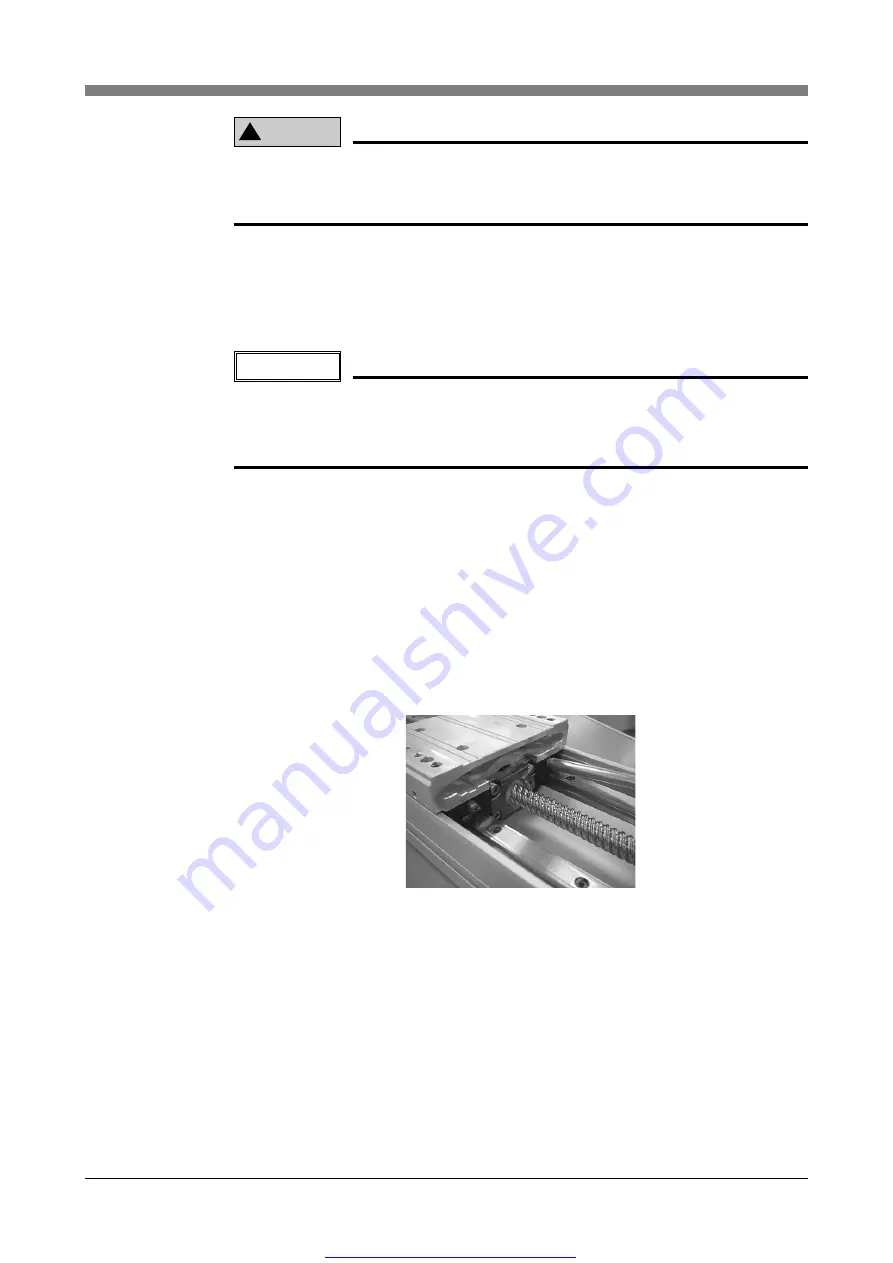
8-28
Chapter 8 SXYX
!
CAUTION
Always remove the grease nipple after completing the work. Damage or
positional deviation could occur if the robot is operated with the grease nipple
installed.
1) Prepare the following recommended grease nipple beforehand.
Recommended grease nipple
A-M6X1 type (JIS B1575)
2) Turn the controller power OFF.
NOTE
When the ZF unit is attached for the 3rd-axis, the replenishment work can be
carried out easier by moving the Z-axis slider to near the motor (near the origin)
and turning the controller power OFF.
3) Place a sign indicating “Work In Progress” so that other operators do not turn
the controller power ON.
4) Remove the stroke cover of the axis to which grease is to be replenished.
(Refer to section "1. Installation" for details on removing the X-axis cover.)
5) Install the grease nipple onto the ball screw flange.
6) Using a grease gun, replenish grease from the grease nipple.
Sufficient grease has been replenished when new grease starts to seep out
from the clearance between the ball screw nut and screw.
Wipe off any excessive grease.
Recommended grease
:
Alvania No. 2 (Showa Shell)
:
Daphne Eponex No. 2 (Idemitsu)
Recommended grease gun
:
MG70 (THK N-type nozzle)
7) Remove the grease nipple.
Содержание XY-X Series
Страница 1: ...OWNER S MANUAL Get other manuals https www bkmanuals com ...
Страница 2: ...Get other manuals https www bkmanuals com ...
Страница 10: ...MEMO Get other manuals https www bkmanuals com ...
Страница 12: ...MEMO Get other manuals https www bkmanuals com ...
Страница 30: ...MEMO Get other manuals https www bkmanuals com ...
Страница 38: ...2 8 MEMO Get other manuals https www bkmanuals com ...
Страница 40: ...MEMO Get other manuals https www bkmanuals com ...
Страница 70: ...MEMO Get other manuals https www bkmanuals com ...
Страница 78: ...4 8 MEMO Get other manuals https www bkmanuals com ...
Страница 80: ...MEMO Get other manuals https www bkmanuals com ...
Страница 86: ...5 6 MEMO Get other manuals https www bkmanuals com ...
Страница 88: ...MEMO Get other manuals https www bkmanuals com ...
Страница 98: ...6 10 MEMO Get other manuals https www bkmanuals com ...
Страница 100: ...MEMO Get other manuals https www bkmanuals com ...
Страница 152: ...MEMO Get other manuals https www bkmanuals com ...
Страница 244: ...11 40 MEMO Get other manuals https www bkmanuals com ...