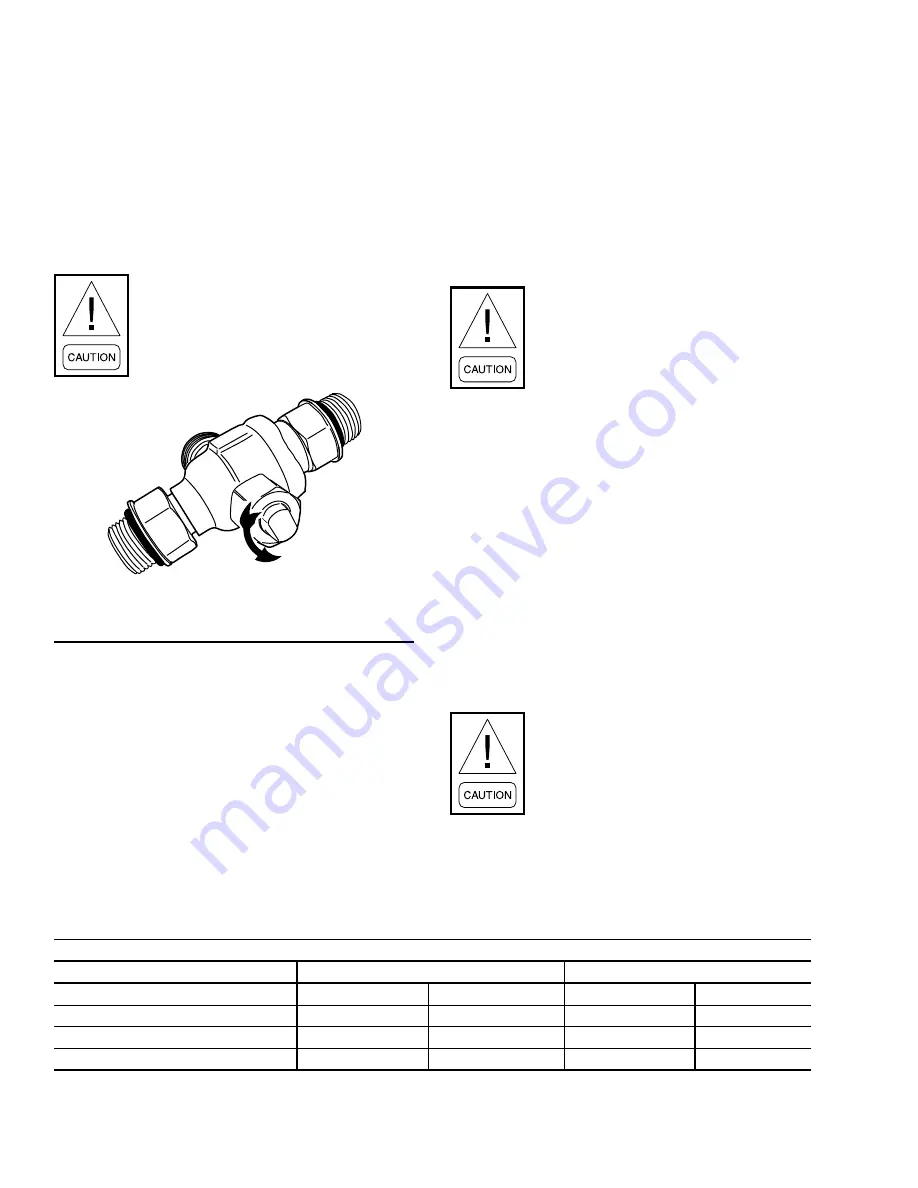
JOHNSON CONTROLS
66
FORM 160.67-O2
ISSUE DATE: 10/9/2020
SECTION 4 - OPERATIONAL MAINTENANCE
Dual Oil Filter Replacement
The dual oil filter option allows one oil filter to be iso-
lated and changed with the chiller in operation.
1.
Isolate the left hand filter by turning the valve
stem parallel with the valve body. 90º counter
clockwise.
2. Isolate the right hand filter by turning the valve
stem 1/4 turn clockwise.
Do not force the valve stem past the stop.
Damage to the Isolation Valve will occur.
FIGURE 17 -
DUAL OIL FILTER ISOLATION VALVE
LD09034
TURBINE OIL MAINTENANCE
Ring Oil Lubrication
Turbines lubricated with oil rings are equipped with
constant level oilers. The purpose of these oilers is to
maintain the correct oil level in the bearing housings.
The oil level within bearing housings must be main-
tained at a sufficient level to allow the oil rings to run
in the oil. An oil level that is too high results in oil leak-
age past the shaft seals. The oil level gauge on the side
of the bearing housing indicates the oil level. A mark
inscribed on the lower-half bearing housing indicates
the proper oil level. Oil levels in both bearing housings
should be checked daily. Always use a strainer when
adding oil to the systems and cover the fill connection
when finished. If there is any reason to suspect wa-
ter in the oil, open the low point drain in each bearing
housings slightly. If water is present, it will be the first
thing to come out of the drain. Low point drains in the
bearing housing should be checked weekly for water.
The presence of oil in the constant level
oilers does not necessarily mean that oil
in the bearing housings is at the proper
level. CLEANLINESS is ESSENTIAL
for long and trouble free service from the
BEARINGS. Care must be taken to ensure
that no foreign material enters bearing
housings or constant level oilers when
performing maintenance, checking oil,
adding oil, or making adjustments.
Cooling of the bearing oil is accomplished by water
jackets integral to the bearing housings. Verify that the
cooling water supply is being maintained at 2 GPM
(7.0 L/min) minimum, 90°F (32°C) maximum, and
150 PSIG (1035 kPaG) for the bearing housings. Cool
-
ing water flow should be adjusted by partially closing
the valve in the cooling water outlet line while observ-
ing the thermometers on the bearing housings to main-
tain the bearing oil sump temperature in the normal
range as shown in the Table 1 below.
Do not allow the COOLING WATER
to COOL THE BEARING OIL SUMP
TEMPERATURE to below 130°F (54°C),
as this may interfere with the action of the
oil rings or cause atmospheric moisture to
condense in the oil reservoir.
TABLE 1 -
RECOMMENDED MAXIMUM TURBINE BEARING, OIL SUMP, AND METAL TEMPERATURES
RECOMMENDED MAXIMUM TURBINE BEARING, OIL SUMP, AND METAL TEMPERATURES
Bearing Oil Sump Temperature
Bearing Metal Temperature
Operating Status
°F
°C
°F
°C
Normal Operation
130-180
54-82
150-200
66-93
Alarm
200
93
210*
99
Trip
210
99
220*
104
* Bearing alarm & trip values should be set at 10 °F (5.5 °C) to 15 °F (8.4 °C) above operating temperature when running at unit design condi-
tions. Maximum alarm setting of 210 °F (99 °C) and 220 °F (104 °C) trip.