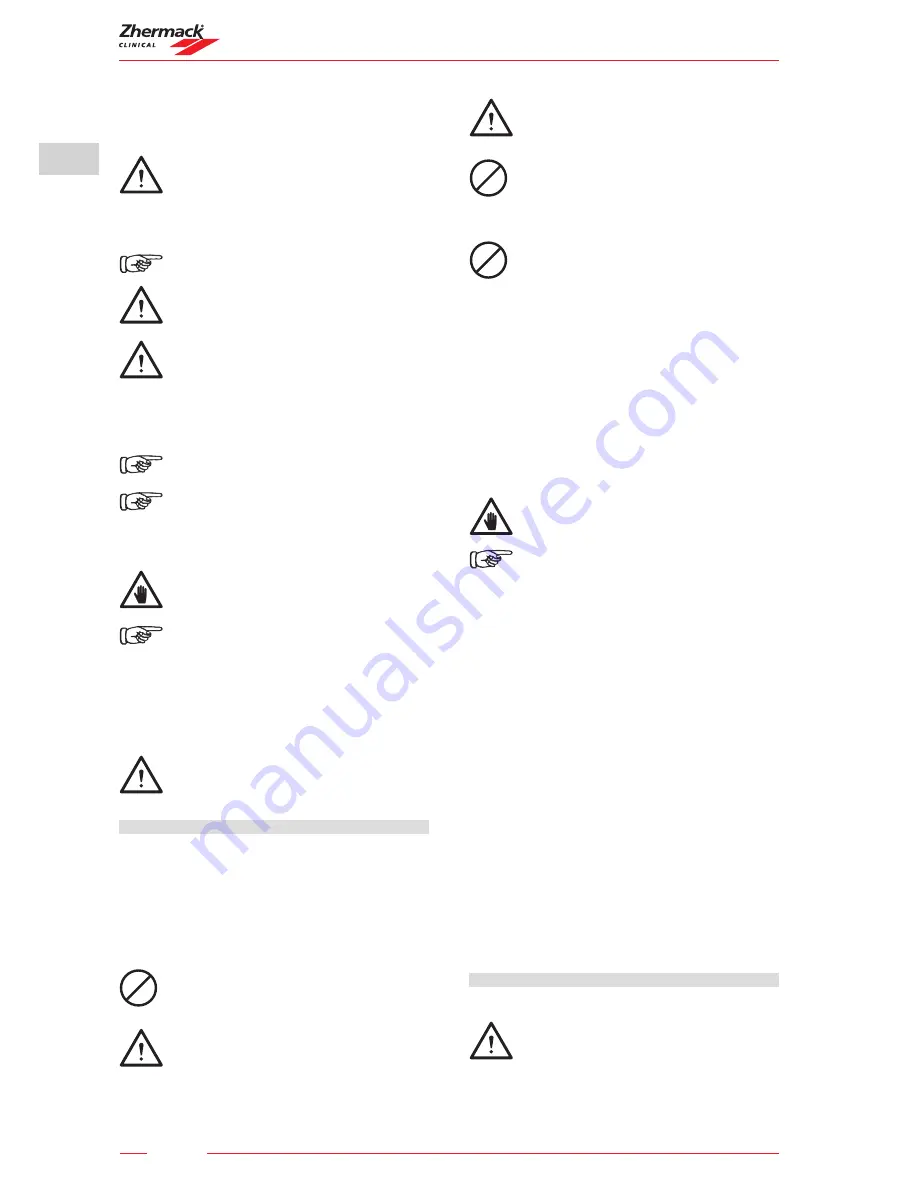
20
hurrimix
The reference figures are present on pages 3, 4, 5 and 6 of this manual and in the product Quick Guide.
EN
Fig. 14: Add the correct quantity of water using the dosing cup
(provided with).
Fig. 15: Dose the plaster using a measuring cup, as recommended
by the Manufacturer and put it in the container for mixing plaster.
The quality of Elite Dental Stones plaster is guaranteed
with a maximum quantity of 100 g. Comply with the
dosage indicated by the Manufacturer.
Fig. 16: Slightly pre-mix the mixture with the provided stick.
Fig. 17: Close the mixing container by pressing the cover and then
turning it clockwise until it locks in place.
It is important to carry out the pre-mixing manually, so
that the powder can be entirely absorbed by the water.
To prevent leakage of material, and malfunctions,
ensure that the cover of the container is closed properly
.
The mixing container is liable to wear and should be
replaced after a period of time.
Fig. 18: Place the container inside the equipment and close the
door.
