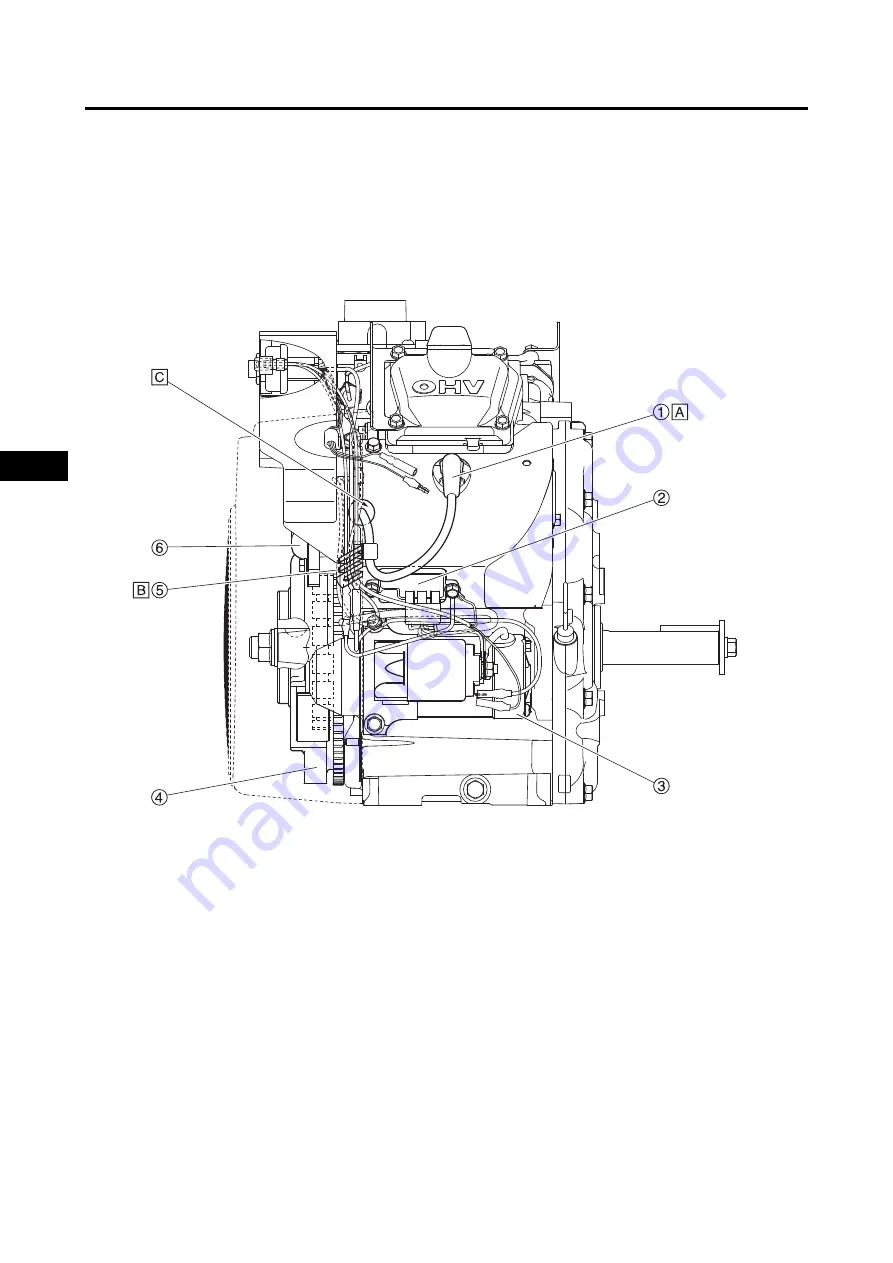
WIRE ROUTING DIAGRAM
7-40
1
2
3
4
5
6
7
8
9
10
SP
ECIFIC
A
T
IO
NS
RECTIFIER/REGULATOR AND STARTER MOTOR (EH65A)
1. Spark plug cap
4. Flywheel
2. Rectifier/regulator
5. Clamp
3. Starter motor
6. TCI unit #1
A. Point the spark plug cap in the direction shown in the illustration.
B. Bundle 1.5 or more volumes other than the wire of the carburetor.
C. Install the grommet all the way to the back of the fan case groove.
Содержание EH63
Страница 2: ...7D5 28197 E0_cover indd 3 4 2019 03 12 10 04 33 ...
Страница 12: ...MEMO ...
Страница 26: ...SPECIAL TOOLS AND TESTERS 1 14 1 2 3 4 5 6 7 8 9 10 GENERAL INFORMATION MEMO ...
Страница 108: ...PISTONS CAMSHAFT CRANKCASE AND CRANKSHAFT 3 64 1 2 3 4 5 6 7 8 9 10 ENGINE MEMO ...
Страница 128: ...ELECTRICAL COMPONENTS 5 3 1 2 3 4 5 6 7 8 9 10 ELECTRICAL ELECTRICAL COMPONENTS 3 1 1 6 5 2 4 ...
Страница 138: ...CHARGING SYSTEM 5 13 1 2 3 4 5 6 7 8 9 10 ELECTRICAL MEMO ...
Страница 144: ...GOVERNOR OPERATION 6 6 1 2 3 4 5 6 7 8 9 10 TROUBLESHOOTING MEMO ...
Страница 189: ...WIRE ROUTING DIAGRAM 7 45 1 2 3 4 5 6 7 8 9 10 SPECIFICATIONS MEMO ...
Страница 190: ...APPENDIX CIRCUIT DIAGRAM G M B L S OFF RUN START B B R R W Y Y Gy B W Y R W B G 1 2 3 4 5 6 7 e 8 8 9 0 q w ...
Страница 192: ...MEMO ...
Страница 193: ...7D5 28197 E0_cover indd 3 4 2019 03 12 10 04 33 ...
Страница 194: ...SERVICE MANUAL EH63 EH64 EH65 EH72 7D5 28197 E0 2019 03 1 7D5 28197 E0_cover indd 1 2 2019 03 12 10 04 33 ...