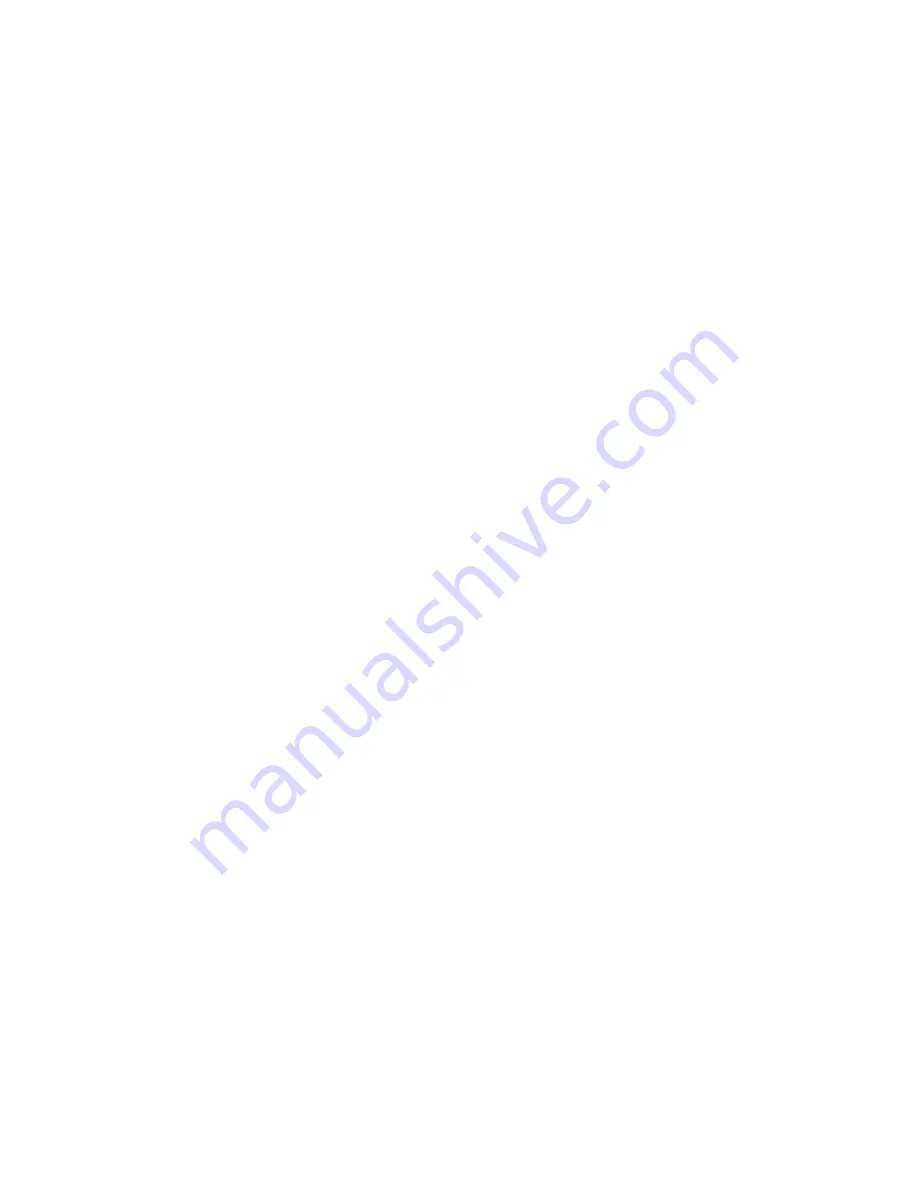
5
Example for temperature correction: The current set temperature value is 200
℃
,
but the actual temperature is only 190
℃
. So it needs to correct by +10
℃
.
Correction method: if the current correction value is 00 or -00; then change it to
10. If the current correction value is -20, then change it to -10. If the current
correction value is 20, then change it to 30.
5.
Fahrenheit and Centigrade (Celsius) temperature selection
When temperature display window shows "F-3" and blinking, press the "SET"
button, at this time ,the system enters the degrees Fahrenheit and Centigrade
temperature selection function, indicating the temperature of the window shows
the current status. Press "▲" or "▼" key to change the temperature selection
status. It expressed as degrees Celsius temperature value If set to
℃
; it shows as
degrees Fahrenheit temperature if set to
℉.
WORKING TEMPERATURE
To meet RoHS requirement, the 60/40 solder alloys are not allowed in the production
process. The lead free solder alloys require a working temperature of 30
℃ (54℉)
higher than previous generation electrical soldering. A low iron temperature will slow
the rate of flow of the solder. A high temperature will burn the flux in the solder,
which in turn will emit a heavy white smoke resulting in a dry joint, or damage to the
P.C.B. When the tip working temperature is set to the correct temperature parameters
suited to the particular solder being used, a good joint is assured.
The working temperature of solder is detailed below and can vary from manufacture
to manufacture.
Melting point
220
℃
(428
℉
)
Normal operation
300-360
℃
(572-680
℉
)
Production line operation
360-410
℃
(680-770
℉
)
IMPORTANT
: The temperature above 410
℃
(770
℉
) is not recommended for
normal soldering functions, but can be used for short periods of time when high
temperatures are required.
Please note
that the lead free solder alloys require a higher
soldering temperature which shortens tip life.
COMMON CAUSES OF TIP UNWETTING
1. Tip temperature higher than 410
℃
(770
℉
).
2. The tip working surfaces are not well tinned while the iron idling.
3. Lack of flux in soldering, wicking, repairing, and touch-up, etc operation.
4. Wiping tip on a high sulphur content sponge, dirty or dry sponge and/or rage.
5. Touching with organic, such as plastic resins, silicone grease and other chemicals.
6. Impurities in solder and low tin content.