Fig. 19: Once the program has been selected (fig.13, B), press the
START button to start a mixing cycle.
hurrimix
mixing accelerates the setting time of the
mixture; use cold water to limit the phenomenon.
The device will stop automatically when the selected
mixing cycle finishes.
Fig. 20 : Once the cycle has finished, the mixture is ready to be used:
In this regard, use the provided spatula to collect easily the mixture
from the container for plaster.
We strongly advise never mixing stone then alginate in
the same container as it may contaminate & impede the
setting.
Once the plaster has been mixed, immediately rinse the
accessories with water to prevent the material from
hardening.
7.4
RESIDUAL RISKS
Residual risks are:
• a danger that cannot be totally eliminated through design and
the application of safety devices;
• a potential danger that cannot be highlighted.
In order to prevent accidents, always operate with
respect to that described in this Manual. If in doubt,
always contact the Manufacturer or Authorised After-
Sales Centre.
ChAPTER 8: MAINTENANCE
8.1
CLEANING ThE EQUIPMENT
Use a dry cloth to clean the equipment exterior. If necessary,
dampen the cloth with a small amount of water or a non-
degreasing detergent (see paragraph 2.4).
The operator must ensure that the equipment is kept clean and
free from any foreign bodies such as debris, water, non-conducting
liquids etc. For this purpose cleaning must be performed at the end
of every shift, with the equipment in stable conditions.
Before cleaning the outside of the equipment, always
make sure that the master switch is off. It is prohibited
to clean the equipment when it is connected to the
electric power supply mains.
CLEANING THE ALGINATE CONTAINER:
Wait till the mixture hardens and then remove it from
the container using the spatula. Subsequently rinse the
container and cover. Gently clean the surfaces with non-
alcohol based products.
CLEANING THE PLASTER CONTAINER:
Rinse the container and cover before the mixture hardens.
Gently clean the surfaces with non-alcohol based products.
Do not use inflammable, corrosive, alkaline or toxic
liquids to clean the equipment.
8.2
ROUTINE MAINTENANCE
Once the equipment has been cleaned (see paragraph
8.1), the operator must check for worn, damaged or
loose parts. If any such situations are detected, contact
the Authorised After-Sales Centre.
If any of the previously-described situations should occur, it is
prohibited to re-start the equipment before the problems have
been solved.
In particular, before moving away from the equipment, the
operator detecting problems of any nature must place a sign on
the it indicating that equipment maintenance is in progress and
that use is prohibited (EC-compliant signs can be purchased from
the relevant suppliers). Routine maintenance, cleaning and correct
equipment use are essential factors in guaranteeing long-lasting
equipment performance and safety.
8.3
EXTRAORDINARY MAINTENANCE
Extraordinary maintenance includes the repair of any accidental
breakage and the replacement of worn or malfunctioning parts.
All electrical and mechanical interventions must only be
performed by a Zhermack S.p.A.-authorised maintenance
technician.
Any modification that alters equipment features from a
safety and risk-prevention point of view can only be
carried out by the Manufacturer who will then certify
conformity of the equipment with safety standards.
Therefore any modification or maintenance intervention
not considered in this manual is to be considered
prohibited. Any modification, tampering or repair
performed by unauthorised staff along with the use of
non-original spare parts relieve the Manufacturer from
any liability. If the necessary maintenance interventions
are not considered in this Use and Maintenance Manual,
contact the Authorised After-Sales Centre.
8.4
RE-START AFTER LONG PERIOD OF INACTIVITY
If the equipment is re-started after a particularly long period of
inactivity, operate as indicated in Chapter 6 regarding commissioning.
If the equipment functions anomalously, act as described in Chapter
9 regarding “Diagnostics”. if the problem should persist or is not
considered, contact the Authorised After-Sales Centre immediately.
8.5
hOW TO REQUEST AFTER-SALES ASSISTANCE
Choose one of the following options to request after-sales
assistance:
1. contact the Authorised After-Sales Centre;
2. telephone the Zhermack S.p.A. After-Sales Service at
+39 0425 597611 and proceed as follows: give personal data (e.g.
address and telephone number); state the information given on
the equipment identification plate (see paragraph 3.3); explain the
problem with the equipment clearly;
3. fax all of the information stated in the previous point and the
correctly filled-in identification form (see Attachment 10.2) to the
following n° +39 0425 53596.
ChAPTER 9: DIAGNOSTICS
9.1
GENERAL WARNINGS
If any of the anomalies described below should occur,
solve the problem, where allowed, with respect to all
instructions contained in this manual. If the problem
persists, contact the Authorised After-Sales Centre.