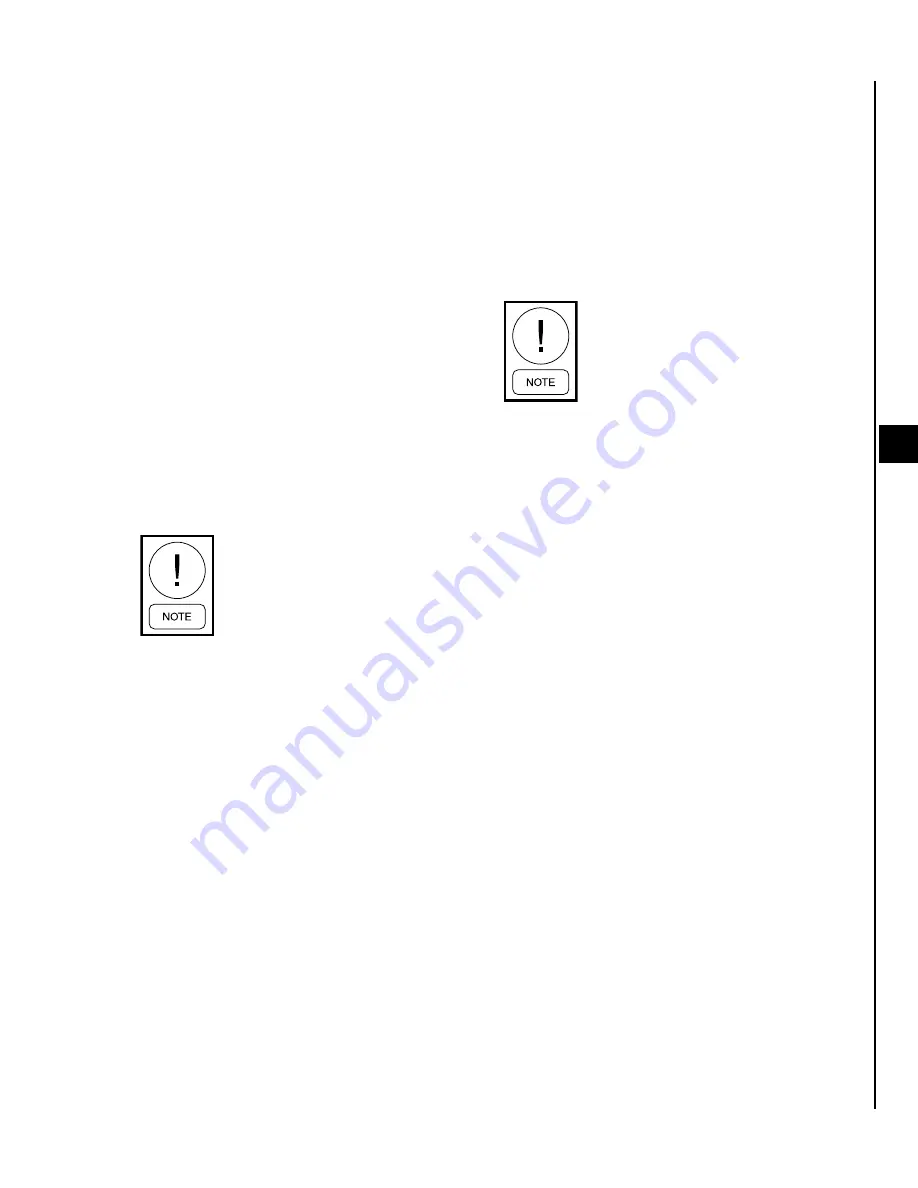
JOHNSON CONTROLS
33
SECTION 7 - PREVENTIVE MAINTENANCE
FORM 160.76-O1
ISSUE DATE: 05/22/2019
7
Procedure
Greasing
In most cases, re-lubrication must be performed with
the motor shut down and at rest. However, in some cas-
es, it may be performed with the motor operating - see
The specified amount of grease should be added at
each specified interval to both the DE and NDE bear-
ings. Current YORK OptiView panels provide a warn-
ing message to re-lubricate beginning at a programmed
number of operating hours (the default value is 1000
hours). At the programmed value plus 400 hours this
feature will shut down the chiller if re-lubrication is
not addressed. In plants where chillers run 24/7, there
is more than 16 days of advance warning prior to shut-
ting down the chiller.
1. Open the relief port plug below the bearing, if
equipped.
2.
Add the specified amount of grease, as per
Only pump the required number
of pumps as determined by the
calibration procedure below. Do
not expect old grease to exit at the
relief port.
3. Run the motor for 30 to 45 minutes.
It is not necessary to see old grease coming out
from the relief port after adding the new grease.
4. Re-install the plug.
Motor Rotation
All motors must be rotated if idle for 90 days. The rota-
tion should allow for the keyway to be positioned dif-
ferently than when the rotation process was started. For
example, if the keyway is at the twelve o'clock posi-
tion, after the rotation the keyway should be at another
position, for example, the three o'clock position.
Grease Gun Calibration
Grease guns should be calibrated to determine the
number of pumps required to get 1.5 cubic inches of
grease. To calibrate,
1. Form an open-top cardboard cube (1 in. x 1 in. x
1 in.).
2. Pump grease into this container until the grease is
level with the top, counting the number of pumps.
3. When the grease is level with the top, this is the
number of pumps for one cubic inch of grease.
4. Multiply the number of pumps by 1.5 to get the
number of pumps for YORK chiller motor bear-
ings.
Over-greasing can be as detrimental as
under-greasing, or total lack of greasing.
A bearing housing over-filled with grease
can run 20
°
centigrade higher temperature
than one with the proper amount of grease.
Similarly, for motors requiring a fixed
number of grams of grease, a scale should
be used to determine the number of pumps
required to achieve the number of grams
prescribed.
Type of Grease
All standard YORK chiller motors utilize a polyurea
grease, specifically formulated for high-speed rolling
element bearings. Only two greases are approved for
most standard chiller motors:
• Preferred choice: Mobil Polyrex EM - Grainger
part number 5XB54
• 2nd choice, for TECO and Ram: Chevron SRI #2
There are a few exceptions, such as Reliance Q-frame
motors built from 1997 to 2003, and some special or-
der motors, such as medium-voltage motors from Sie-
mens and ABB. In these cases, use only grease called
for by the motor manufacturer.
For Reliance motors, there is a metal tag affixed to the
motor calling for Texaco Premium RB grease. This is
a lithium based lubricant and should never be mixed
with polyurea grease. When the two products come to-
gether, the thickeners release their oil molecules and
oil settles in the bottom of the bearing housing, or exits
at the relief plug or around the shaft. Bearings can fail
within 1000 hours when non-compatible greases be-
come mixed. If you are unable to locate this specific
Texaco product, other approved lithium based greases
are Shell Alvania RL3 in NLGI #3 or Mobilith SHC100
NLGI #2, Grainger P/N 4ZF49.