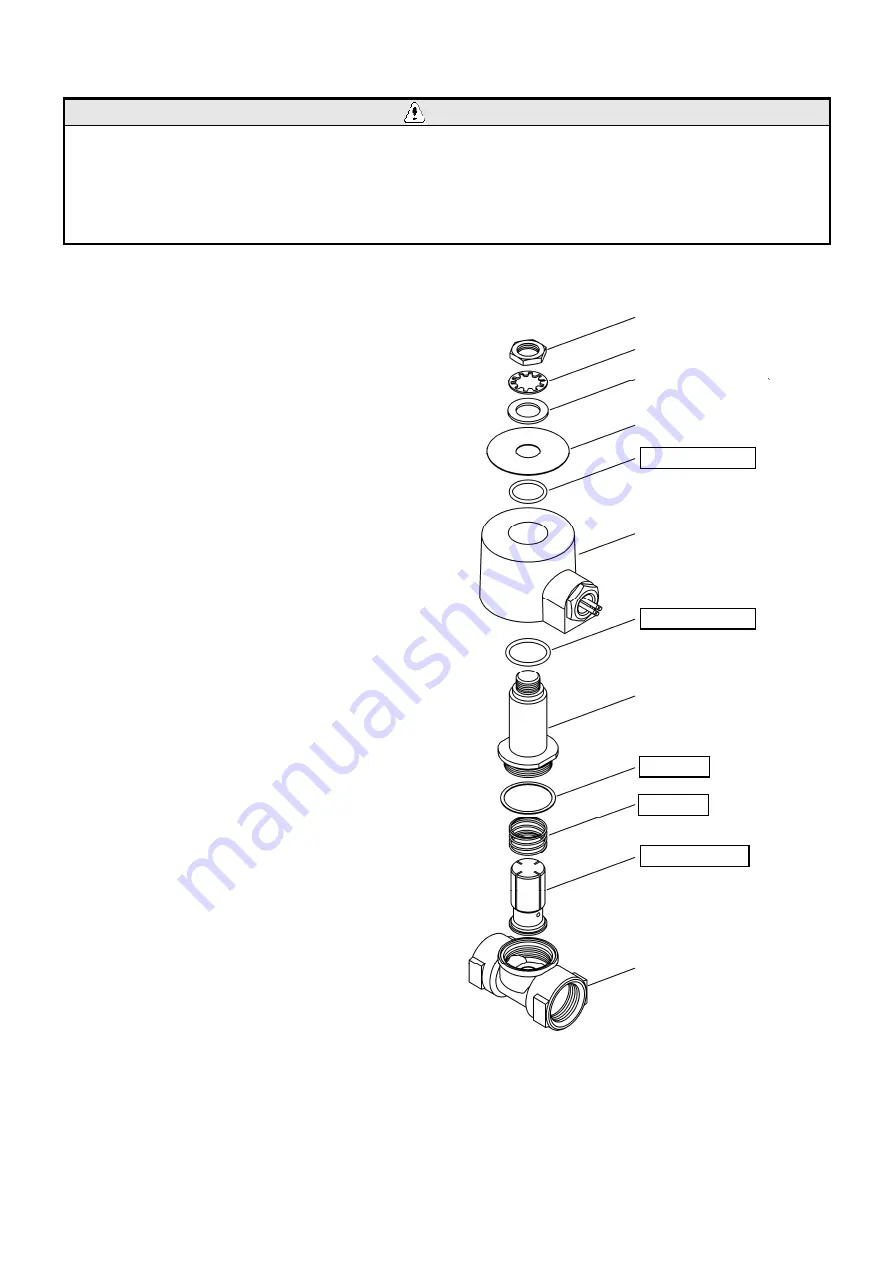
12
■
EPDT-251b
■
9.4 Disassembly and reassembly
(See “Exploded drawing” below.)
Warning
1. Confirm that no power is supplied before disassembling.
* Failure to do so may cause an electric shock.
2. Completely discharge the pressure inside of the product, line and equipment before disassembling or
maintenance, and cool down the product till it can be touched with bare hands in the case of
high-temperature fluid.
* Failure to do so may result in injury or burns due to residual pressure.
■
Exploded drawing
(1) Loosen Hexagon nut (M14) and
remove Tooth lock washer, Plain
washer, Name plate and O-ring
(Small), and then dismount Coil.
(2) Remove Pipe with a spanner (32
mm width across flat).
(3) Remove Plunger.
(4) Reassemble the product in the
reverse order of disassembling.
(5) Tighten Pipe with the torque of 50
N
▪
m, and Hexagon nut with that of
15 N
▪
m.
The parts name shown in the rectangle boxes
are available as consumable supply.
Pipe
Hexagon nut
Tooth lock washer
Plain washer
Name plate
O-ring (Small)
Coil
O-ring (Large)
Gasket
Spring
Plunger (Disc)
Body