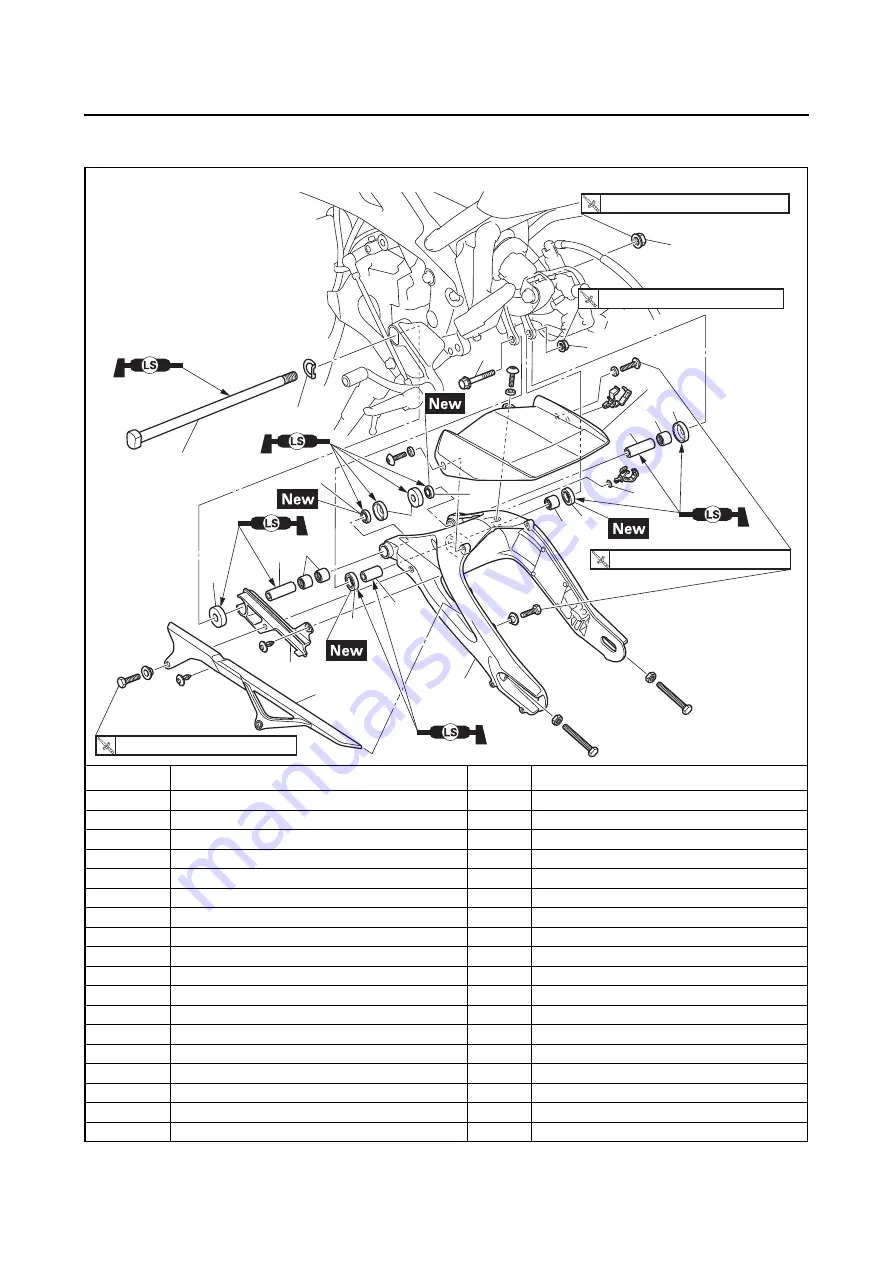
SWINGARM
4-95
EAS20037
SWINGARM
Removing the swingarm
Order
Job/Parts to remove
Q’ty
Remarks
Rear brake caliper
Refer to “REAR BRAKE” on page 4-48.
