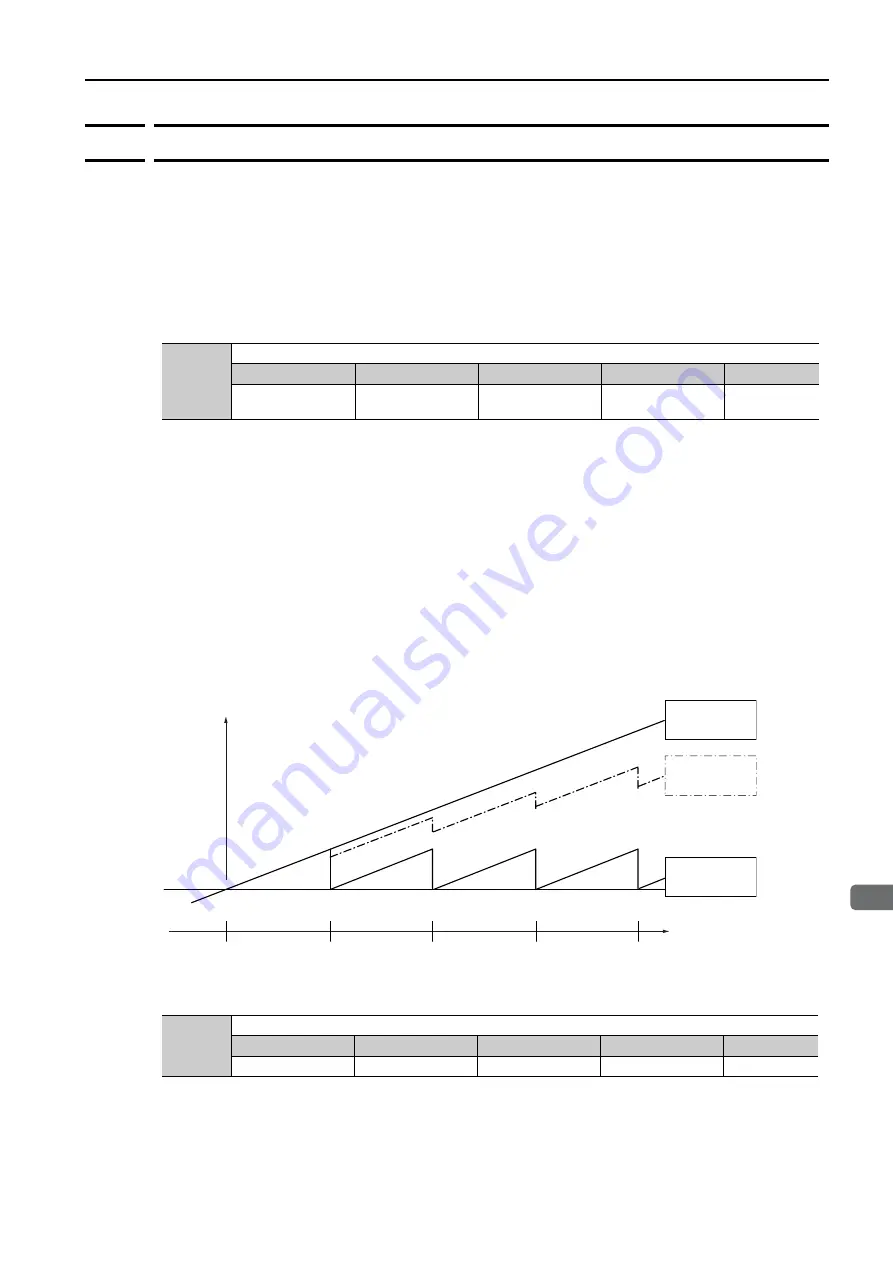
10.3 Parameter Settings for Fully-Closed Loop Control
10.3.6 Alarm Detection Settings
10-9
10
Fully-Closed Loop Contr
ol
10.3.6
Alarm Detection Settings
This section describes the alarm detection settings (Pn51B and Pn52A).
Pn51B (Motor-Load Position Deviation Overflow Detection
Level)
This setting is used to detect the difference between the feedback position of the Servomotor
encoder and the feedback load position of the external encoder for fully-closed loop control.
If the detected difference exceeds the setting, an A.d10 alarm (Motor-Load Position Error Over-
flow) will be output.
Note: If you set this parameter to 0, A.d10 alarms will not be output and the machine may be damaged.
Pn52A (Multiplier per Fully-closed Rotation)
Set the coefficient of the deviation between the Servomotor and the external encoder per Ser-
vomotor rotation.
This setting can be used to prevent the Servomotor from running out of control due to damage
to the external encoder or to detect belt slippage.
Setting Example
Increase the value if the belt slips or is twisted excessively.
If this parameter is set to 0, the external encoder value will be read as it is.
If you use the default setting of 20, the second rotation will start with the deviation for the first
Servomotor rotation multiplied by 0.8.
Related Parameter
Pn51B
Motor-Load Position Deviation Overflow Detection Level
Setting Range
Setting Unit
Default Setting
When Enabled
Classification
0 to
1,073,741,824
1 reference unit
1000
Immediately
Setup
Pn52A
Multiplier per Fully-closed Rotation
Setting Range
Setting Unit
Default Setting
When Enabled
Classification
0 to 100
1%
20
Immediately
Setup
Pn52A = 0
Pn52A = 100
Pn52A = 20
Deviation between Servomotor and external encoder
Large
Number of Servomotor rotations
4th rotation
3rd rotation
1st rotation
2nd rotation
Small