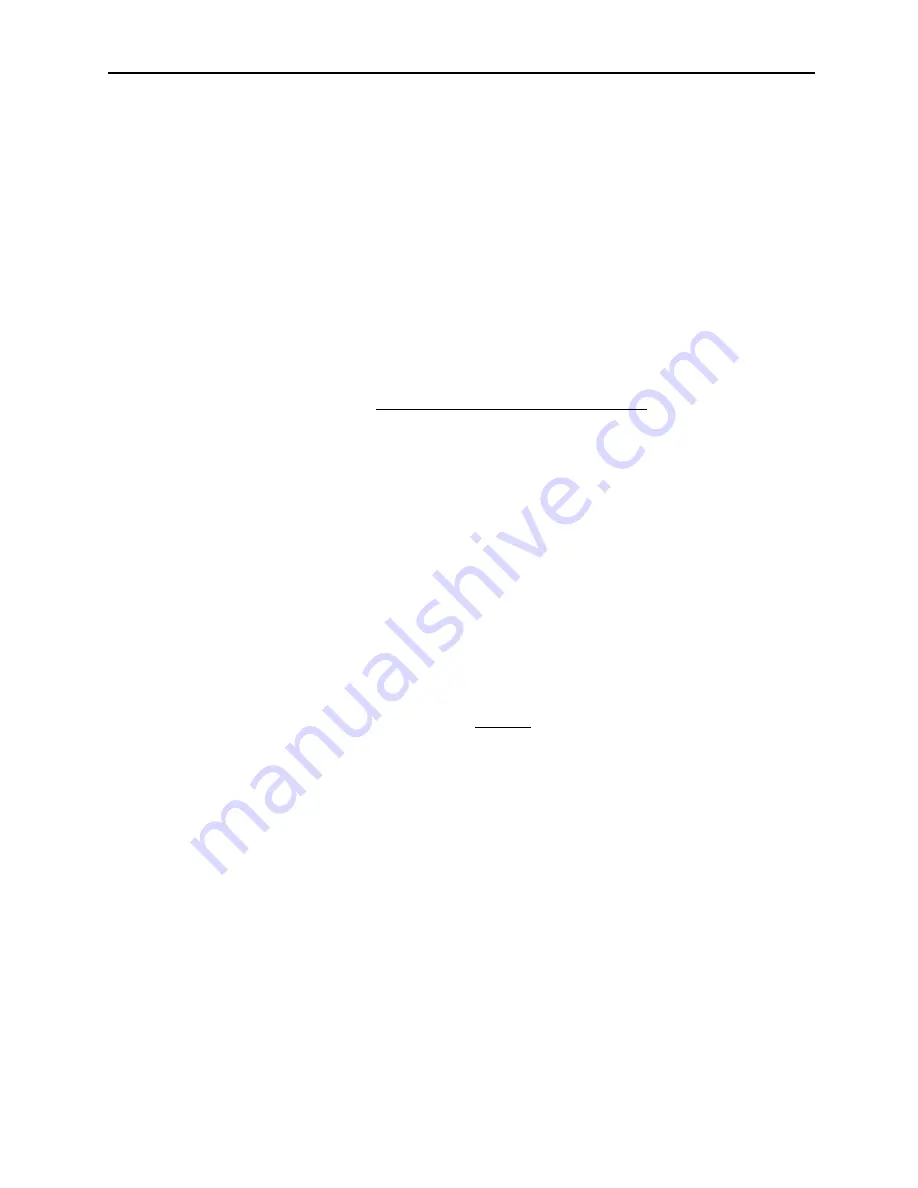
Sigma II User’s Manual
Chapter 6: Servo Adjustment
6 - 37
Position Control
Parameters
The following parameters are used.
•
Speed Loop Gain (Pn100)
This parameter is used for determining the response speed of the speed loop. For
the best response, set this parameter as high as possible, without exceeding the
point where the mechanical system vibrates. The value of speed loop gain is the
same as the set value of Pn100 if the inertia ratio set in Pn103 is correct.
Speed loop gain Kv = Set value of Pn100 (Hz)
Set Pn103 to the following value:
Note:
In the case of manual adjustments of parameters, the user must set the value of parameter Pn103. The
inertia ratio can be obtained if the servo gain constant is written with parameter Fn007 after auto-tun-
ing has been performed. For details regarding Fn007, refer to
6.3 Auto-Tuning.
•
Speed Loop Integral Time Constant (Pn101)
The speed loop has an integral element so that the speed loop can respond to
minute inputs. This integral element delays the operation of the servo system,
resulting in longer positioning settling time. As the value of the time constant
increases, the response becomes slower.
If the load inertia is large or the mechanical system is likely to vibrate, make sure
that the speed loop integral time constant is large enough. Use the following for-
mula to calculate the optimum time constant.
Where: T
i
= Integral time constant [s]
K
v
= Speed loop gain (calculated from the above) [Hz]
•
Torque Reference Filter Time Constant (Pn401)
If the mechanical system uses ball screws, torsional resonance may result. In
this case, the oscillation noise will be a high-pitched tone. The oscillation may
be minimized by increasing the time constant of the torque reference filter. Like
the integral time constant, this filter causes a delay in the operation of the servo
system. Therefore, this constant must not be set to an excessively large value.
•
Position Loop Gain (Pn102)
The responsiveness of the servo system is determined by the position loop gain.
The response increases if the position loop gain is set to a high value, and the
time required for positioning will be shortened. In order to set the position loop
gain to a high value, the rigidity and natural frequency of the mechanical system
Pn103 Setting Value =
×
100%
Motor shaft reflected load inertia (J
L
)
Servomotor rotor inertia (J
M
)
T
i
≥
2.3
×
1
2π ×
K
v
Содержание SGMAH
Страница 1: ...Sigma II Series Servo System User s Manual...
Страница 2: ......
Страница 4: ...ii This page intentionally left blank...
Страница 6: ...iv This page intentionally left blank...
Страница 10: ...Sigma II User s Manual Table of Contents Preface viii Notes...
Страница 17: ...Sigma II User s Manual Table of Contents Preface xv C 6 Torque Control Mode C 9...
Страница 18: ...Sigma II User s Manual Table of Contents Preface xvi...
Страница 38: ...Sigma II User s Manual Chapter 2 Installation 2 10 NOTES...
Страница 472: ...Sigma II User s Manual Appendix C Examples of Standard Connections C 10 Notes...
Страница 487: ......