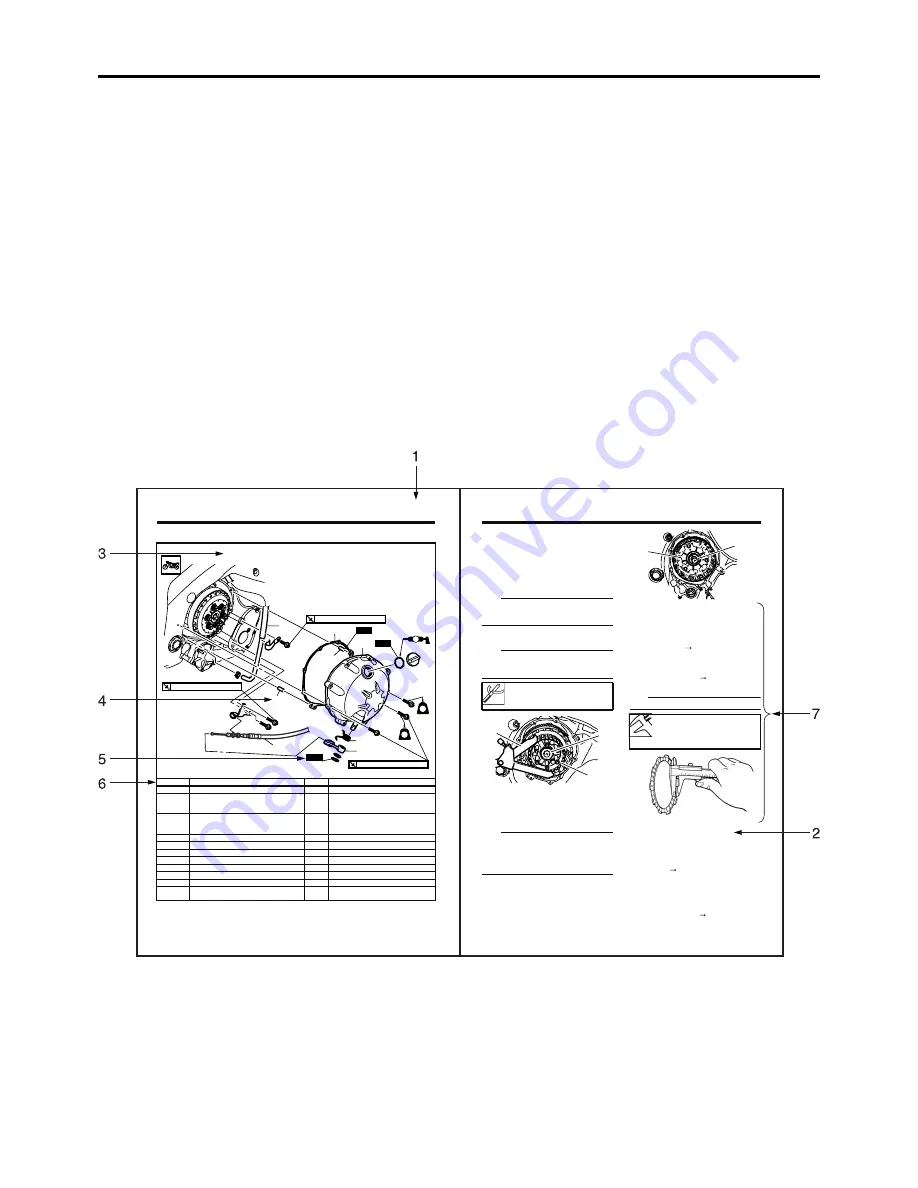
EAS20090
HOW TO USE THIS MANUAL
This manual is intended as a handy, easy-to-read reference book for the mechanic. Comprehensive
explanations of all installation, removal, disassembly, assembly, repair and check procedures are
laid out with the individual steps in sequential order.
• The manual is divided into chapters and each chapter is divided into sections. The current section
title “1” is shown at the top of each page.
• Sub-section titles “2” appear in smaller print than the section title.