Rear wheel
Refer to “REAR WHEEL” on page 4-27.
Muffler assembly
Refer to “ENGINE REMOVAL” on page 5-3.
Drive chain
Refer to “CHAIN DRIVE” on page 4-98.
1
Connecting arm lower nut
1
2
Connecting arm lower bolt
1
3
Pivot shaft nut
1
4
Pivot shaft
1
5
Washer
1
6
Swingarm
1
7
Drive chain guard
1
8
Drive chain guide
1
9
Rear fender
1
10
Dust cover
4
11
Collar
3
12
Oil seal
4
13
Bearing
4
14
Washer
1
1
2
3
4
5
6
7
8
9
10
11
12
13
10
10
13
12
11
12
13
11
12
14
7 N
・
m (0.7 kgf
・
m, 5.1 lb
・
ft)
7 N
・
m (0.7 kgf
・
m, 5.1 lb
・
ft)
110 N
・
m (11 kgf
・
m, 80 lb
・
ft)
55 N
・
m (5.5 kgf
・
m, 40 lb
・
ft)
Содержание Tracer MT09TRAH 2017
Страница 1: ...2017 SERVICE MANUAL MT09TRA MT09TRAH 2SC 28197 E0 ...
Страница 2: ......
Страница 8: ......
Страница 59: ...LUBRICATION POINTS AND LUBRICANT TYPES 2 18 ...
Страница 62: ...LUBRICATION SYSTEM CHART AND DIAGRAMS 2 21 EAS30021 LUBRICATION DIAGRAMS 1 2 3 4 ...
Страница 64: ...LUBRICATION SYSTEM CHART AND DIAGRAMS 2 23 4 7 7 8 9 5 6 2 3 1 ...
Страница 66: ...LUBRICATION SYSTEM CHART AND DIAGRAMS 2 25 4 5 6 2 3 1 ...
Страница 68: ...LUBRICATION SYSTEM CHART AND DIAGRAMS 2 27 6 5 3 2 7 4 1 ...
Страница 70: ...LUBRICATION SYSTEM CHART AND DIAGRAMS 2 29 9 8 7 6 3 3 2 5 4 1 ...
Страница 72: ...COOLING SYSTEM DIAGRAMS 2 31 EAS20020 COOLING SYSTEM DIAGRAMS 1 1 2 3 ...
Страница 73: ...COOLING SYSTEM DIAGRAMS 2 32 1 Water pump 2 Thermostat 3 Radiator ...
Страница 74: ...COOLING SYSTEM DIAGRAMS 2 33 1 2 3 4 5 6 ...
Страница 76: ...CABLE ROUTING 2 35 EAS20021 CABLE ROUTING Handlebar top view ...
Страница 78: ...CABLE ROUTING 2 37 Handlebar front view ...
Страница 80: ...CABLE ROUTING 2 39 Radiator front side view and right side view ...
Страница 82: ...CABLE ROUTING 2 41 Fuel tank left and bottom view ...
Страница 84: ...CABLE ROUTING 2 43 Canister top view and left side view ...
Страница 86: ...CABLE ROUTING 2 45 Air filter case and throttle body top view and left side view ...
Страница 88: ...CABLE ROUTING 2 47 Air cut off valve left side view ...
Страница 90: ...CABLE ROUTING 2 49 Frame and engine right side view ...
Страница 92: ...CABLE ROUTING 2 51 Frame and engine right side view ...
Страница 94: ...CABLE ROUTING 2 53 Frame and engine left side view ...
Страница 96: ...CABLE ROUTING 2 55 Frame top view ...
Страница 98: ...CABLE ROUTING 2 57 Frame top view ...
Страница 100: ...CABLE ROUTING 2 59 Frame top view ...
Страница 102: ...CABLE ROUTING 2 61 Front brake right side view and left side view ...
Страница 104: ...CABLE ROUTING 2 63 Rear brake ...
Страница 106: ...CABLE ROUTING 2 65 Hydraulic unit top view and left side view ...
