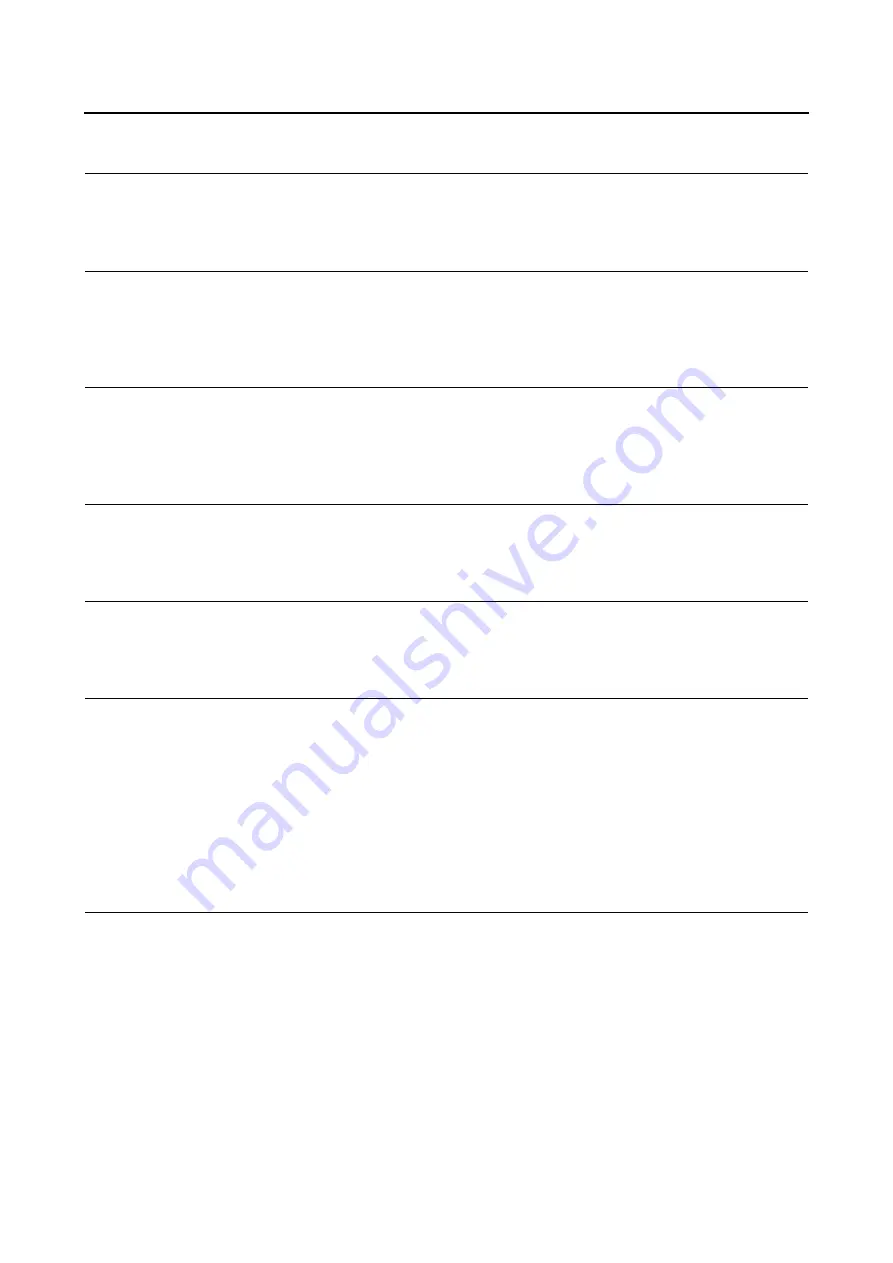
CHASSIS SPECIFICATIONS
2-7
EAS20015
CHASSIS SPECIFICATIONS
Chassis
Frame type
Double cradle
Caster angle
27.0 °
Trail
105 mm (4.1 in)
Front wheel
Wheel type
Spoke wheel
Rim size
21
×
1.85
Radial wheel runout limit
2.0 mm (0.08 in)
Lateral wheel runout limit
2.0 mm (0.08 in)
Rear wheel
Wheel type
Spoke wheel
Rim size
18M/CxMT4.00
Radial wheel runout limit
2.0 mm (0.08 in)
Lateral wheel runout limit
2.0 mm (0.08 in)
Front tire
Type
With tube
Size
90/90 – 21 M/C 54V M+S
Manufacturer/model
PIRELLI/SCORPION RALLY STR A
Rear tire
Type
With tube
Size
150/70 R18 M/C 70V M+S
Manufacturer/model
PIRELLI/SCORPION RALLY STR
Tire air pressure (measured on cold tires)
1 person
Front
220 kPa (2.20 kgf/cm², 32 psi)
Rear
250 kPa (2.50 kgf/cm², 36 psi)
2 persons
Front
220 kPa (2.20 kgf/cm², 32 psi)
Rear
250 kPa (2.50 kgf/cm², 36 psi)
Off-road riding
Front
200 kPa (2.00 kgf/cm², 29 psi)
Rear
200 kPa (2.00 kgf/cm², 29 psi)
Front brake
Type
Hydraulic dual disc brake
Front disc brake
Disc outside diameter
×
thickness
282.0
×
4.5 mm (11.10
×
0.18 in)
Brake disc thickness limit
4.0 mm (0.16 in)
Brake disc runout limit (as measured on wheel)
0.15 mm (0.0059 in)
Brake pad lining thickness limit
4.0 mm (0.16 in)
Master cylinder inside diameter
16.00 mm (0.63 in)
Caliper cylinder inside diameter (Left)
28.00 mm, 28.00 mm (1.10 in, 1.10 in)
Caliper cylinder inside diameter (Right)
28.00 mm, 28.00 mm (1.10 in, 1.10 in)
Specified brake fluid
