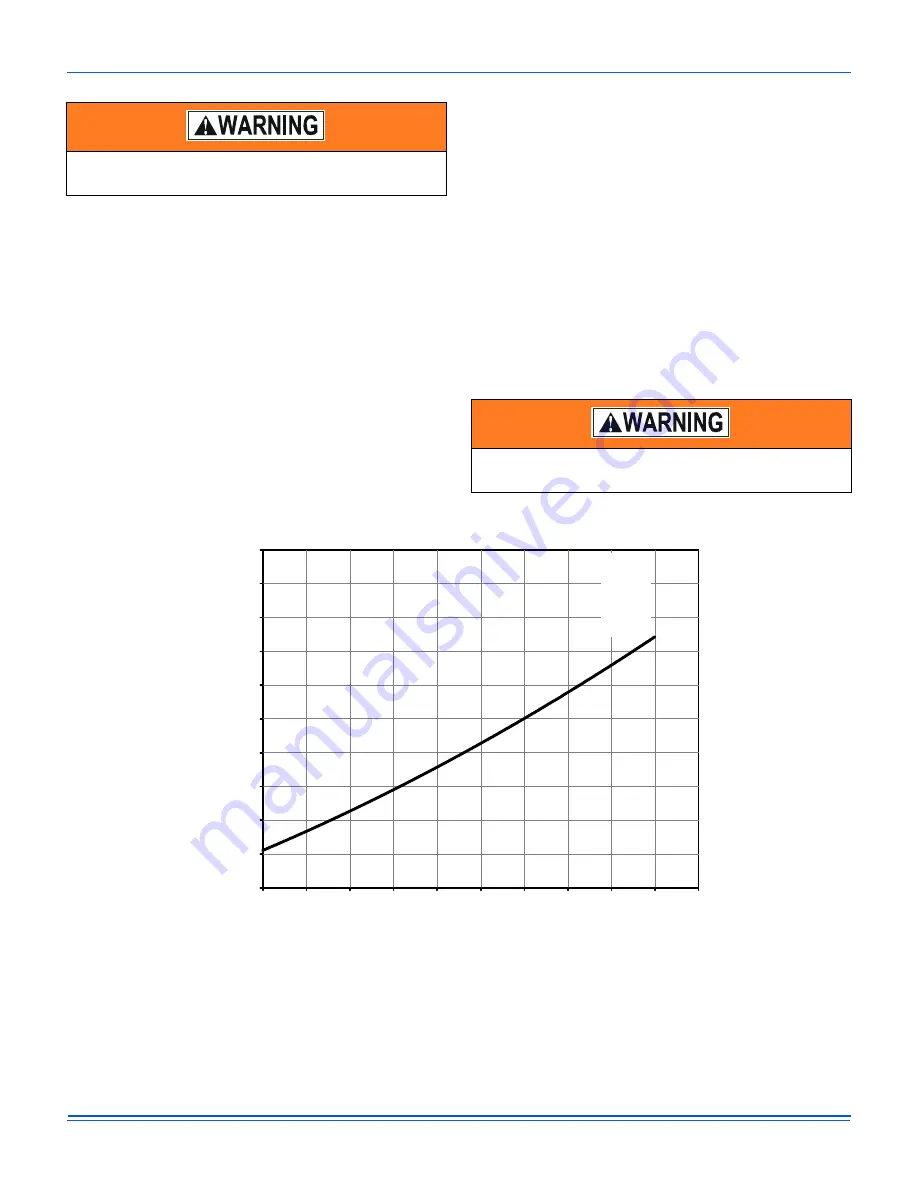
5565604-BIM-B-1018
50
Johnson Controls Ducted Systems
Method Two
1.
Drill two 5/16 inch holes, one in the return air duct as close
to the inlet of the unit as possible, and another in the supply
air duct as close to the outlet of the unit as possible.
2.
Using the whole drilled in step 1, insert eight inches of 1/4
inch metal tubing into the airflow of the return and supply
air ducts of the unit.
NOTE:
The tubes must be inserted and held in position
perpendicular to the airflow so that velocity pressure
will not affect the static pressure readings.
3.
Use an Inclined Manometer or Magnehelic to determine
the pressure drop across the unit. This is the External
Static Pressure (ESP). In order to obtain an accurate
measurement, be certain that the air filters are clean.
4.
Determine the number of turns the variable motor sheave
is open.
5.
Select the correct blower performance table for the unit
from Tables 17 and 18. Tables are presented for side and
down flow configuration.
6.
Determine the unit Measured CFM from the Blower
Performance Table, External Static Pressure and the
number of turns the variable motor sheave is open.
7.
To adjust Measured CFM to Required CFM, see SUPPLY
AIR DRIVE ADJUSTMENT.
8.
After reading has been obtained, remove the tubes and
seal holes.
9.
Tighten blower pulley and motor sheave set screws after
any adjustments. Re-check set screws after 10-12 hrs. run
time is recommended.
NOTE:
With the addition of field installed accessories repeat
this procedure.
Figure 31: Dry Coil Delta P
Failure to properly adjust the total system air quantity
can result in extensive blower damage.
Failure to properly adjust the total system air quantity
can result in extensive blower damage.
0
0.05
0.1
0.15
0.2
0.25
0.3
0.35
0.4
0.45
0.5
1500
2000
2500
3000
3500
4000
4500
5000
5500
6000
6500
Airflow (CFM)
Dry Coil Delta P (iwg)
ZW-08
ZW-10
ZW-12
ZW-06
ZW-07