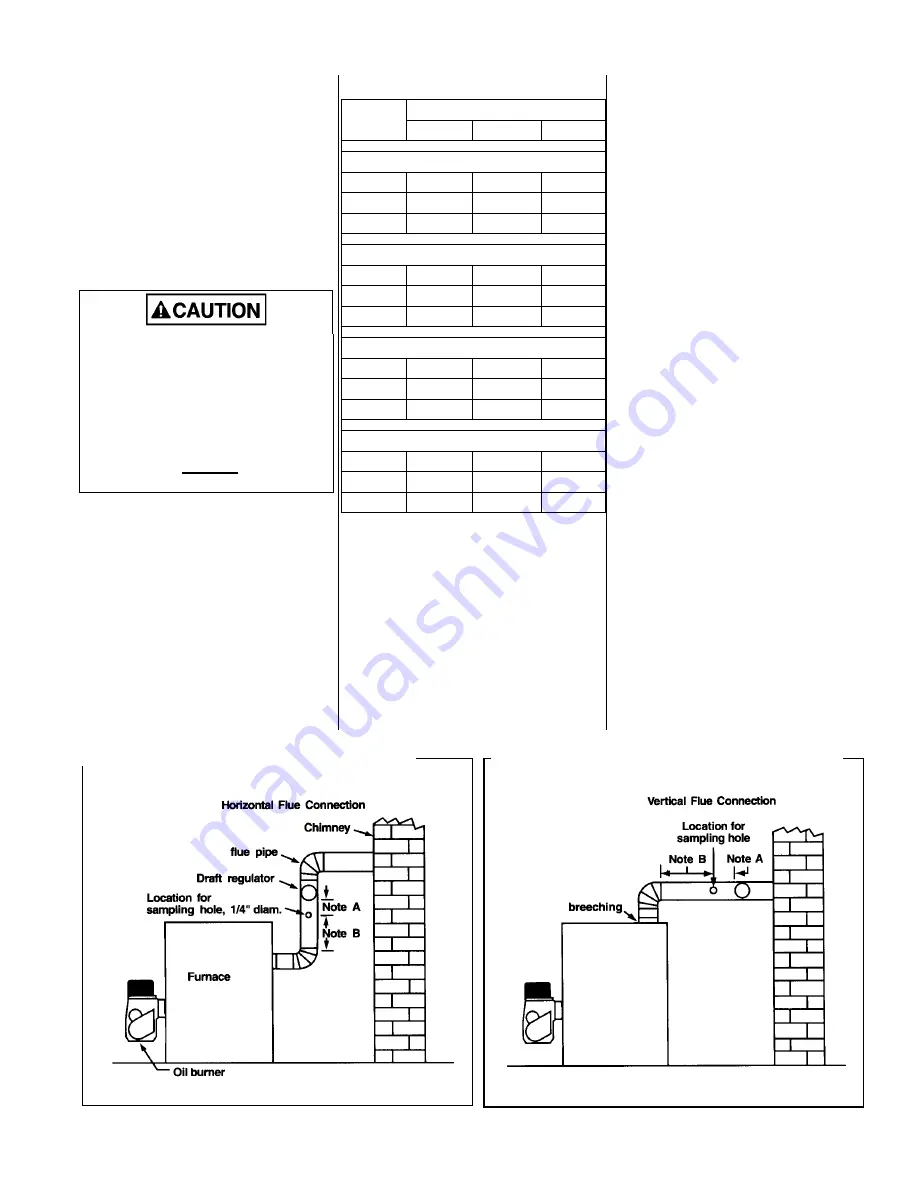
8
OIL BURNER
P*HMX and P*LBX furnaces are
equipped with Beckett AFG Series oil
burners. The oil burner must align prop-
erly with the cerafelt fiber chamber (fire-
pot). The cerafelt fiber chamber is initially
quite soft, but hardens and becomes
quite brittle after the first firing. The fire-
pot is held in place by a retaining
bracket; however, it is possible for the
firepot to shift if subjected to rough han-
dling during transit.
