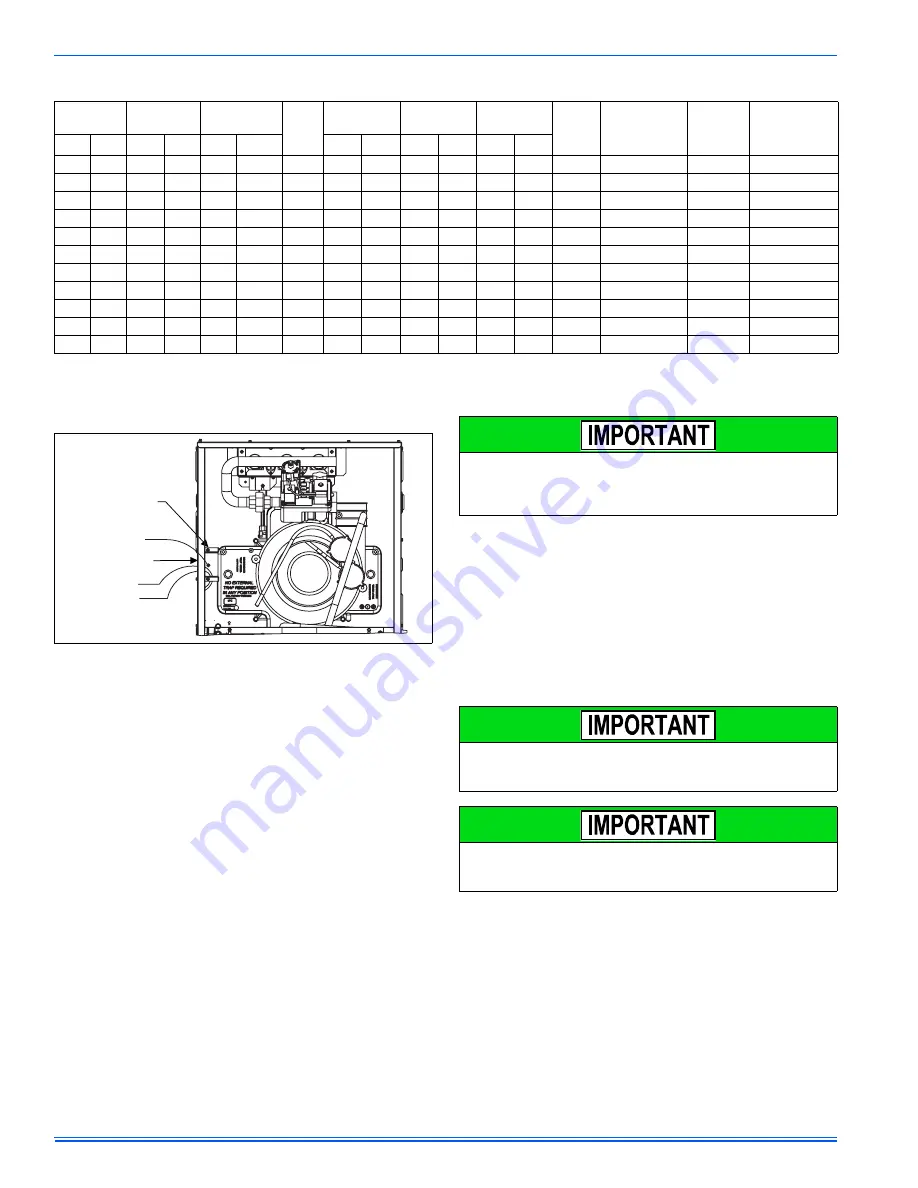
1083287-UIM-A-0114
12
Johnson Controls Unitary Products
Annual Fuel Utilization Efficiency (AFUE) numbers are determined in accordance with DOE Test procedures.
Wire size and over current protection must comply with the National Electrical Code (NFPA-70-latest edition) and all local codes.
The furnace shall be installed so that the electrical components are protected from water.
SUPPLY VOLTAGE CONNECTIONS
1.
Provide a power supply separate from all other circuits. Install over-
current protection and disconnect switch per local/national electrical
codes. The switch should be close to the unit for convenience in
servicing. With the disconnect or fused switch in the OFF position,
check all wiring against the unit wiring label. Refer to the wiring dia-
gram in this instruction.
2.
