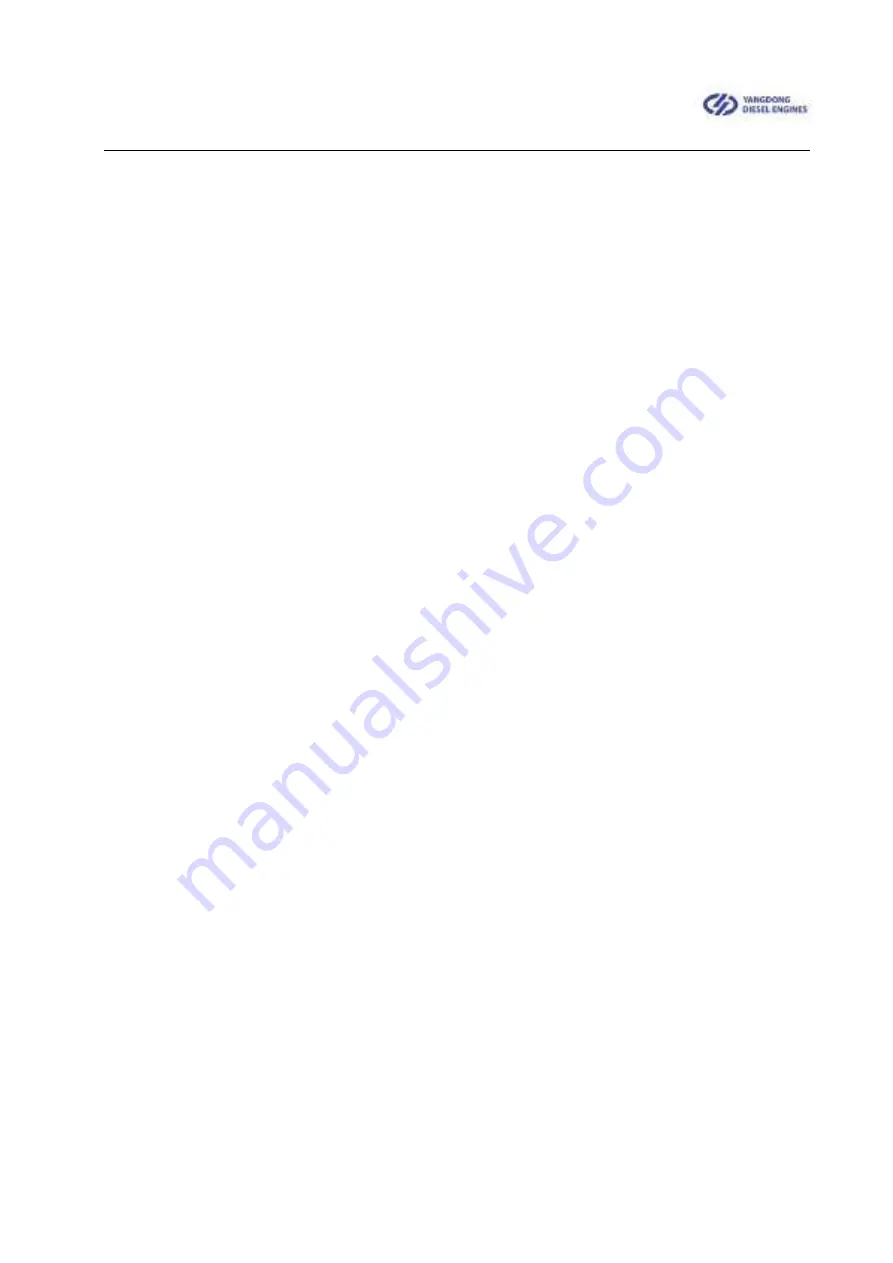
O P E R A T I O N & M A I N T E N A N C E M A N U A L
33
ring shall be 0.060-0.092mm, and the second gaseous ring shall be 0.040-0.072mm, see
figure 8 for detail.
Special purpose tool shall be employed for dismantling the piston ring. When
assembling, opening positions of each piston ring shall stagger 120 degrees and not put
on the direction of the piston pin.
During maintenance, if the piston ring can not move smoothly, immerse it in diesel
(diesel or petroleum) for twenty-four hours or longer, then knock on the piston ring. After
it is released by itself, take it out of the diesel and clean it with diesel or carbon
tetrachloride.
Check if there is any rupture or crack on the piston ring, change a new one if any
defect is found.
No.45 steel with die forging technology is made of the connecting rod. Section
surface of the connection rod body is I-beam axle. Parting plane of the big end is 45
degrees to the connecting rod body. The connecting rod and connecting rod casing shall
be corresponding borehole. Assemble it with marks and no error shall be made during
assembly. Positioning lip is used for positioning for the connecting rod and connecting
rod casing. Bolts for connecting rod are made of 40Cr steel. The upper and lower shaft
bushings for the connecting rod are made of copper-lead alloy and tin-aluminum with
support. When the clearance exceeds its limit value by abrasion or the surface wears off
or burns. Please change the new ones in couple.
Before overhaul for the diesel or assembling(disassembling) the connecting rod
assembly, clean the deposit carbon and oil stain on upper part of the cylinder sleeve.
Coat clean engine oil on cylinder trepan boring, external surface of the piston, piston ring,
shaft bush for connecting rod, crankshaft, connecting rod journal and etc, then place the
guide bush on the cylinder sleeve. Rotate the crankshaft, assemble the connecting rod in
the cylinder sleeve carefully, and tighten the bolts in turn with required force moment.
4
、
Crankshaft and flywheel
Timing gear for the crankshaft and belt pulley are installed at the front of the
crankshaft, The flying wheel is installed at the back flange and positioned by the
positioning pin. Six bolts are used for tightening the flying wheel as specified force
moment, one6203-z bearing is installed at the center of flange of the back of the