• To help identify parts and clarify procedure steps, there are exploded diagrams “3” at the start of
each removal and disassembly section.
• Numbers “4” are given in the order of the jobs in the exploded diagram. A number indicates a dis-
assembly step.
• Symbols “5” indicate parts to be lubricated or replaced.
Refer to “SYMBOLS”.
• A job instruction chart “6” accompanies the exploded diagram, providing the order of jobs, names
of parts, notes in jobs, etc.
• Jobs “7” requiring more information (such as special tools and technical data) are described
sequentially.
CLUTCH
5-36
EAS25060
CLUTCH
Removing the clutch cover
Order
Job/Parts to remove
Q’ty
Remarks
.
1
-
4
e
g
a
p
n
o
”
S
I
S
S
A
H
C
L
A
R
E
N
E
G
“
o
t
r
e
f
e
R
y
l
b
m
e
s
s
a
g
n
il
w
o
c
e
d
i
S
Engine oil
Drain.
Refer to “CHANGING THE ENGINE OIL” on
page 3-12.
Coolant
Drain.
Refer to “CHANGING THE COOLANT” on
page 3-21.
.
t
c
e
n
n
o
c
s
i
D
1
e
s
o
h
r
e
h
t
a
e
r
b
p
m
u
p
r
e
t
a
W
1
.
t
c
e
n
n
o
c
s
i
D
1
e
l
b
a
c
h
c
t
u
l
C
2
1
r
e
v
e
l
ll
u
P
3
1
g
n
i
r
p
s
r
e
v
e
l
ll
u
P
4
1
r
e
v
o
c
h
c
t
u
l
C
5
1
t
e
k
s
a
g
r
e
v
o
c
h
c
t
u
l
C
6
2
n
i
p
l
e
w
o
D
7
For installation, reverse the removal proce-
dure.
5
2
6
7
1
3
4
7
LT
New
New
LT
New
LS
T
R
.
.
12 Nm (1.2 m
•
kg, 8.9 ft
•
Ib)
T
R
.
.
12 Nm (1.2 m
•
kg, 8.9 ft
•
Ib)
T
R
.
.
12 Nm (1.2 m
•
kg, 8.9 ft
•
Ib)
CLUTCH
5-40
EAS25070
REMOVING THE CLUTCH
1. Remove:
• Oil strainer
Refer to “OIL PUMP” on page 5-48.
• Water pump
Refer to “WATER PUMP” on page 6-8.
• Friction plates
• Clutch plates
NOTE:
Be sure to mark the friction plates and clutch
plates or note the position of each part so that
they are installed in their original positions.
2. Loosen:
• Clutch boss nut “1”
NOTE:
While holding the clutch boss “2” with the uni-
versal clutch holder “3”, loosen the clutch boss
nut.
3. Remove:
• Spacer “1”
• Bearing
• Clutch housing “2”
• Oil pump drive chain
NOTE:
Remove the spacer and bearing from the main
axle, then remove the oil pump drive chain
from the oil pump driven sprocket, and then
remove the clutch housing and oil pump drive
chain from the main axle.
EAS25100
CHECKING THE FRICTION PLATES
The following procedure applies to all of the
friction plates.
1. Check:
• Friction plate
Damage/wear
Replace the friction
plates as a set.
2. Measure:
• Friction plate thickness
Out of specification
Replace the fric-
tion plates as a set.
NOTE:
Measure the friction plate at four places.
EAS25110
CHECKING THE CLUTCH PLATES
The following procedure applies to all of the
clutch plates.
1. Check:
• Clutch plate
Damage
Replace the clutch plates as
a set.
2. Measure:
• Clutch plate warpage
(with a surface plate and thickness gauge
“1”)
Out of specification
Replace the clutch
plates as a set.
Universal clutch holder
90890-04086
YM-91042
1
2
3
Friction plate thickness
2.92–3.08 mm (0.115–0.121 in)
Wear limit
2.80 mm (0.1102 in)
2
1