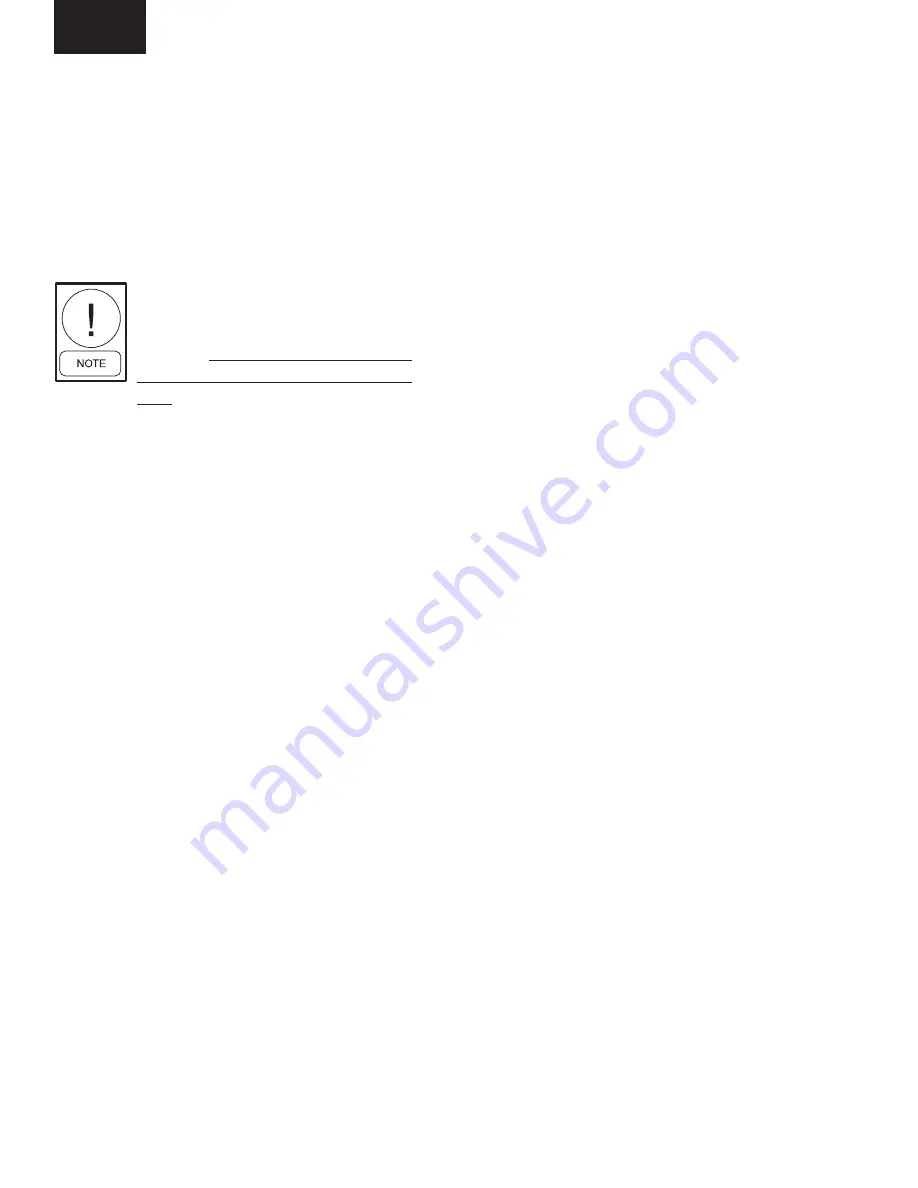
YORK INTERNATIONAL
32
FORM 220.11-NM2 (602)
SECTION 4
SERVICE
GENERAL
Service on these compressors consists essentially of
maintaining the lubrication system (auxiliary oil pump,
filter and cooler) and replacing the various seals and
bearings.
