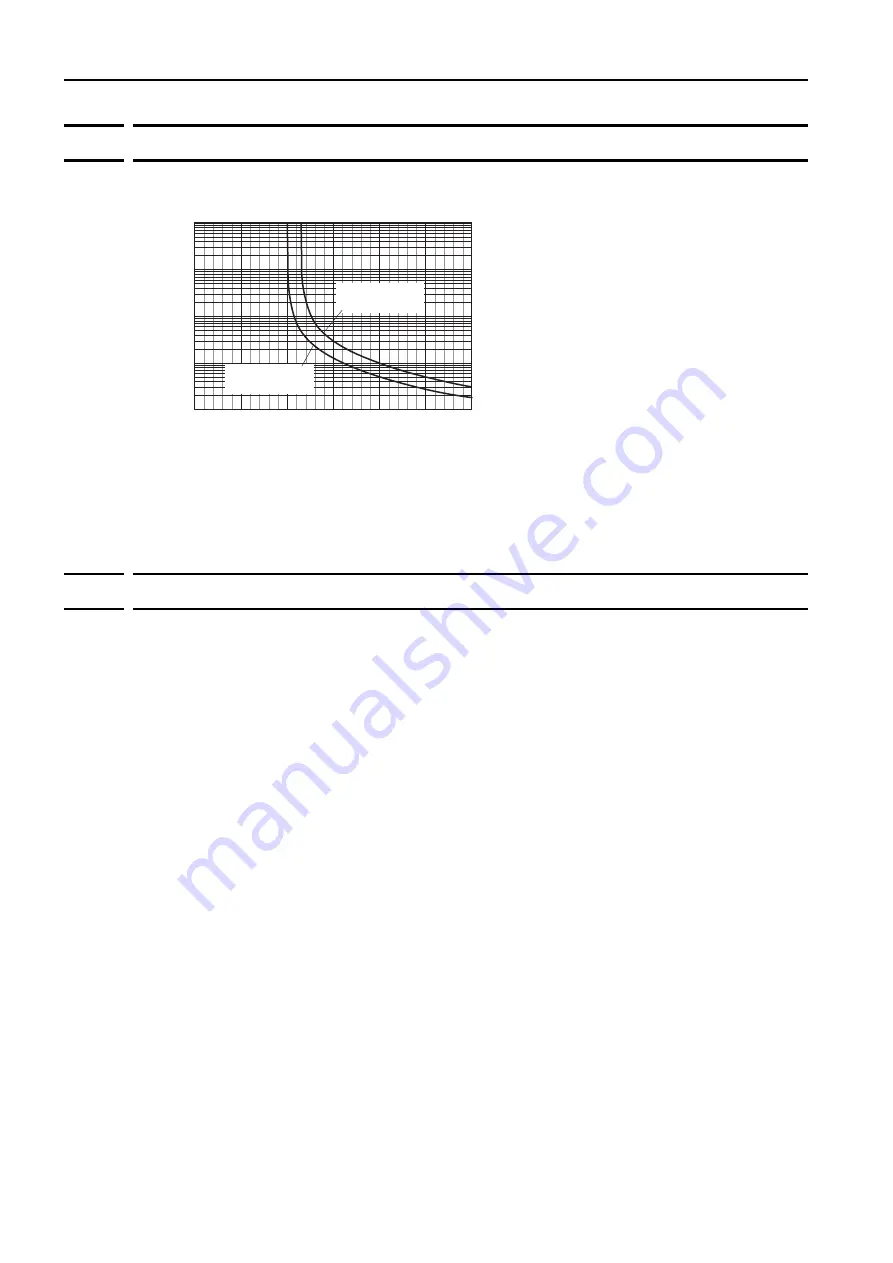
6.2 Specifications and Ratings
6.2.5 Servomotor Overload Protection Characteristics
6-8
6.2.5
Servomotor Overload Protection Characteristics
The overload detection level is set for hot start conditions with a Servomotor surrounding air
temperature of 40
°
C.
Note: The above overload protection characteristics do not mean that you can perform continuous duty operation
with an output of 100% or higher.
Use the Servomotor so that the effective torque remains within the continuous duty zone given in
6.2.6
Load Moment of Inertia
The load moment of inertia indicates the inertia of the load. The larger the load moment of iner-
tia, the worse the response. If the moment of inertia is too large, operation will become unsta-
ble.
The allowable size of the load moment of inertia (
J
L
) for the Servomotor is restricted. Refer to
on page 6-4. This value is provided strictly as a
guideline and results depend on Servomotor driving conditions.
An Overvoltage Alarm (A.400) is likely to occur during deceleration if the load moment of inertia
exceeds the allowable load moment of inertia. SERVOPACKs with a built-in regenerative resis-
tor may generate a Regenerative Overload Alarm (A.320). Perform one of the following steps if
this occurs.
•
Reduce the torque limit.
•
Reduce the deceleration rate.
•
Reduce the maximum motor speed.
•
Install an External Regenerative Resistor if the alarm cannot be cleared using the above
steps.
Regenerative resistors are not built into SERVOPACKs for 400-W Servomotors or smaller Ser-
vomotors.
Even for SERVOPACKs with built-in regenerative resistors, an External Regenerative Resistor is
required if the energy that results from the regenerative driving conditions exceeds the allow-
able loss capacity (W) of the built-in regenerative resistor.
Torque reference (percent of rated torque)
(%)
0
50
100
150
200
250
300
10000
1000
100
10
1
Motor speed of
10 min
-1
or higher
Motor speed of
less than 10 min
-1
Detection time (s)