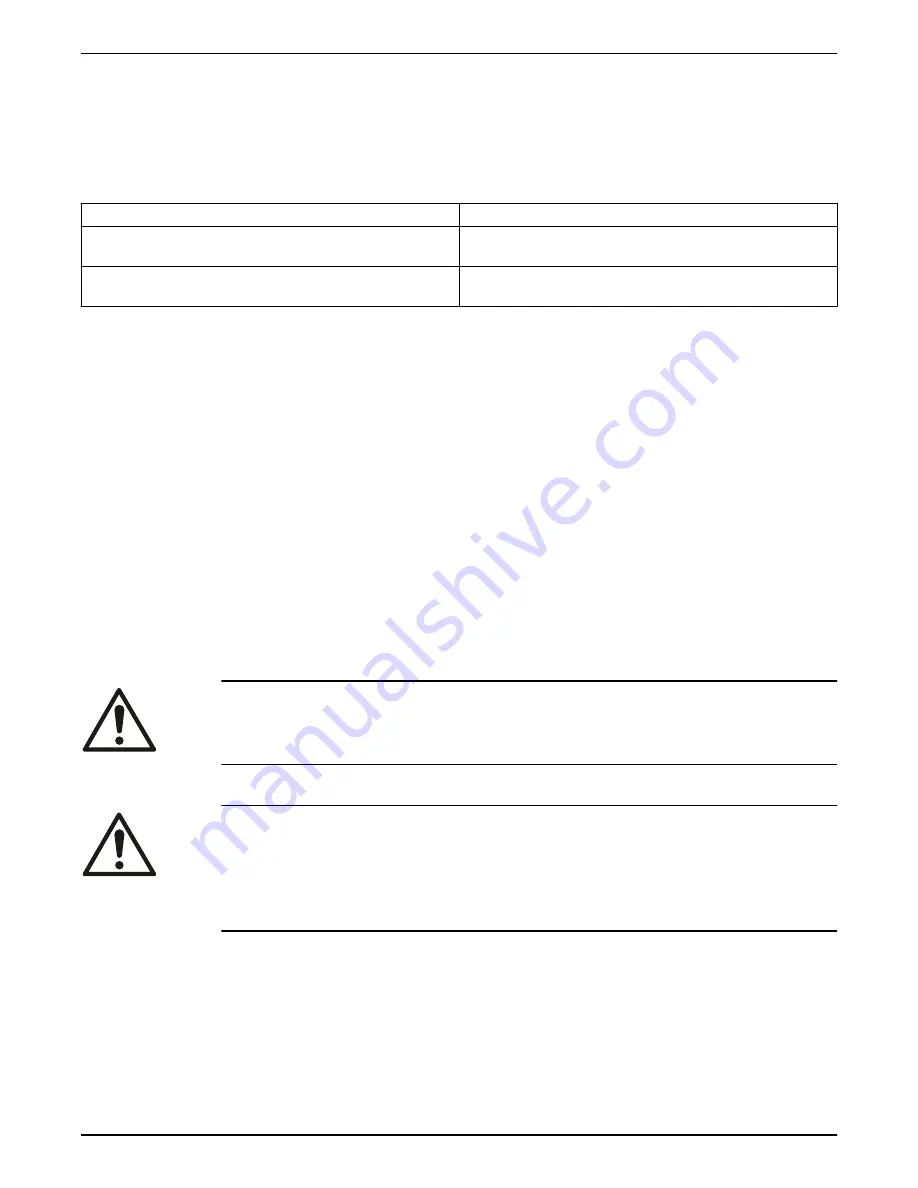
9. Assure that pump is full of liquid (see priming) and all valves are properly set and
operational, with the discharge valve closed, and the suction valve open.
10.Check rotation. Be sure that the driver operates in the direction indicated by the arrow
on the pump casing as serious damage can result if the pump is operated with
incorrect rotation. Check rotation each time the motor leads have been disconnected.
5.1.2 Priming
Type of installation
Procedure
Positive head on the suction
Open the suction and vent valve and allow the liquid to enter the
casing.
Suction lift
Use other methods such as foot valves, ejectors or by manually filling
the casing and suction line.
5.1.3 Starting
1. Close drain valves and valve in discharge line.
2. Open fully all valves in the suction line.
3. Prime the pump.
NOTE: If the pump does not prime properly, or loses prime during start-up, it should
be shut down and the condition corrected before the procedure is repeated.
4. When the pump is operating at full speed, open the discharge valve slowly. This
should be done after start-up to prevent damage to pump by operating at zero flow.
5.1.4 Operating checks
1. Check the pump and piping to assure that there are no leaks.
2. Check and record pressure gauge readings for future reference.
3. Check and record voltage, amperage per phase, and kw if an indicating wattmeter is
available.
4. Check bearings for lubrication and temperature. Normal temperature is 180°F
maximum.
5. Make all pump output adjustments with the discharge line.
CAUTION:
• Do not throttle the suction line to adjust the pump output.
• Do not let heated pump temperature rise above 150°F.
5.1.5 Check the rotation
WARNING:
• Operating the pump in reverse rotation can result in the contact of metal parts, heat
generation, and breach of containment.
• Always disconnect and lock out power to the driver before you perform any installation
or maintenance tasks. Failure to disconnect and lock out driver power will result in
serious physical injury.
1. Unlock power to the driver.
2. Make sure that everyone is clear, and then jog the driver long enough to determine
that the direction of rotation corresponds to the arrow on the pump.
3. Lock out power to the driver.
5 Commissioning, Startup, Operation, and Shutdown
24
G&L Pumps Series A-C 9100 Base Mounted Centrifugal Pumps INSTRUCTION MANUAL
Содержание G&L A-C 9100 Series
Страница 1: ...INSTRUCTION MANUAL AC5657C G L Pumps Series A C 9100 Base Mounted Centrifugal Pumps...
Страница 2: ......
Страница 57: ......
Страница 58: ......
Страница 59: ......