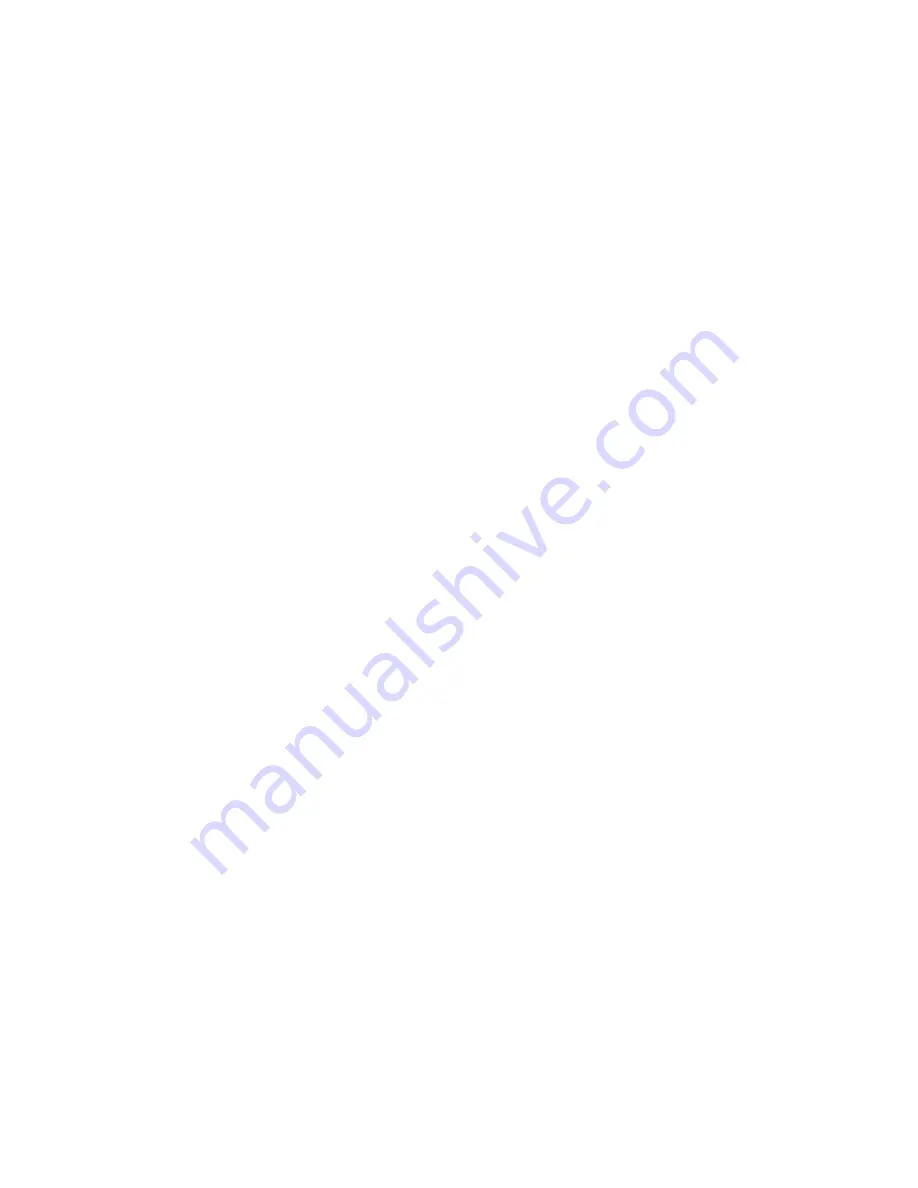
©York Survey Supply Centre 2018
Ref:.. \operat98\instructions 18\354920.qxp 05-01-18
Protimeter Hygromaster
with Humidity Box or Humidity Sleeves
Moisture Related Damage in Floors
Excessive moisture in concrete floor slabs and screeds can lead to the following types of failure or
damage:
• Adhesion failure between floor covering and concrete slab. When the critical moisture level for
a given covering/adhesive/concrete is passed, bond strength drops sharply.
• Vinyl floor covering movement. Dampness in concrete may aggravate alkali related
dimensional changes in sheet vinyl.
• Emissions of harmful substances from floor covering materials. Examples include the emission
of ammonia from some screeds, the emission of formaldehyde from chipboard and the
degradation of certain plasticisers in sheet vinyl.
• Excessive expansion of solid wood floor coverings and the decay and degradation of wood
based floorboards.
