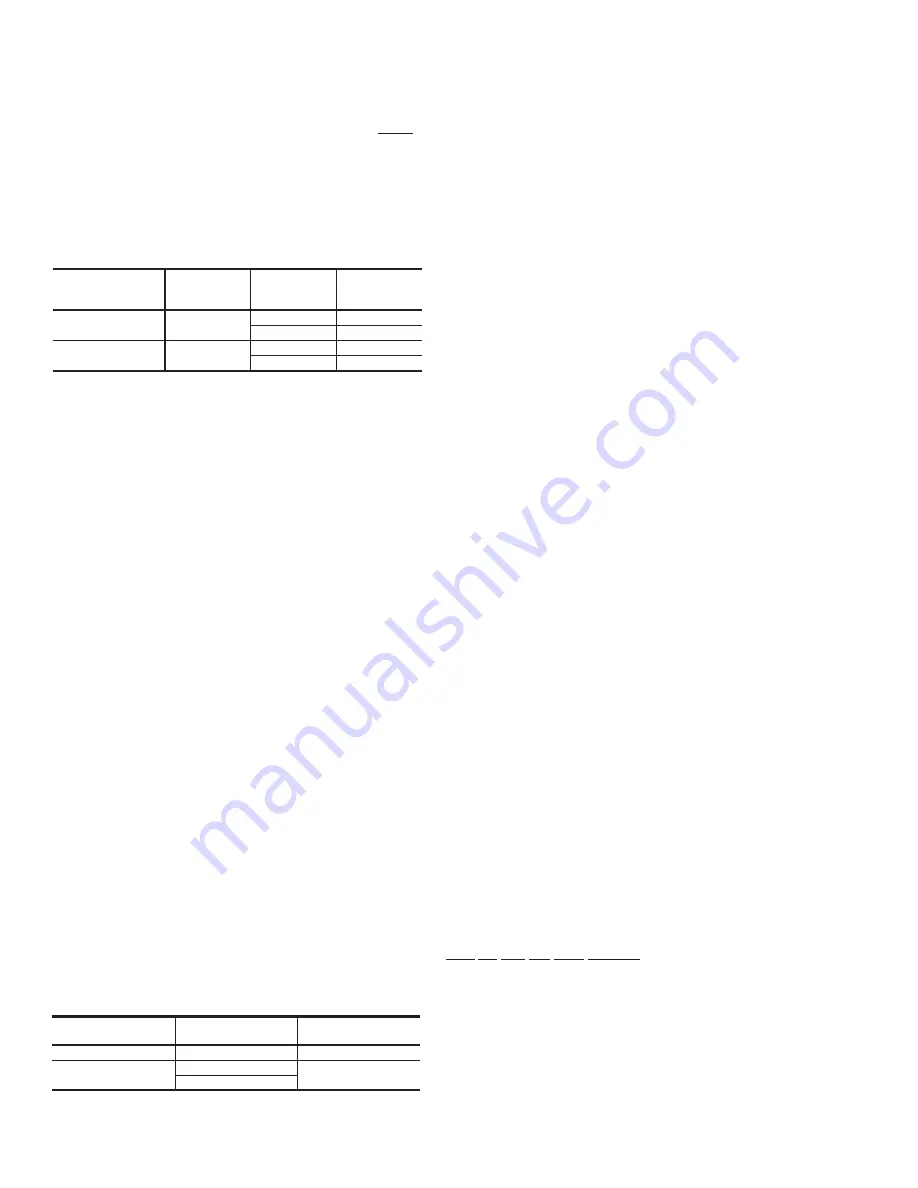
(29 feet x 8.0 psi/100 feet) .............................................2.3 psi
7 feet of 1-3/8" OD, type “L” copper tubing (horizontal)
(7 feet x 2.8 psi/100 feet) ...............................................0.2 psi
Fitting*....................................................................................0.5 psi
Vapor Line Pressure Drop = 3.0 psi
*
Determine the pressure drop of the fittings for each installation - DO NOT use the estimated
values as shown in the above examples.
Although longer vapor lines are permissible, friction losses ex-
ceeding3 psi (2
°
F) will reduce system capacity in both the cool-
ing and heating cycles.
SERVICE VALVES
These outdoor units have both vapor and liquid line service
valves.
Both valves are shipped from the factory front-seated and
closedwith the valve stem in the maximumclockwiseposition.
These servicevalves are the back-seatingtype and have a 1/4"
male flare accessport for evacuatingand chargingthe system.
Shrader access valves are provided on the compressor vapor
and discharge lines for pressure checking the system.
