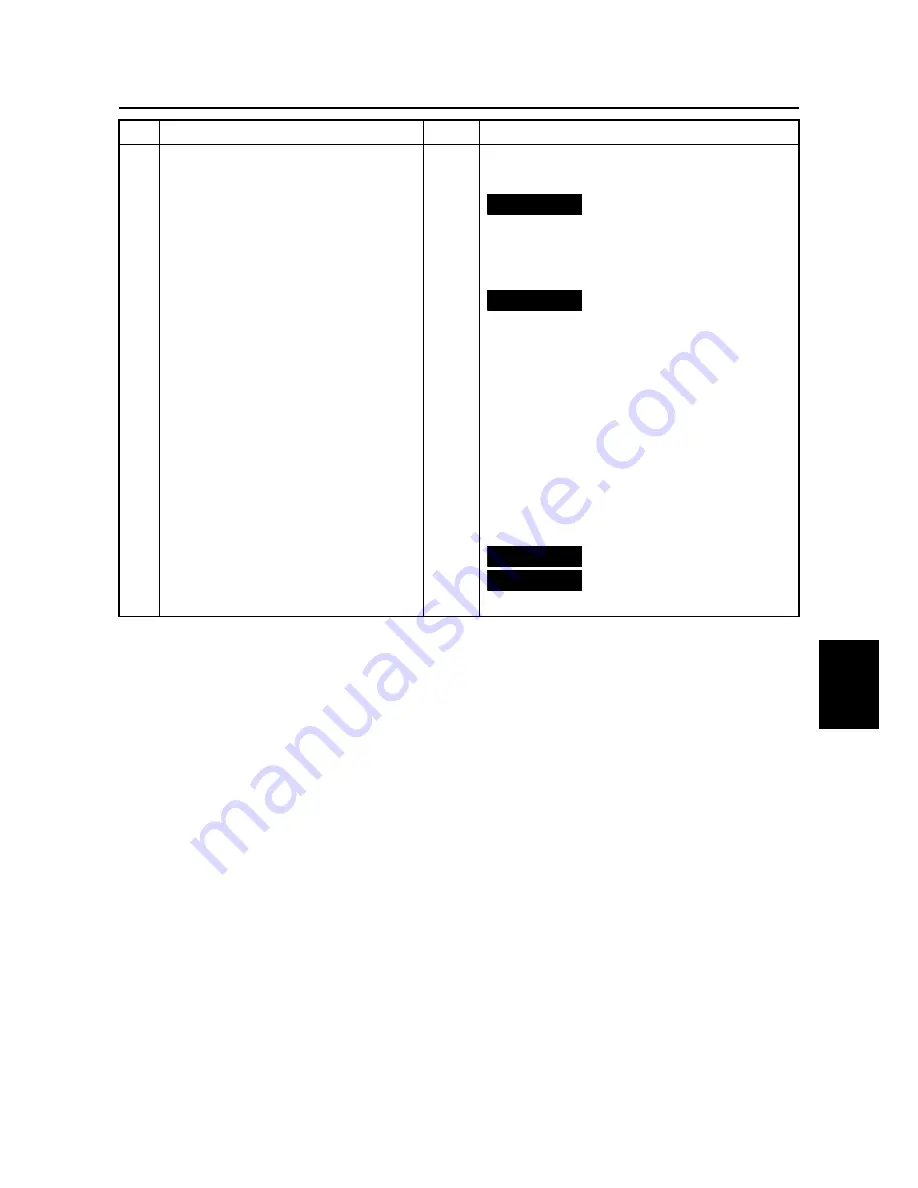
69J1D11
6-16
1
2
3
4
5
6
7
8
9
No.
