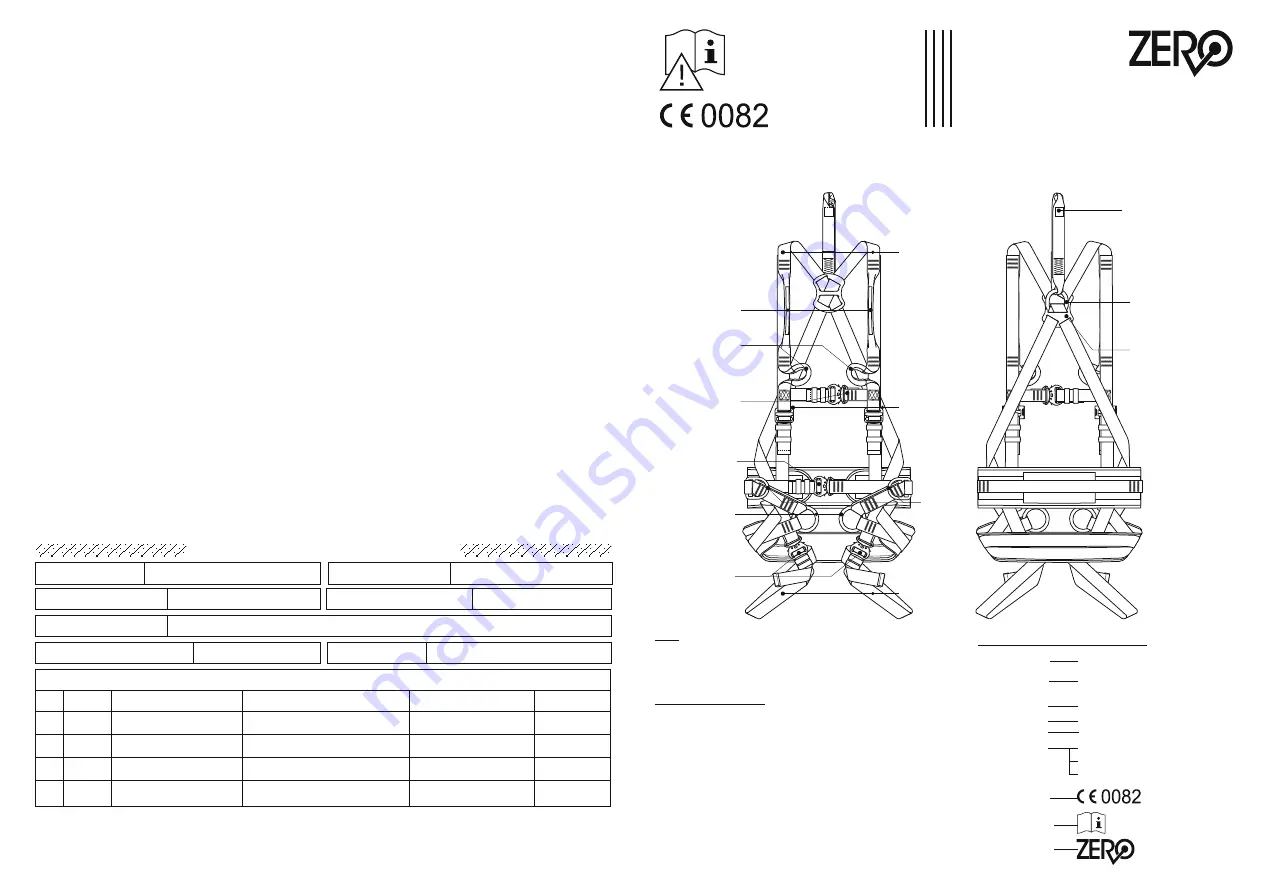
Safety harness Z+87R is body holding device used in fall arrest equipment complied with EN 361. The Z+87R is also equipped in work positioning belt
complied with EN 358 and special attachment loops on the shoulders to be used as a rescue harness complied with EN 1497. Maximum load of the
rescue harness is 140 kg. The harness Z+87R is made of polyester webbings with metallic connecting and adjustment buckles.
!
after every
12 months of utilization, personal protective equipment must be withdrawn from use to carry out periodical detailed inspection. The
periodic inspection must be carried out by a competent person for periodic inspection. The periodic inspection can be carried out also by the
manufacturer or his authorized representative.
In case of some types of the complex equipment e.g. some types of retractable fall arresters the
annual inspection can be carried out only by the manufacturer or his authorized representative.
!
regular periodic inspections are the essential for equipment maintenance and the safety of the users which depends upon the continued efficiency
and durability of the equipment.
!
during periodic inspection it is necessary to check the legibility of the equipment marking.
!
it is essential for the safety of the user that if the product is re-sold outside the original country of destination the reseller shall provide instructions
for use, for maintenance, for periodic examination and for repair in language of the country in which the product is to be used.
!
personal protective equipment must be withdrawn from use immediately when any doubt arise about its condition for safe use and not used again
until confirmed in writing by equipment manufacturer or his representative after carried out the detailed inspection.
!
personal protective equipment must be withdrawn from use immediately and destroyed (or another procedures shall be introduced according
detailed instruction from equipment manual) when it have been used to arrest a fall.
,
!
a full body harness
(complied with EN 361)
is the only acceptable body holding device that can be used in a fall arrest system.
!
the anchor device or anchor point for the fall arrest system should always be positioned, and the work carried out in such a way, as to minimise
both the potential for falls and potential fall distance. The anchor device/point should be placed above the position of the user . The shape and
construction of the anchor device/point shall not allowed to self-acting disconnection of the equipment. Minimal static strength of the anchor
device/point is 1
2
kN. It is recommended to use certified and marked structural anchor point complied with EN795.
