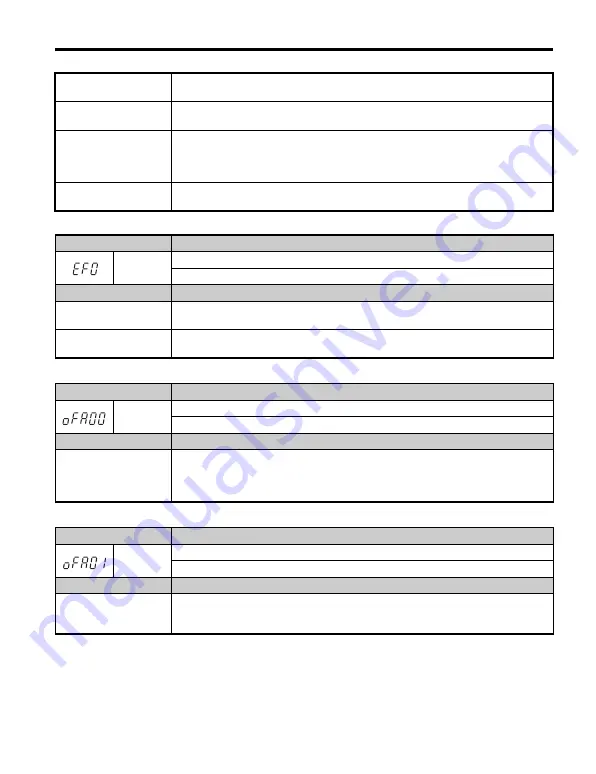
9 Troubleshooting
YASKAWA ELECTRIC
TOBP C730600 59B V1000 Option SI-EM3/V Installation Manual
43
The option is not properly
connected to the drive.
Reinstall the option.
Option is damaged
If there are no problems with the wiring and the error continues to occur, replace the
option.
Control Connection
Time-out.
• Option did not receive a command (write to Modbus address 01H) within the time-out
period specified in parameter F7-16
• Check value programmed in F7-16
• Check if PLC program stopped running
Duplicate IP Address
The option shares IP Address with at least one other node.
Check the setting value of F7-03 and F7-04 (IP Address).
Keypad Display
Fault Name
EF0
Option Card External Fault
The alarm function for an external device has been triggered.
Cause
Possible Solutions
An external fault was
received from the PLC.
1. Remove the cause of the external fault.
2. Reset the external fault input from the PLC.
Problem with the PLC
program
Check the PLC program.
Keypad Display
Fault Name
oFA00
Option Card Fault
Option is not properly connected.
Cause
Possible Solutions
The option card installed
into port CN5-A is
incompatible with the
drive.
Connect the option to the correct option port.
Note: PG option cards are supported by option ports CN5-B and CN5-C only.
Keypad Display
Fault Name
oFA01
Option Card Fault
Option is not properly connected.
Cause
Possible Solutions
The option connected to
option port CN5-A was
changed during run.
De-energize the drive and plug the option into the drive according to