Страница 108: ...CABLE ROUTING 2 67 ...
Страница 148: ...GENERAL CHASSIS 1 4 5 1 a b ...
Страница 177: ...REAR WHEEL 4 34 Thickness gauge 90890 03180 Feeler gauge set YU 26900 9 1 2 a ...
Страница 190: ...FRONT BRAKE 4 47 BRAKE SYSTEM ABS on page 3 15 ...
Страница 246: ...CHAIN DRIVE 4 103 ...
Страница 267: ...CAMSHAFTS 5 18 TIP Install the ignition coils 1 in the direction shown in the illustration 1 ...
Страница 334: ...TRANSMISSION 5 85 ...
Страница 362: ...AIR INDUCTION SYSTEM 7 15 EAS20071 AIR INDUCTION SYSTEM 1 2 3 2 3 4 4 ...
Страница 368: ...AIR INDUCTION SYSTEM 7 21 ...
Страница 371: ......
Страница 372: ...IGNITION SYSTEM 8 1 EAS20072 IGNITION SYSTEM EAS30490 CIRCUIT DIAGRAM ...
Страница 377: ...IGNITION SYSTEM 8 6 ...
Страница 378: ...ELECTRIC STARTING SYSTEM 8 7 EAS20073 ELECTRIC STARTING SYSTEM EAS30493 CIRCUIT DIAGRAM ...
Страница 384: ...CHARGING SYSTEM 8 13 EAS20074 CHARGING SYSTEM EAS30496 CIRCUIT DIAGRAM ...
Страница 387: ...CHARGING SYSTEM 8 16 ...
Страница 388: ...LIGHTING SYSTEM 8 17 EAS20075 LIGHTING SYSTEM EAS30498 CIRCUIT DIAGRAM ...
Страница 391: ...LIGHTING SYSTEM 8 20 ...
Страница 392: ...SIGNALING SYSTEM 8 21 EAS20076 SIGNALING SYSTEM EAS30500 CIRCUIT DIAGRAM ...
Страница 398: ...COOLING SYSTEM 8 27 EAS20077 COOLING SYSTEM EAS30502 CIRCUIT DIAGRAM ...
Страница 401: ...COOLING SYSTEM 8 30 ...
Страница 402: ...FUEL INJECTION SYSTEM 8 31 EAS20078 FUEL INJECTION SYSTEM EAS30504 CIRCUIT DIAGRAM ...
Страница 474: ...FUEL PUMP SYSTEM 8 103 EAS20081 FUEL PUMP SYSTEM EAS30513 CIRCUIT DIAGRAM ...
Страница 477: ...FUEL PUMP SYSTEM 8 106 ...
Страница 478: ...IMMOBILIZER SYSTEM 8 107 EAS20084 IMMOBILIZER SYSTEM EAS30519 CIRCUIT DIAGRAM ...
Страница 487: ...IMMOBILIZER SYSTEM 8 116 ...
Страница 488: ...ABS ANTI LOCK BRAKE SYSTEM 8 117 EAS20085 ABS ANTI LOCK BRAKE SYSTEM EAS30843 CIRCUIT DIAGRAM ...
Страница 490: ...ABS ANTI LOCK BRAKE SYSTEM 8 119 EAS30525 ABS COMPONENTS CHART 1 2 3 4 5 8 9 1 6 7 ...
Страница 492: ...ABS ANTI LOCK BRAKE SYSTEM 8 121 EAS30844 ABS COUPLER LOCATION CHART 2 1 3 4 5 ...
Страница 520: ...ELECTRICAL COMPONENTS 8 149 EAS20089 ELECTRICAL COMPONENTS ...
Страница 522: ...ELECTRICAL COMPONENTS 8 151 1 2 3 4 5 6 7 8 9 10 11 12 13 14 15 16 17 18 19 ...
Страница 546: ...ELECTRICAL COMPONENTS 8 175 ...
Страница 571: ......
Страница 572: ......