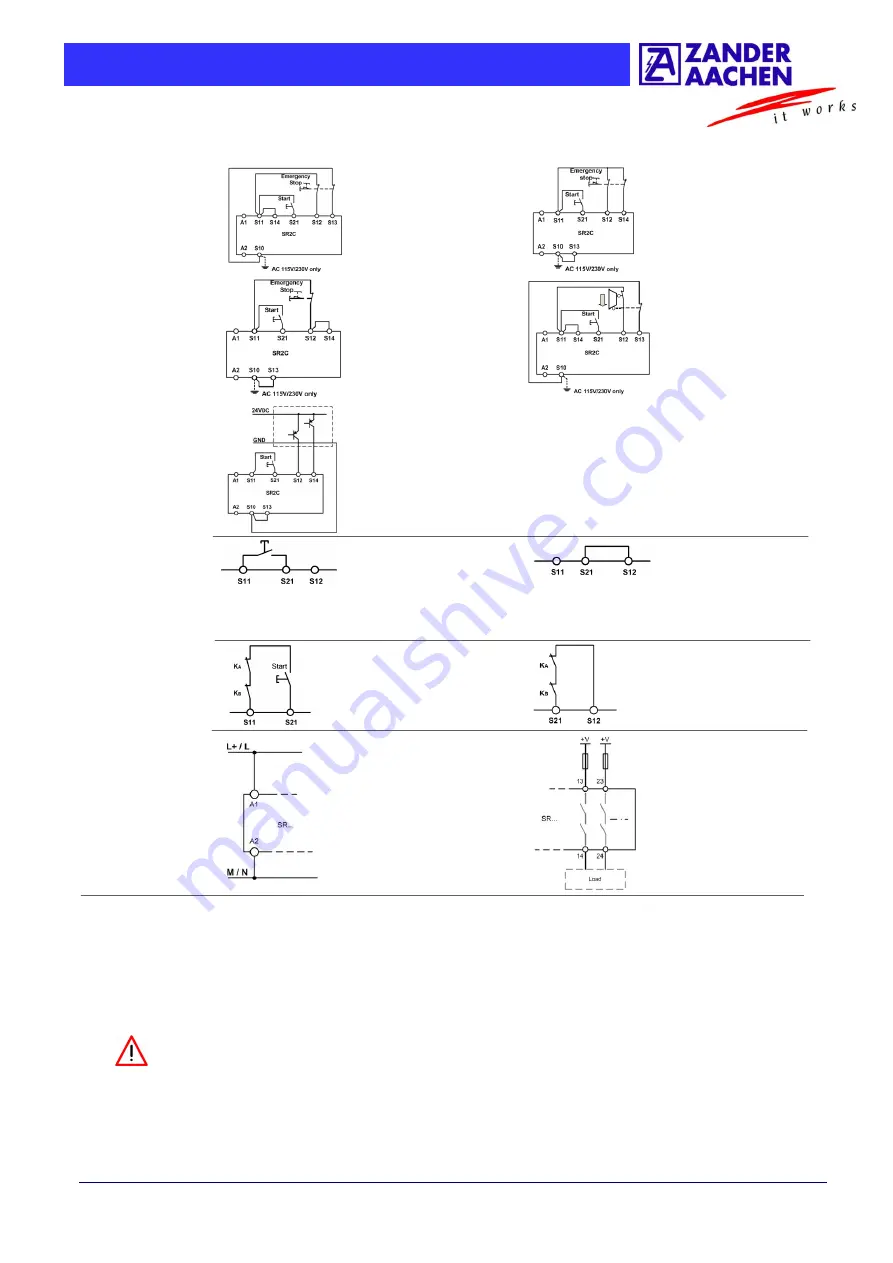
2
H. ZANDER
GmbH & Co. KG • Am Gut Wolf 15 • D52070 Aachen • Tel +49 (0)241 9105010 • Fax +49 (0)241 91050138
[email protected] • www.zander-aachen.de
User Information
B01
B101
E61-136-00
Note:
The items listed under “Electrical connection” must be observed during commissioning
.
Commissioning
Procedure
1. Wiring emergency stop circuit:
Wire the emergency stop circuit according to the required
Performance Level determined (see Fig. 1 to Fig. 5).
2. Wiring start circuit:
Wire the start circuit according to Fig. 6 or Fig. 7 to set the
starting behavior.
Warning:
If “Automatic start” is set, bear in mind that the safety con-
tacts will switch immediately after the power supply is
connected. If “Monitored manual start” is set, the start
button must be opened after wiring.
3. Wiring feedback loop:
If your application provides for external contactors or ex-
pansion modules, connect them to the device according to
Fig. 8 or Fig. 9.
4. Wiring power supply:
Connect the power supply to terminals A1 and A2 (Fig. 10).
Warning:
Wiring only in de-energized state.
5. Starting the device:
Switch on the operating voltage.
Warning:
If the “Automatic start” starting behavior is set, the safety
contacts will close immediately.
If the “Monitored manual start” starting behavior is set, close
the start button to close the safety contacts.
LEDs
K1
and
K2
are lit.
6. Triggering safety function:
Open the emergency stop circuit by actuating the connec-
ted safety switch. The safety contacts open immediately.
7. Reactivation:
Close the emergency stop circuit. If “Automatic start” is
selected, the safety contacts will close immediately.
If the “Monitored manual start” starting behavior is set, close
the start button to close the safety contacts.
Fig. 6:
Monitored manual start.
It is monitored that the start
button was opened before the
emergency stop button closes.
(Prerequisite:
operating voltage must not be
interrupted.)
Fig. 7:
Automatic start.
Max perm. delay during
closing of the safety switches
on S12 and S13:
S12 before S13: 300 ms
S13 before S12: any
Warning:
Safety contacts switch
immediately when the
power supply is connected.
Depending on the application or the result of the risk assessment according to EN ISO 13849-1, the device must be wired as
shown in Fig. 1 to Fig. 11.
Applications
Fig. 3:
Single-channel emergency stop
circuit with earth fault monito-
ring.
(category 1, up to PL c)
Fig. 2:
Two-channel emergency stop
circuit with earth fault monitoring.
(category 3, up to PL d)
Fig. 1:
Two-channel emergency stop
circuit with short circuit and earth
fault monitoring.
(category 4, up to PL e)
Fig. 4:
Two-channel sliding guard
monitoring with short circuit and
earth fault monitoring.
(category 4, up to PL e)
Emergency Stop
Circuit
Starting Behavior
Safety Emergency Stop Relay SR2C
Notice:
In order to activate earth fault monitoring, S10 must be
connected to PE (protective earth) on the AC115/230V
devices. With AC/DC 24 V, connect PE only to the power
supply unit according to EN60204-1.
Fig. 5:
Two-channel emergency stop
with pnp-outputs/OSSD-outputs
with
short circuit monitoring.
(category 4, up to PL e)
Fig. 8:
Feedback loop for monitored manual
start:
The feedback loop monitors contactors
or the expansion modules .
Feedback Loop
Fig. 9:
Feedback loop for automatic start:
The feedback loop monitors contac-
tors or the expansion modules .
Power supply
and
Safety contacts
Fig. 10:
Power supply A1 and A2.
(Power supply according to techn.
Data )
Fig. 11:
Connecting load to safety contacts.
(Figure shows example.
Voltage „+V“ according to techn.
Data)