Part name
Q’ty
Remarks
1
Drive shaft
1
2
Cover
1
3
Oil seal
2
Not reusable
4
Bolt
4
M8
×
25 mm
5
Drive shaft housing
1
6
Needle bearing
1
7
O-ring
1
Not reusable
3
×
60.5 mm
8
Pinion shim
—
As required
9
Thrust bearing
1
10
Lower case
1
11
Needle bearing outer case
1
12
Needle bearing
24
13
Pinion
1
14
Washer
1
15
Nut
1
16
Forward gear shim
—
As required
17
Bearing outer race
1
Not reusable
18
Taper roller bearing
1
Not reusable
19
Forward gear
1
Drive shaft and lower case (regular rotation model)
Содержание F200C
Страница 1: ...F200C LF200C F225C LF225C SERVICE MANUAL 69J 28197 1F 11 LIT 18616 02 76 LIT186160276 ...
Страница 47: ...69J1D11 2 10 1 2 3 4 5 6 7 8 9 MEMO Maintenance specifications ...
Страница 75: ...69J1D11 3 20 1 2 3 4 5 6 7 8 9 Lubrication 1 Apply water resistant grease to the areas shown General ...
Страница 80: ...FUEL Fuel system 4 3 69J1D11 Intake silencer fuel filter and fuel pump 4 ...
Страница 82: ...FUEL Fuel system 4 5 69J1D11 Vapor separator 4 ...
Страница 86: ...FUEL Fuel system 4 9 69J1D11 Intake manifold and high pressure fuel line 4 ...
Страница 88: ...FUEL Fuel system 4 11 69J1D11 ...
Страница 90: ...FUEL Fuel system 4 13 69J1D11 Throttle control 4 ...
Страница 101: ...69J1D11 5 2 1 2 3 4 5 6 7 8 9 Piston ring compressor YM 08037 Special service tools ...
Страница 102: ...POWR Power unit 5 3 69J1D11 Power unit 5 ...
Страница 104: ...POWR Power unit 5 5 69J1D11 ...
Страница 106: ...POWR Power unit 5 7 69J1D11 ...
Страница 110: ...POWR Power unit 5 11 69J1D11 ...
Страница 128: ...POWR Power unit 5 29 69J1D11 Cylinder head 5 ...
Страница 130: ...POWR Power unit 5 31 69J1D11 ...
Страница 142: ...POWR Power unit 5 43 69J1D11 Cylinder block 5 ...
Страница 144: ...POWR Power unit 5 45 69J1D11 ...
Страница 172: ...LOWR Lower unit 6 9 69J1D11 Propeller shaft housing regular rotation model 6 ...
Страница 178: ...LOWR Lower unit 6 15 69J1D11 Drive shaft and lower case regular rotation model 6 ...
Страница 194: ...LOWR Lower unit 6 31 69J1D11 ...
Страница 198: ...LOWR Lower unit 6 35 69J1D11 Propeller shaft housing counter rotation model 6 ...
Страница 204: ...LOWR Lower unit 6 41 69J1D11 Drive shaft and lower case counter rotation model 6 ...
Страница 223: ...69J1D11 7 2 1 2 3 4 5 6 7 8 9 MEMO Special service tools ...
Страница 224: ...BRKT Bracket unit 7 3 69J1D11 Bottom cowling 7 ...
Страница 226: ...BRKT Bracket unit 7 5 69J1D11 ...
Страница 228: ...BRKT Bracket unit 7 7 69J1D11 Upper case steering arm swivel bracket and clamp brackets 7 ...
Страница 230: ...BRKT Bracket unit 7 9 69J1D11 ...
Страница 232: ...BRKT Bracket unit 7 11 69J1D11 ...
Страница 242: ...BRKT Bracket unit 7 21 69J1D11 Power trim and tilt unit 7 ...
Страница 244: ...BRKT Bracket unit 7 23 69J1D11 ...
Страница 246: ...BRKT Bracket unit 7 25 69J1D11 ...
Страница 288: ...ELEC Electrical systems 8 21 69J1D11 Starter motor 8 ...
Страница 321: ...YAMAHA MOTOR CORPORATION USA Printed in USA Sep 2003 0 0 1 CR E ...