BEFORE OPERATING THE FUR-
NACE CHECK BURNER ALIGNMENT
WITH COMBUSTION CHAMBER.
THE END CONE OF THE AIR TUBE
MUST BE CENTRED TO THE AC-
COMODATING RING PROVIDED IN
THE DESIGN OF THE COMBUSTION
CHAMBER. ADJUST ALIGNMENT AS
NECESSARY BEFORE THE FIRST
FIRING.
OIL BURNER NOZZLES
P2HMX12F08001 and P3LBX12F08001
furnaces are certified for multiple firing
rates, ranging from approximately 60,000
to 80,000 BTU/hr. The
P3HMX14F10001, P3HMX20F12001
and P3LBX14F12001 furnaces are certi-
fied for multiple firing rates of approxi-
mately 85,000 115,000 BTU/hr. By
changing the oil burner nozzle within the
specific Model Range, and temperature
rise, the furnace may be fired at an ideal
rate for a wide range of structures.
Table 5: Nozzles
NOZZLE
OUTPUT
BTU/Hr.
Delavan Hago Stienen
P2HMX12F08001
58,000
0.50/70°W 0.50/70°SS 0.50/70°Q
73,000
0.65/70°W 0.65/70°SS 0.65/70°Q
79,000
0.70/70°W 0.70/70°SS 0.70/70°Q
P3LBX12F08001
57,000
0.50/70°W 0.50/70°SS 0.50/70°Q
75,000
0.65/70°W 0.65/70°SS 0.65/70°Q
79,000
0.70/70°W 0.70/70°SS 0.70/70°Q
P3HMX14F10001 / P3HMX20F12001
87,000
0.75/70°W 0.75/70°SS 0.75/70°Q
100,000
0.85/70°W 0.85/70°SS 0.85/70°Q
118,000
1.00/70°W 1.00/70°SS 1.00/70°Q
P3LBX14F12001
85,000
0.75/70°W 0.75/70°SS 0.75/70°Q
96,000
0.85/70°W 0.85/70°SS 0.85/70°Q
113,000
1.00/70°W 1.00/70°SS 1.00/70°Q
BURNER ELECTRODES
Correct positioning of the electrode tips
with respect to each other, to the fuel oil
nozzle, and to the rest of the burners is
essential for smooth light ups and proper
operation. The electrode tips should be
adjusted to a gap of 5/32”, 1/16” ahead
of the nozzle, 5/16” above the centerline
of the nozzle. The “Z” dimension (front
edge of the burner head to the front face
of the nozzle is 1-1/8 inches.
Electrode positioning should be checked
before the first firing of the furnace.
The electrode porcelains should be free
of cracks, the electrode tips should be
tapered and free of burrs, and the con-
tact rods must be clean and be in firm
contact with the ignition transformer con-
tact springs. The electrodes must not
come into contact with the burner head.
OIL BURNER SET-UP
The burner air supply is adjusted to
maintain the
fuel to air
ratio
to obtain
ideal combustion conditions. A lack of air
causes "soft" and "sooty" flames, result-
ing in soot build-up throughout the heat
exchanger passages. Excess combus-
tion air causes a bright roaring fire and
high stack temperatures resulting in poor
fuel efficiency.
PREPARATIONS:
Drill a ¼” test port in the venting, ideally
at least 2 flue pipe diameters away from
the furnace breeching, if venting horizon-
tally from the furnace, (typically P3LBX)
or from the flue pipe elbow if venting
vertically (typically P*HMX) before reach-
ing the furnace. (see Figures 4 and 5).
The test port will allow flue gas samples
to be taken and stack temperatures to be
measured.
Before starting the burner, check the
burner alignment with the combustion
chamber (fire pot), check that the correct
nozzle is tightened into place, and that
the burner electrodes are properly posi-
tioned.
Fig. 4: Horizontal Smoke Test Port Location
Fig. 5: Vertical Smoke Test Port Location
Содержание P2HMX12F08001
Страница 16: ...16 APPENDIX B WIRING DIAGRAM ...