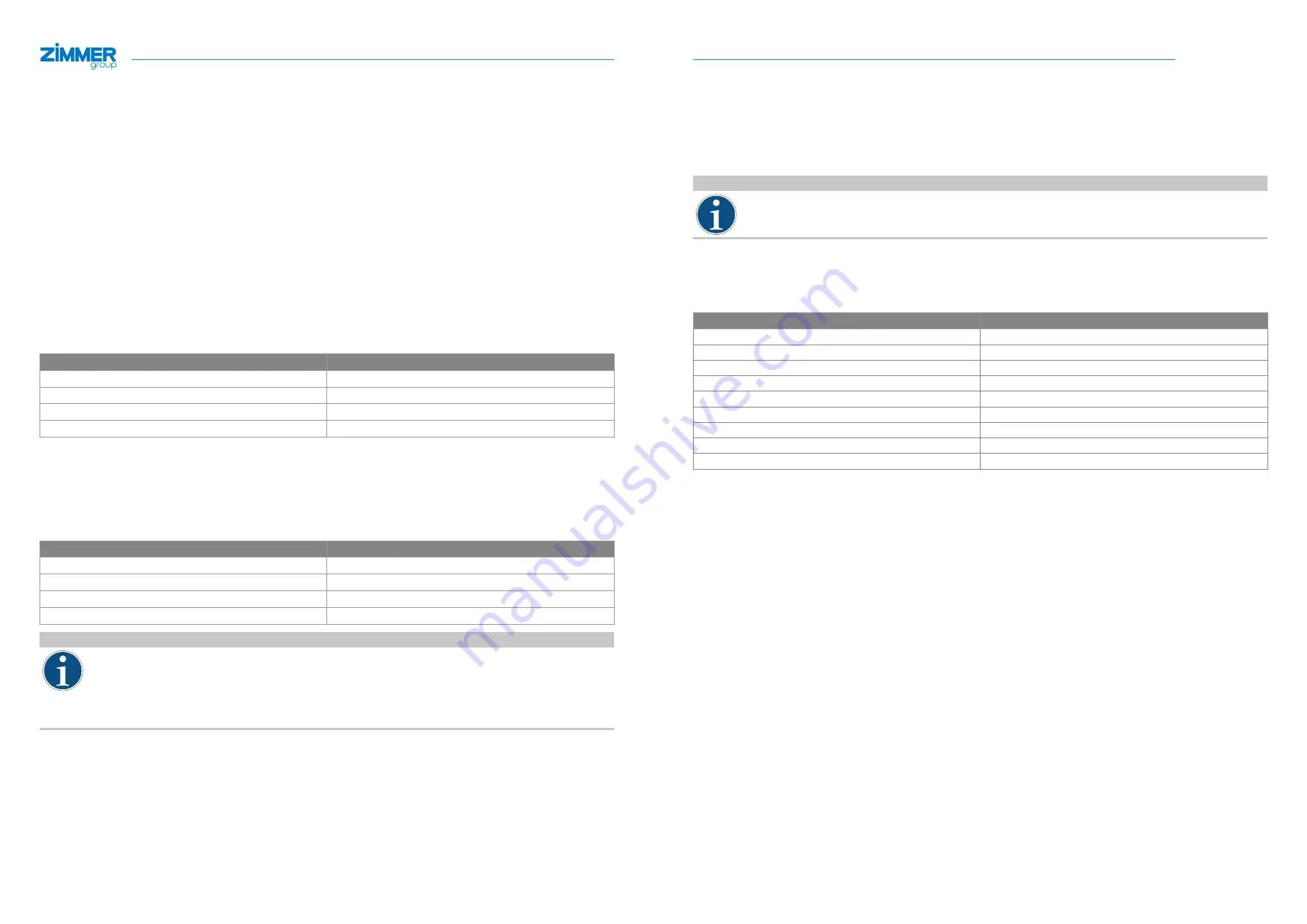
INSTALLATION AND OPERATING INSTRUCTIONS:
GEH6000IL/GED6000IL
INSTALLATION AND OPERATING INSTRUCTIONS:
GEH6000IL/GED6000IL
26
27
EN / 2021-07-28
DDOC00212 / 0
EN / 2021-07-22
DDOC00212 / 0
Zimmer GmbH
•
Am Glockenloch 2
•
77866 Rheinau, Germany
•
+49 7844 9138 0
•
www.zimmer-group.com
Zimmer GmbH
•
Am Glockenloch 2
•
77866 Rheinau, Germany
•
+49 7844 9138 0
•
www.zimmer-group.com
Bit 11: UndefinedPosition
Active if the product is not set to TeachPosition, WorkPosition or BasePosition.
Bit 12: DataTransferOK
This bit is used for data transmission using the handshake. Active as soon as the product has taken over the data using the
parameter ControlWord = 1 (decimal).
Bit 13: ControlWord 0x0100
This bit is a direction flag. Active if the last motion task was carried out toward BasePosition.
Bit 14: ControlWord 0x0200
This bit is a direction flag. Active if the last motion task was carried out toward WorkPosition.
Bit 15: Error
Active if the product has an active error. The error message can be determined using Diagnosis.
11.4.12 Diagnosis
The value returned in Diagnosis corresponds to the error code (see the section “Error Diagnosis”).
Name
Diagnosis
Data format
UINT16
Permission
Write
Transfer
Cyclical
Value range
0 to 65535
11.4.13 ActualPosition
The ActualPosition corresponds to the current position of the gripper jaws relative to the full stroke.
The value is specified with a resolution of 0.01 mm.
The values can move between the BasePosition (minimum value) and the WorkPosition (maximum value). With the installed
position measuring system, it is possible to achieve a position accuracy of +/- 0.05 mm.
Name
ActualPosition
Data format
UINT16
Permission
Read
Transfer
Cyclical
Value range
0 to max. jaw stroke of the product
INFORMATION
►
Use the StatusWord of the product to check whether a workpiece has been gripped correctly.
•
The position measurement resolution is 0.01 mm.
•
The position measurement accuracy is 0.1 mm.
►
During commissioning, be aware of fluctuations around the exact value if you use the ActualPosition
parameter to detect the workpiece.
11.5 Cold boot
For proper function, Zimmer GmbH recommends that the actuator and sensor voltage be supplied with power separately.
The sensor supply must be switched on first.
Once the product is communicating with the PLC, the actuator power supply can be switched on.
Depending on the application, simultaneous activation of both voltages is possible.
INFORMATION
If the sensor supply is disconnected, the C/Q signal (IO-Link) must be disconnected as well.
11.6 Minimum travel path
All products of the GEH6000IL/GED6000IL series need one minimum travel path per gripper jaw to generate the full
gripping force. For each attainable maximum force, the minimum travel path per gripper jaw specified below results before
the gripper fingers are to hit the workpiece.
Installation size
Minimum travel path [mm]
GEH6040IL-03-B
3
GEH6040IL-31-B
3
GEH6060IL-03-B
3
GEH6060IL-31-B
3
GEH6140IL-03-B
1
GEH6180IL-03-B
1
GED6040IL-03-A
4
GED6040IL-31-A
4
GED6140IL-03-A
2