All access ports are sealed with a removable cap. Never re-
move a cap unless the valve is fully back-seated with its valve
stem in the maximum counter-clockwise position because the
refrigerant charge will be lost.
EXTENDING THE SERVICE PORTS
Refer to Fig.6:
1. Loosen the screws securing the service ports in shipping
position. (See FIG 6).
2. Push the service ports through the corner post.
3. Tighten the screws to secure the service ports for installation.
INSTALLATION
Since the condensing units are shipped with a holding charge
of Refrigerant-22, they can be checked for a refrigerant leak by
depressing the stem on either of the service ports that extend
through the cabinet. As soon as some internal pressure is re-
lieved release the stem. DO NOT release the entire holding
charge.
If the unit has already lost its holding charge, it should be leak
tested and the necessary repairs should be made. If the unit
has maintained its holding charge, you can assume that it has
no leaks and proceed with the installation.
CAUTION: When making a braze connection, wrap a wet rag
around all tubing inside the unit to prevent damage
to the other components.
Dry nitrogen should always be supplied through a
connection while it is being brazed or unbrazed
because the temperature required to make or
break a brazed joint is sufficiently high to cause
oxidation of the copper unless an inert atmos-
phere is provided. The flow of nitrogen should be
continued until the joint has cooled.
WARNING: The dry nitrogen must always be supplied through
a pressure regulating valve.
Before installing the liquid line between the outdoor and indoor
units, remove the copper disc from the liquid connectionon the
outdoor unit per the following procedure:
1.
Make sure the refrigerant in the line has been recovered
and that the liquid service valve on the unit is front-seated
and closed. The valve stem should be turned to its maxi-
mum clockwise position.
2.
Drill a small hole through the disc before unbrazing it to per-
mit a flow of dry nitrogen through the connection while it is
being unbrazed.
WARNING: This hole is also required to prevent the internal
pressure from building up as the disc is being un-
brazed and from blowing the disc off.
This warning applies to any disc being removed
from a service valve, coil connection, etc.
3.
Remove the cap from the 1/4" access port on the liquid line stop
valve.
4.
Connect a supply of dry nitrogen to this access port.
5.
Unbraze the copper disc from the liquid connection while
maintaining a minimum flow of dry nitrogen through the
connection.
After the disc has been removed,
1.
Burnish the external surfaces of the liquid connection on
the outdoor unit and the end of the field-supplied piping be-
ing used for the liquid line.
NOTE:
Clean surfaces are essential for a well brazed connec-
tion.
2. Carefully clean the internal surfaces of the above. Any par-
ticles left on these surfaces may lead to a future system
malfunction.
8
Unitary Products Group
035-15410-002-B-0404
System
Model
Refrigerant
Flow Rate,
4
(Lbs/Min)
Type L
Copper Tubing
(In. OD)
Friction
Loss,
5,6
(PSI/100 Ft.)
EFB090/FEH090
22.5
1-1/8
4.7
1-3/8
1.6
EFB120/FEH120
30.0
1-1/8
8.0
1-3/8
2.8
1
All horizontal vapor lines should be level since the refrigerant flows in both directions.
2
All vapor lines with a vertical rise exceeding 50 feet should have an intermediate trap. Small
radius traps will provide drainage points for the oil which is in the riser when the circuit is
deactivated. When the circuit is reactivated, the oil will be returned to the compressor more
quickly and in smaller slugs.
3
Every vapor riser greater than 5 feet in height should have a small radius trap at the bottom.
4
Based on Refrigerant-22 at the nominal cooling capacity of the system, a vapor temperature
of 40
°
F and a liquid temperature of 105
°
F. Since refrigerant flow rates will be a little lower at
the nominal heating capacity of each system, vapor line friction loss should always be based
on cooling operation.
5
Although vapor lines should be sized for a friction loss equivalent to a 2
°
F change in saturation
temperature (or approximately 3 psi), sizing the lines for the proper return of oil is more
important.
6
These friction losses do not include any allowance for fittings. Only use a 1-1/8" riser when
the indoor unit is above the outdoor unit.
TABLE 5
- VAPOR LINES
1,2,3
Refrigerant
Line
2
Line Size,
OD (In.)
Refrigerant Charge
(Lb/Ft)
Liquid
5/8
0.113
Vapor
1-1/8
0.013
1-3/8
1
Charges are based on 40
°
F suction temperature and 105
°
F liquid temperature.
2
Type “L” copper tubing.
TABLE 6
- REFRIGERANT LINE CHARGE
1