When the system is open for repairs,
it is important to keep the gas side of
the compressor as clean and dry as
possible. Keep all openings covered
except while actually working on the
unit.
Before installing new parts, thoroughly clean the parts
and apply a light coating of Liquid Molycote (Part No.
013-00834-000) to the balance piston seal ring, shaft
seal labyrinths and impeller labyrinths. Apply Molycote
Paste, Part No. 360-00125, to the impeller eye diam-
eter and the shaft area under the floating aluminum shaft
seals.
The journal bearings and balance piston drum diam-
eter shall be pre-lubricated with a light coating of Mo-
lybdenum Disulfide Powder, Part No. 364-21508-000
(2 oz. tin).
SERVICE TIPS
Practices that should be followed in disassembly and
reassembly of the compressor are as follows:
Do Not Mix Parts
Keep parts in some general order when removing them
from the compressor. It is suggested that parts be laid
out to follow exploded views as shown in the illustra-
tions outlining the disassembly and assembly of the
various parts.
Do Not Mix Cap Screws and Washers
Cap screws and like parts of a length, material, and
heat treatment are suited to the location in which they
are used. Too long or too short a cap screw can result
in leakage or interference with some interior parts. It is
very important to use correct washers or lockwashers.
The parts list and figures on the compressor drawing
shows the correct length and size of screws and wash-
ers. See the drawing supplied with job to order the cor-
rect numbers.
The Operating and Maintenance Instructions,
From???????
Inspect as Compressor is Disassembled
Once compressor parts have been disassembled and
cleaned, valuable indications of the compressor condi-
tion are lost. For example: Materials found in oil often
indicate as to why a part or parts have failed.
Protect Parts and Surfaces
Do not scatter removed parts indiscriminately. Coat ma-
chined surfaces likely to rust with YORK Oil or a rust
preventive. Protect surfaces subject to scratching or nick-
ing during repair operations. Plug any oil passages likely
to accumulate dust or abrasives.
Clean Thoroughly
No compressor is completely overhauled if it is not
cleaned internally to “new part” condition. Dirty parts
cannot be inspected nor fitted and will cause excessive
and/or premature wear when the compressor is in op-
eration. The oil cooler and interconnecting lines must
also be cleaned.
Cleaning and Checking Wearing Parts
Before reassembling the compressor, all parts should
be thoroughly washed with an approved safety solvent.
During reassembly, carefully check each part for signs
of uneven wear, bearing in mind that a polished sur-
face is not an indication of excessive wear. Sudden ex-
cessive wear on any part of the compressor is not nor-
mal. It is usually caused by some other condition which
must be determined and corrected to assure trouble free
operation.
Worn parts should be replaced with new parts and each
new part should be thoroughly examined for shipping
damage.
While the compressor oil sump is open, carefully wash
with an approved safety solvent, clean with a lint free
cloth, and oil with YORK Oil of proper designation.
Clean and check all oil passageways and tubing.
Before assembling parts, all friction surfaces such as
bearings and moving parts should be lightly coated with
the appropriate lubricant. Be sure to use YORK Oil of
proper designation. Bearings and seals should be re-
placed with new parts. All gaskets and O-rings should
be replaced after compressor disassembly to ensure
proper sealing of surfaces.
Service
Содержание Turbomaster M 255
Страница 9: ...FORM 220 11 NM2 602 9 YORK INTERNATIONAL FIG 2 TYPICAL COMPRESSOR CROSS SECTIONAL VIEW LD07317 1...
Страница 15: ...FORM 220 11 NM2 602 15 YORK INTERNATIONAL FIG 3 TYPICAL PRIMARY COMPRESSOR GAS FLOW LD07318 3...
Страница 16: ...YORK INTERNATIONAL 16 FORM 220 11 NM2 602 FIG 4A MAJOR COMPONENTS LD07319 Operation...
Страница 31: ...FORM 220 11 NM2 602 31 YORK INTERNATIONAL Operation 3 This page intentionally left blank...