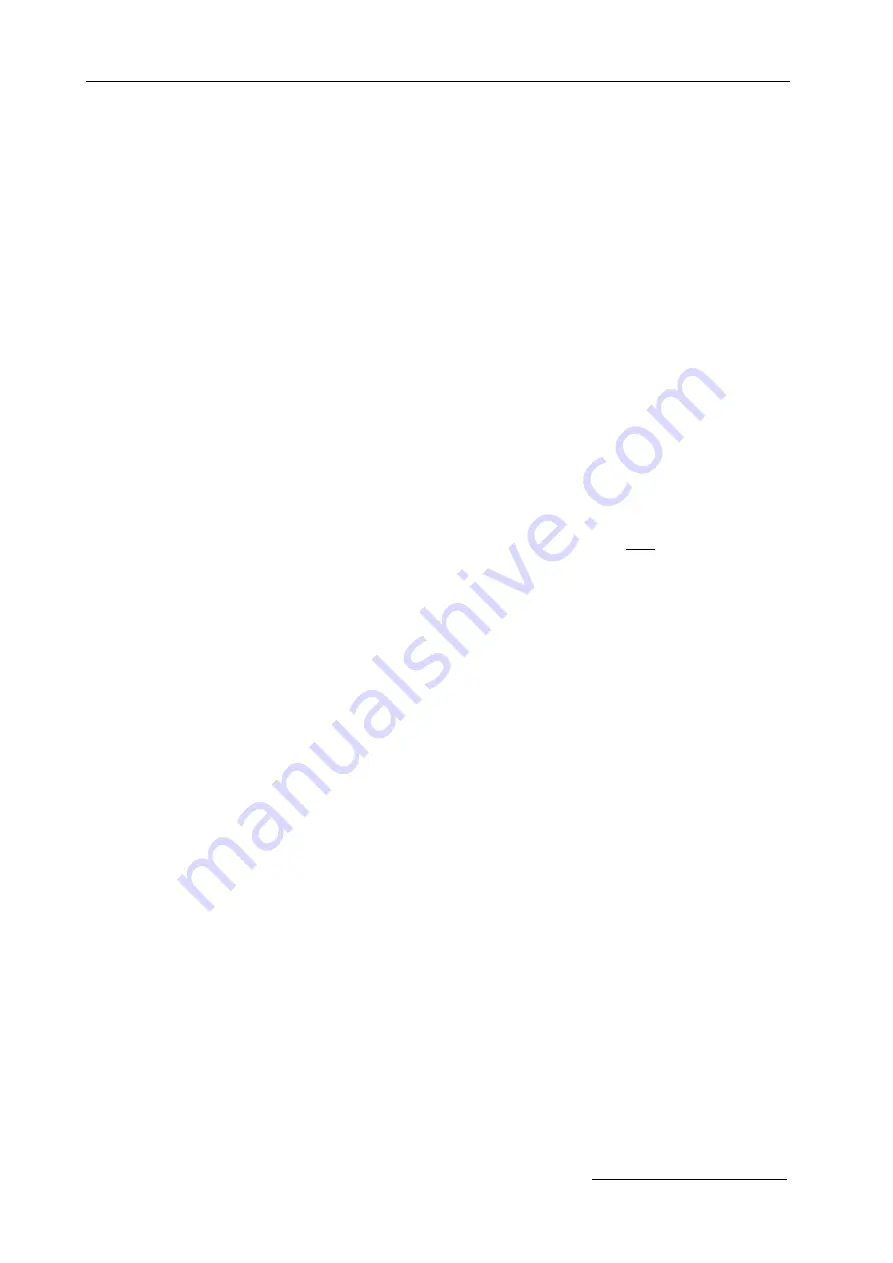
Yaskawa Electric America, Inc.
Installation Guide IG.E7B.02 Rev: 04-11
Date: 11-1-04 Page 44 of 46
Table 1 is also used to document parameters that have been factory set to typical values for fan and pump
applications. These parameters [
b1-08
,
L4-05
,
L5-01
,
L5-03
,
o2-03
and
o3-02
] may be changed to meet the
needs of the specific application.