These problems tend to occur when the moisture content of the concrete or screed exceeds the
critical moisture content of the materials that are in contact with it. A material’s critical moisture
content can be expressed as an equilibrium relative humidity (ERH) value or a moisture content
(%mc) value. ERH values are particularly suitable for this purpose because they convey the
moisture condition of the material in question - its degree of wetness. Whilst the critical moisture
content values vary for different materials, the problems outlined above are avoided when
substrates have an ERH below 75%.
Humidity and Relative Humidity (%rh)
Humidity denotes the presence of water vapour - the gaseous form of water - in air and other
gases. The expression relative humidity (rh%) of air expresses the degree of saturation with water
vapour at a given temperature. Saturated air - having 100%rh - contains its full capacity of water
vapour. Relative humidity measurements are particularly appropriate for assessing the moisture
condition of environments. Similarly, equilibrium relative humidity (ERH) measurements are very
useful for assessing if materials are in a wet or dry condition. ERH values of materials are
obtained by measuring the %rh of a pocket of air deemed to be in moisture equilibrium with the
material under investigation.
Guidance for Measuring Moisture in the ERH of Screeds and Slabs
The GE Protimeter Hygromaster L and GE Protimeter MMS instruments may be used to measure
the ERH of screeds and floor slabs when they are used with a GE Protimeter extension lead and a
GE Protimeter humidity box or GE Protimeter humidity sleeves. Please refer to the GE Protimeter
Hygromaster L and MMS user instructions for specific information on using these instruments.
1. ERH Test Procedure - using GE Protimeter Humidity Sleeves
i. Drill 16mm (5/8”) diameter clearance holes to a nominal depth of 50mm (2”) at the required
points of measurement (POMs).
ii. Position a plastic membrane over the hole and push a GE Protimeter humidity sleeve through
the membrane and into the hole. Ensure that the flange of the humidity sleeve is flush with the
floor surface and that the humidity sleeve cap is firmly in position, to make an airtight seal.
iii. Leave for at least 24 hours to ensure moisture equilibrium conditions are reached within the
humidity sleeve. If in use, switch off any accelerated drying apparatus at least 4 days before
taking final readings.
iv. The ERH reading is made with the Hygrostick sensor supplied with the GE Protimeter
Hygromaster L instrument. Hygrosticks are fitted with a soft conical sealing sleeve. Ensure that
the tip of the Hygrostick protrudes fully from the narrow end of the sealing sleeve.
v. Remove the humidity sleeve cap and push the Hygrostick assembly into the humidity sleeve
and twist firmly to seal. Ideally, leave the Hygrostick in the hole for at least 30 minutes before
taking the first reading.
vi. Connect the Hygrostick to the Hygrometer L instrument with the GE Protimeter extension lead.
vii. Measure the %rh in the hole; this is the ERH value of the floor slab.
2. ERH Test Procedure - using GE Protimeter Humidity Box
This test procedure follows the guidelines given in the British Standards BS 5325 and BS 8203.
If full BS procedure compliance is required, please refer to these standards for comprehensive
details.
i. Place the humidity box on the surface at the required point of measurement (POM) and put a
brick or similar object on top to ensure it is not inadvertently moved. Ensure the plug is in the
hole in the side of the box. If the surface is smooth, no additional sealing is required around the
rim of the box. If the surface has a rough texture, seal the box-surface interface with an inert
sealant such as plasticine.
ii. If in use, switch off any accelerated drying apparatus at least 4 days before taking readings.
Thereafter, for un-bonded screeds of thickness 50 - 75mm (2 - 3”) where a damp-proof
membrane has been placed between the base and screed, leave the humidity box in position
for at least 24 hours to ensure moisture equilibrium is reached within the box before taking
readings. For bonded screeds and direct finish base slabs allow a minimum of 72 hours to
pass before taking readings. Note that it may take many weeks for equilibrium conditions to be
reached within a humidity box on the surface when the slab thickness exceeds 200mm (8”)
and/or it has a power floated finish.
iii. The ERH reading is made with the Hygrostick sensor supplied with the GE Protimeter
Hygromaster L instrument. Hygrosticks are fitted with a soft conical sealing sleeve. Ensure that
the tip of the Hygrostick protrudes fully from the narrow end of the sealing sleeve.
iv. Remove the humidity box plug and push the Hygrostick assembly into the hole and twist firmly
to seal. Ideally, leave the Hygrostick in the humidity box for at least 30 minutes before taking
the first reading.
v. Connect the Hygrostick to the Hygrometer L instrument with the GE Protimeter extension lead.
vi. Measure the %rh in the humidity box; assuming equilibrium conditions have been reached, this
is the ERH value of the screed or slab.