Remove the wiring box cover screws. Route all power wiring
through a conduit connector or other proper bushing that is field
installed into the unit opening and the junction box. In the junction
box there is a black wire, a white wire and a green ground screw.
Connect the power supply as shown on the unit’s wiring label on
the inside of the blower compartment door or the wiring schematic
in this section. Connect the black wire to L1 (hot) from the power
supply. Connect the white wired to neutral. Connect the ground wire
(installer-supplied) to the green (equipment ground) screw. An
alternate wiring method is to use a field-provided 2” (5.1 cm) x 4”
(10.2 cm) box and cover on the outside of the furnace. Route the
furnace leads into the box using a protective bushing where the
wires pass through the furnace panel. After making the wiring con-
nections replace the wiring box cover and screws. Refer to Figure
17.
3.
The furnace's control system requires correct polarity of the power
supply and a proper ground connection. Refer to Figure 17.
LOW VOLTAGE CONTROL WIRING CONNECTIONS
Install the field-supplied thermostat by following the instructions that
come with the thermostat. With the thermostat set in the OFF position
and the main electrical source disconnected, connect the thermostat
wiring from the wiring connections on the thermostat to the terminal
board on the ignition module, as shown in Figure 17. Electronic thermo-
stats may require the common wire to be connected. Apply strain relief
to thermostat wires passing through cabinet. If air conditioning equip-
ment is installed, use thermostat wiring to connect the Y and C termi-
nals on the furnace control board to the proper wires on the condensing
unit (unit outside).
The 24-volt, 40 VA transformer is sized for the furnace components
only, and should not be connected to power auxiliary devices such as
humidifiers, air cleaners, etc. The transformer may provide power for an
air conditioning unit contactor.
Table 6:
Ratings & Physical / Electrical Data
Input
Output
Nominal
Airflow
AFUE
%
Air Temp.
Rise
Max. Outlet
Air Temp
Blower
Blower
Size
Max
Over-Current
Protect
Total Unit
Amps
Min. wire Size
(awg) @ 75 ft
one way
MBH
kW
MBH
kW
CFM m
3
/min
°F
°C
°F
°C
HP
Amps
40
11.7
38
11.1
800
22.7
95.5
30-60 17-33
160
71.1
1/3
4.8
11x8
15
8.0
14
60
17.6
57
16.7
1000
28.3
95.5
30-60 19-36
160
71.1
1/2
7.07
11x8
15
10.0
14
60
17.6
57
16.7
1200
34.0
95.5
30-60 19-36
160
71.1
1/2
7.07
11x8
15
10.0
14
80
23.4
76
22.3
1200
34.0
95.5
35-65 19-36
165
73.9
1/2
7.07
11x8
15
10.0
14
80
23.4
76
22.3
1600
45.3
95.5
35-65 19-36
165
73.9
3/4
8.8
11x10
15
11.5
14
80
23.4
76
22.3
2200
62.3
95.5
35-65 19-36
165
73.9
1
14.5
11x11
20
17.0
12
100
29.3
95
27.8
1600
45.3
95.5
35-65 19-36
165
73.9
3/4
8.8
11x10
15
11.5
14
100
29.3
95
27.8
2000
56.6
95.5
35-65 19-36
165
73.9
1
14.5
11x11
20
17.0
12
120
35.1
114
33.4
1600
45.3
95.5
40-70 22-39
170
76.7
3/4
8.8
11x10
15
11.5
14
120
35.1
114
33.4
2000
56.6
95.5
35-65 19-36
165
73.9
1
14.5
11x11
20
17.0
12
130
38.1 123.5 36.2
2000
56.6
95.5
45-75 28-44
175
79.4
1
14.5
11x11
20
17.0
12
FIGURE 17:
Electrical Wiring
Electrical Entry
Junction
Box
L1-Hot
Neutral
Connect ground
lead to screw
BLK
WHT
The power connection leads and wiring box may be relocated to the
opposite side of the furnace. Remove the screws and cut wire tie
holding excess wiring. Reposition on the opposite side of the furnace
and fasten using holes provided.
Set the heat anticipator in the room thermostat to 0.4 amps. Setting it
lower will cause short cycles. Setting it higher will cause the room
temperature to exceed the set points.
Some electronic thermostats do not have adjustable heat anticipa-
tors. They should be set to six cycles per hour. Follow the thermostat
manufacturer's instructions.