4.
From the
ADV/PRGM
menu, press
DATA/ENTER
, go to parameter
E1-01
and enter the nominal input
voltage that the Drive will receive in this specific application. The overall voltage classification of the Drive
cannot be changed by this parameter. However, the input voltage should be adjusted within the range avail-
able for the given voltage “class” of the Drive to match the input voltage level normally found on the jobsite.
For example, 480 VAC class Drives may be employed on nominal three phase voltage distribution systems
of: 380, 400, 415, 440, 460 or 480 VAC. The factory default values may need to be changed to meet the needs
of the application distribution voltage.
5.
From parameter
E1-01
, use the ESC,
and
DATA/ENTER
keys as necessary, to go to parameter
E2-01
and enter the Motor Rated Current. Set this parameter to the motor rated Full Load Amps (FLA) shown on
the motor nameplate. This is essential for proper Drive operation and motor overload protection. [
Note:
Do
not include the “service factor” amps.]
6.
Press the
MENU
key to return to the
DRIVE
menu and the same operational status LED configuration
described in step 2 above. The alpha/numeric display will show the speed command frequency.
To start the motor in Drive mode, press the
HAND
key. The
DRIVE Run
LEDs (red and green) and the
HAND
LED (amber) will light and the Drive output will ramp up to “6 HZ.” Verify that motor rotation is
correct.
If the direction of motor rotation is wrong, press the
OFF
key and turn the Power
OFF
! Wait for the red
CHARGE
LED (near the Drive power terminals) to go out. When it does, swap the wires for
T1
&
T2
on the
output terminals of the motor Overload Relay. Tighten the terminal lugs, reapply the power, press the
HAND
key and re-check the rotation direction.
7.
With correct motor rotation, press the
MENU
key, if necessary, to return to the
DRIVE
menu. Press
DATA/
ENTER
(as needed to get “F” flashing) then using the
and
keys, manually run the Drive throughout
its entire speed range, while observing operation. If excessive vibration of the driven load is noted at specific
frequencies (speeds), the Jump Frequency function may be used to eliminate this vibration, by programming
d3-01
through
d3-04
. Press the
OFF
key.
8.
Determine whether the remote speed command is a 0-10 VDC or a 4-20 mA signal. The positive side of the
signal should be connected to terminal
TB3-3
of the E7B terminal strip. The “common” of the remote speed
command signal should be connected to terminal
TB3-1
of the E7B. See the connection diagram on page 1 of
the E7B Bypass unit schematic E7B-10. [
Note:
The factory default is 4-20 mA, to change to 0 to 10 VDC
adjust parameter
H3-08
to “0: 0-10VDC” and move E7B DIP switch
S1-2
, on the terminal PCB to the OFF
position (toward the unit rear).]
9.
For the Auto mode, request a run command and speed command signal from the building automation system
to confirm remote (auto) operation.
10. Press the
AUTO
key, the
DRIVE Run
LEDs (red and green), the
AUTO
LED (green) and
AUTO Run
LED
(green) will light and the Drive output will ramp up to the Auto mode speed command. Observe if the remote
speed command can achieve the minimum and maximum speeds desired. If not, perform the following: - See
Chapter 5 of TM.E7B.01.
For 0-10 VDC input at Terminal
TB3-3
1.
With no input, adjust the Bias (
H3-11
setting) until an output of “0.0 Hz” is obtained.
2.
With full scale input, adjust the Gain (
H3-10
setting) until an output of “60.0 Hz” (or other desired
maximum frequency) is obtained.
For 4-20 mA input at Terminal
TB3-3
1.
With 4 mA input, adjust Bias (
H3-11
setting) until an output of “0.0 Hz” is obtained.
2.
With 20 mA input, adjust Gain (
H3-10
setting) until an output of “60.0 Hz” (or other desired
maximum frequency) is obtained.
Содержание E7B T Series
Страница 2: ......
Страница 48: ...Yaskawa Electric America Inc Installation Guide IG E7B 02 Rev 04 11 Date 11 1 04 Page 46 of 46 ...
Страница 49: ......