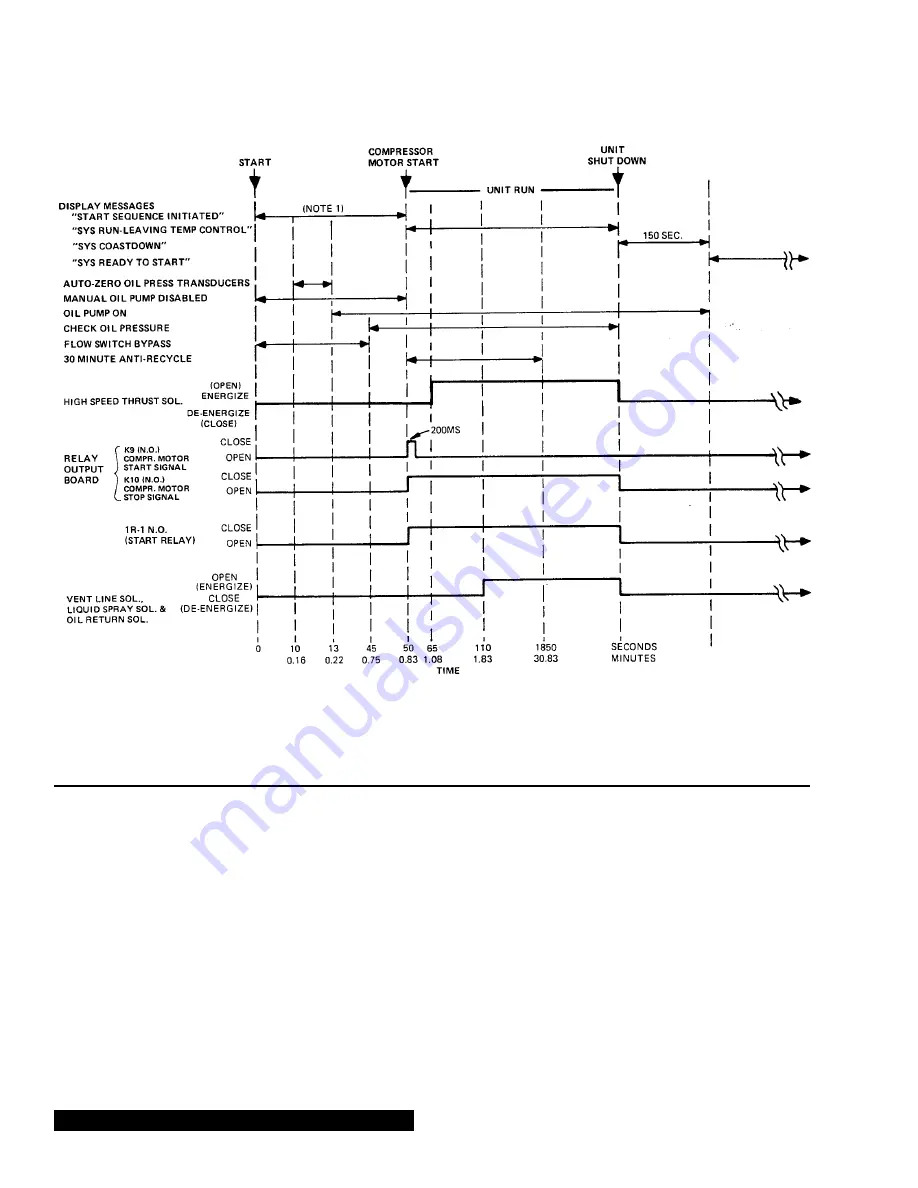
32
YORK INTERNATIONAL
However, the current draw (amperes) by the compres-
sor motor cannot exceed the setting of the % CUR-
RENT LIMIT at any time during the unit operation, since
the MicroComputer Control Center 40 to 100% three-
phase peak current limit software function, plus the 3-
phase 100% solid state overload current limiter (CM-
2) on Electro-Mechanical Starter applications or the
Solid State Starter current Limit function will override
the temperature control function and prevent the Pre-
rotation Vanes from opening beyond the % CURRENT
LIMIT setting.
If the load continues to decrease, after the Prerotation
Vanes are entirely closed, the chiller will be shut down
by the Low Water Temperature control (LWT) function
which is displayed on the Control Center as:
MON 10:30 AM – LOW WATER TEMPERATURE – AUTOSTART
This occurs when the leaving water temperature falls
to 4°F below setpoint or 36°F, whichever is higher. The
LWT is part of the Micro Board.
NOTE: If the temperature setpoint has been repro-
grammed within the last 10 minutes, the LWT
cutout is 36°F for 10 minutes.
Condenser Water Temperature Control
The YORK Millennium chiller is designed to use less
power by taking advantage of lower than design tem-
peratures that are naturally produced by cooling tow-
ers throughout the operating year. Exact control of con-
denser water such as a cooling tower bypass, is not
necessary for most installations. The chiller requires
only that the minimum condenser water temperature
SYSTEM STARTING & SHUTDOWN SEQUENCE
OPERATOR INITIATED
FIG. 15 – CHILLER STARTING SEQUENCE & SHUTDOWN SEQUENCE
NOTES: 1. REF. MICROBOARD PROGRAM JUMPER JP6
2. REF. MICROBOARD PROGRAM JUMPER JP4
(NOTE 2)
LD00952