!
it is obligatory
to
verify the free space required beneath the user at the workplace before each occasion of use the fall arrest system, so that, in the
case of a fall, there will be no collision with the ground or other obstacle in the fall path. The required value of the free space should be taken from
instruction manual of used equipment.
!
there are many hazards that may affect the performance of the equipment and corresponding safety precautions that have to be observed during
equipment utilization, especially:
- trailing or looping of lanyards or lifelines over sharp edges,
- any defects like cutting, abrasion, corrosion,
- climatic exposure,
- pendulum falls,
- extremes of temperature,
- chemical reagents,
- electrical conductivity.
!
personal protective equipment must be transported in the package (e.g.: bag made of moisture-proof textile or foil bag or cases made of steel or
plastic) to protect it against damage or moisture.
!
the equipment can be cleaned without causing adverse effect on the materials in the manufacture of the equipment. For textile products use mild
detergents for delicate fabrics, wash by hand or in a machine and rinse in water. Plastic parts can be cleaned only with water. When the equipment
becomes wet, either from being in use or when due cleaning, it shall be allowed to dry naturally, and shall be kept away from direct heat. In metallic
products some mechanic parts (spring, pin, hinge, etc.) can be regularly slightly lubricated to ensure better operation. Other maintenance and
cleaning procedures should be adhered to detailed instructions stated in the manual of the equipment.
!
personal protective equipment should be stored loosely packed, in a well-ventilated place, protected from direct light, ultraviolet degradation, damp
environment, sharp edges, extreme temperatures and corrosive or aggressive substances.
IDENTITY CARD
PERIODIC EXAMINATION AND REPAIR HISTORY
1
2
DATE
REASON FOR
ENTRY PERIODIC EXAMINATION
OR REPAIR
3
4
SERIAL NUMBER
USER NAME
DATE OF MANUF.
DATE OF PUTTING
INTO OPERATION
DATE OF PURCHASE
IT IS THE RESPONSIBILITY OF THE USER ORGANISATION TO PROVIDE THE IDENTITY CARD AND TO FILL IN THE DETAILS REQUIRED. THE IDENTITY CARD SHOULD BE
FILLED IN BEFORE THE FIRST USE BY A COMPETENT PERSON, RESPONSIBLE INTHE USER ORGANIZATION FOR PROTECTIVE EQUIPMENT. ANY INFORMATION
ABOUT THE EQUIPMENT LIKE PERIODIC INSPECTIONS, REPAIRS, REASONS OF EQUIPMENT'S WITHDRAWN FROM USE SHALL BE NOTED INTO THE IDENTITY CARD
BY A COMPETENT PERSON. THE IDENTITY CARD SHOULD BE STORAGED DURING A WHOLE PERIOD OF EQUIPMENT UTILIZATION. DO NOT USE THE EQUIPMENT
WITHOUT THE IDENTITY CARD. ALL RECORDS IN THE IDENTITY CARD CAN BE FILLED IN ONLY BYACOMPETENT PERSON.
REF. NUMBER
DEFECTS NOTED,
REPAIRS CARRIED OUT
AND OTHER REVELANT INFORMATIONS
NAME AND SIGNATURE
OF COMPETENT PERSON
PERIODIC
EXAMINATION
NEXT DUE DATE
EN 1497:2007
Instruction Manual
READ CAREFULLY BEFORE USE
THE EQUIPMENT
EN 361:2002
ADMISSIBLE TIME OF USE
Safety harness can be used for 5 years from a date of putting the
harness into operation. After this period the harness
manufacturer's
.
The
manufacturer's inspection can be carried out
by:
- manufacturer
- or person recommended by manufacturer
- or company recommended by manufacturer.
During
this inspection
will be established admissible time of
harness
use till next
manufacturer's
inspection.
The harness
must be
withdrawn from use to carry out
detailed inspection
must be withdrawn from use immediately and destroyed
when it ha
s
been used to arrest a fall.
EN 358:1999
dorsal attachment D ring
for fall arrest systems
extension lanyard
for fall arrest systems
crossing plate
work
positioning belt
connecting
buckle
frontal
attachment loops
for fall arrest
systems
leg strap
connecting
buckles
chest strap
connecting buckle
lateral
attachment rings
for work positioning
systems
shoulder strap
adjustment
buckles
shoulder
attachment loops
for rescue
equipment
shoulder
straps
leg
straps
SIZES
The harness is manufactured in two sizes:
- universal: M-XL
- extra large: XXL
model marking
marking of the manufacturer
or distributor
caution: read the manual
CE marking and number
of a notified body controlling
manufacturing of the equipment (art. 11)
number / year
of the European standards
the equipment conform
size
month/year of manufacture
type of the device
CONTENT OF HARNESS IDENTITY LABEL
MODEL AND
TYPE OF EQUIPMENT
Notified body, at which the European certification
was performed and which
supervises
the production of the equipment:
APAVE SUDEUROPE SAS - CS 60193
13322 MARSEILLE CEDEX 16 - FRANCE
device serial number
lateral
attachment
D-rings
for work
positioning
systems
HTP1679
SAFETY/RESCUE HARNESS
Size:
M-XL
Date of manufacture:
MM/YYYY
Serial number:
XXXXXXX
EN 361:2002
EN 358:1999
EN 1497:2007 - max. 140 kg
zero tolerance is essential
HTP1679
zero tolerance is essential
Zero Advanced Height Safety
Head Office, PBI Height Safety Ltd
PO Box 39048, Harewood 8545
10 Holt Pl, Harewood 8053
Christchurch, New Zealand
P: +64 3357 0093 F: +64 3360 2199
Freephone: (NZ) 0800 357 003
(AUST) 1800 421 608
E: [email protected]
www.zero4heightsafety.com
SAFETY/RESCUE
HARNESS
PBIHS