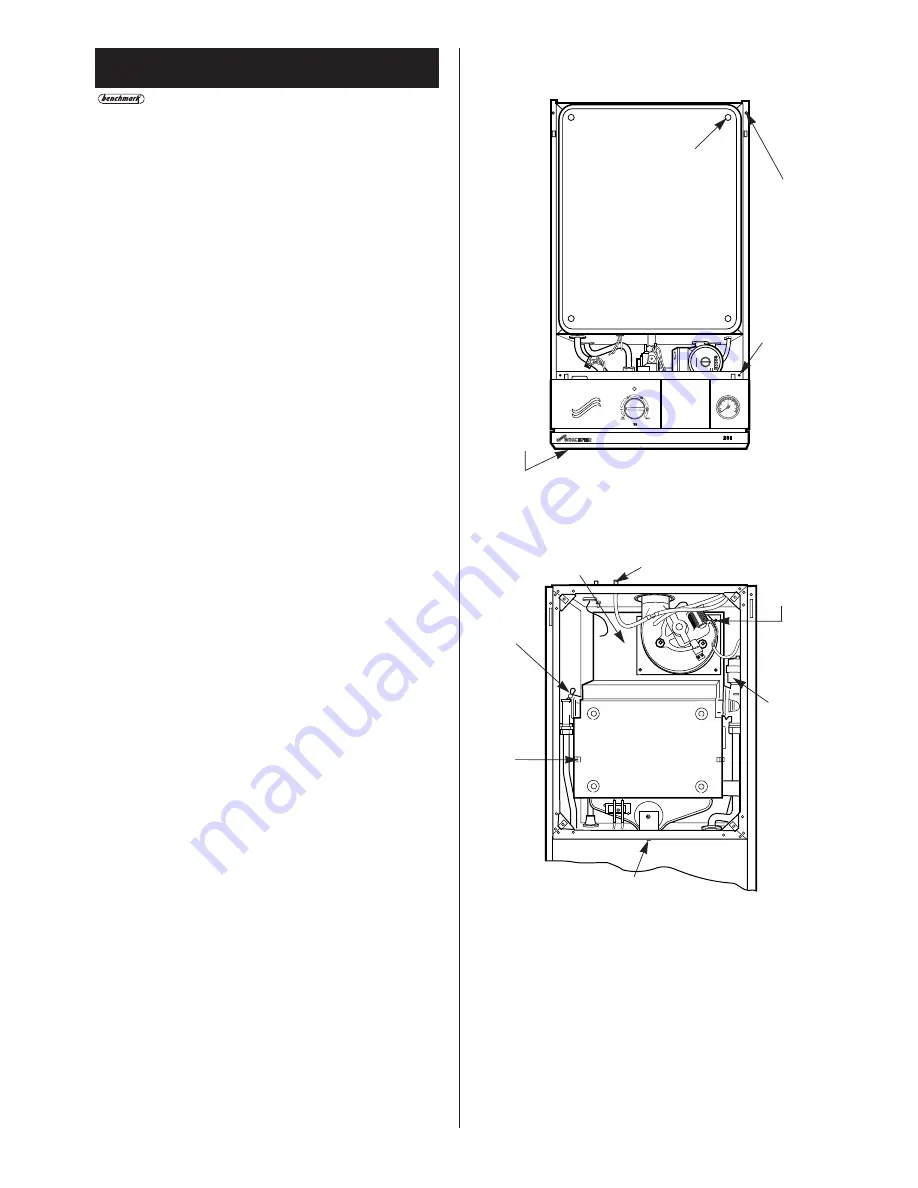
15.1 SERVICING
To ensure continued efficient operation of the appliance it must
be checked and serviced as necessary at regular intervals. The
frequency of servicing will depend upon the particular
installation conditions and usage, but once per year should
generally be adequate. The extent of the service required by the
appliance is determined by the operating condition of the
appliance when tested by fully qualified engineers.
Any service work must be carried out by competent engineers
such as British Gas or Corgi registered personnel.
15.2 PRE-SERVICE INSPECTION
Check that the flue terminal and the terminal guard, (if fitted), are
clear.
If the appliance is in a compartment, check that the ventilation
openings in the compartment door or walls are clear. See Section
6 - Air Supply.
Check the system and remake any joints or fittings which show
signs of leakage.
Refill, vent and re-pressurise as described in Section 13.2.
Operate the appliance and the system taking note of any faults.
Measurement of the Flue Gases
For consistency of results of the flue gas measurements it is
necessary to have a constant output and for the appliance to be
at equilibrium.
Turn on a tap to create a hot water demand.
Wait until the appliance reaches thermal equilibrium (approx. 10
minutes).
Remove the test point sealing screw on the appliance top panel.
See Fig. 17 and 30.
Connect to the test point with a piece of tubing.
Expected measurements should be between:
For Natural Gas:
7.0 - 7.5%
Carbon Dioxide
0.003 - 0.007%
Carbon Monoxide
After taking the measurement replace the sealing cap.
IMPORTANT
Disconnect the electrical supply at the mains and turn off the
gas supply at the gas service cock on the appliance before
servicing.
After completing the service always test for gas soundness as
indicated in BS 6891.
15.3 DISMANTLE THE APPLIANCE
To carry out a full and comprehensive service of the appliance
remove the following parts to gain access to the components
which need to be checked or serviced.
(a) Cabinet Front Panel.
Remove by lifting off the supports.
(b) Inner Casing Cover.
Check that the electricity supply to the
appliance is turned off. Remove the cabinet front panel. Unscrew
the four screws securing the cover to the casing and lift off. See Fig. 35.
(c) Facia Panel.
Check that the electricity supply to the appliance
is turned off. Remove the cabinet front panel. Unscrew the two
upper screws as shown in Fig. 35. and hinge down the facia
taking care not to damage the pressure gauge capillary tube or
electrical connections.
(d) Bottom panel.
Unclip and remove the appliance bottom panel.
(e) Fan.
Remove the inner casing cover as detailed in Section
15.3(b) above. Carefully unplug the electrical connections and
pull off the sensing tubes. Unscrew the four fixing screws and
remove the fan assembly. See Fig. 36.
(f) Combustion Chamber Front.
Remove the inner casing cover.
Undo the spring clips fixing the combustion chamber front
taking care not to damage the insulation on removal. See Fig. 36.
(g) Flue Hood Assembly.
Remove the fan assembly as described
in Section 15.3(e). Remove the combustion chamber front taking
care not to damage the insulation. Lift and slide the flue hood
assembly from the appliance. See Fig. 36. When refitting the hood
ensure that the rear return edge passes under the lip at the rear of the
combustion chamber.
15. Inspection And Service
21
Inner casing
cover
screws (4)
Side casing
fixing
screws (4)
Facia panel
fixing
screws (2)
Bottom
facia panel
fixing
screws (3)
Fig.35. Appliance casing and control
equipment fixings.
Fig. 36. Appliance components and fixings
(upper assembly).
1
7
5
6
4
3
2
1 Flue hood
2 Flue Gas Test Point
3 Fan assembly fixing screws (4)
4 Auto air vent
5 Burner fixing screw
6 Combustion chamber cover fixing clips (2)
7 Overheat thermostat
Содержание 28i RSF
Страница 38: ...38 9 8 14 3 21 1 15 13 4 22 11 7 12 10 23 20 6 25 24 2 19 18 16 24 23 20 3 5 ...
Страница 39: ...39 ...