DOT 4
Содержание XTZ690 2020
Страница 1: ...2020 SERVICE MANUAL Ténéré 700 XTZ690 XTZ690 U BW3 F8197 E0 ...
Страница 2: ......
Страница 6: ......
Страница 8: ......
Страница 56: ...CABLE ROUTING 2 33 Hydraulic unit assembly top and left side view 1 2 3 4 3 4 ...
Страница 58: ...CABLE ROUTING 2 35 Radiator front and right side view A B C 1 2 3 3 4 5 ...
Страница 60: ...CABLE ROUTING 2 37 Radiator left side view A B C D D F E G 1 1 2 2 3 4 5 6 6 7 5 ...
Страница 62: ...CABLE ROUTING 2 39 ...
Страница 65: ......
Страница 166: ...FRONT FORK 4 67 T R Front fork cap bolt 30 N m 3 0 kgf m 22 lb ft Upper bracket pinch bolt 23 N m 2 3 kgf m 17 lb ft ...
Страница 189: ...ENGINE INSPECTION 5 2 7 Install Spark plugs Ignition coils T R Spark plug 13 N m 1 3 kgf m 9 6 lb ft ...
Страница 213: ...CYLINDER HEAD 5 26 ...
Страница 252: ...CRANKCASE 5 65 a 1 2 2 b 45 10 1 ...
Страница 276: ...TRANSMISSION 5 89 4 Check Transmission Rough movement Repair TIP Oil each gear shaft and bearing thoroughly 3 2 1 c b a ...
Страница 292: ...WATER PUMP 6 15 ...
Страница 308: ...THROTTLE BODIES 7 15 ...
Страница 311: ......
Страница 317: ...IGNITION SYSTEM 8 6 ...
Страница 325: ...CHARGING SYSTEM 8 14 ...
Страница 329: ...LIGHTING SYSTEM 8 18 ...
Страница 337: ...SIGNALING SYSTEM 8 26 ...
Страница 393: ...FUEL INJECTION SYSTEM 8 82 ...
Страница 407: ...IMMOBILIZER SYSTEM 8 96 ...
Страница 452: ...ELECTRICAL COMPONENTS 8 141 ...
Страница 469: ......
Страница 470: ......