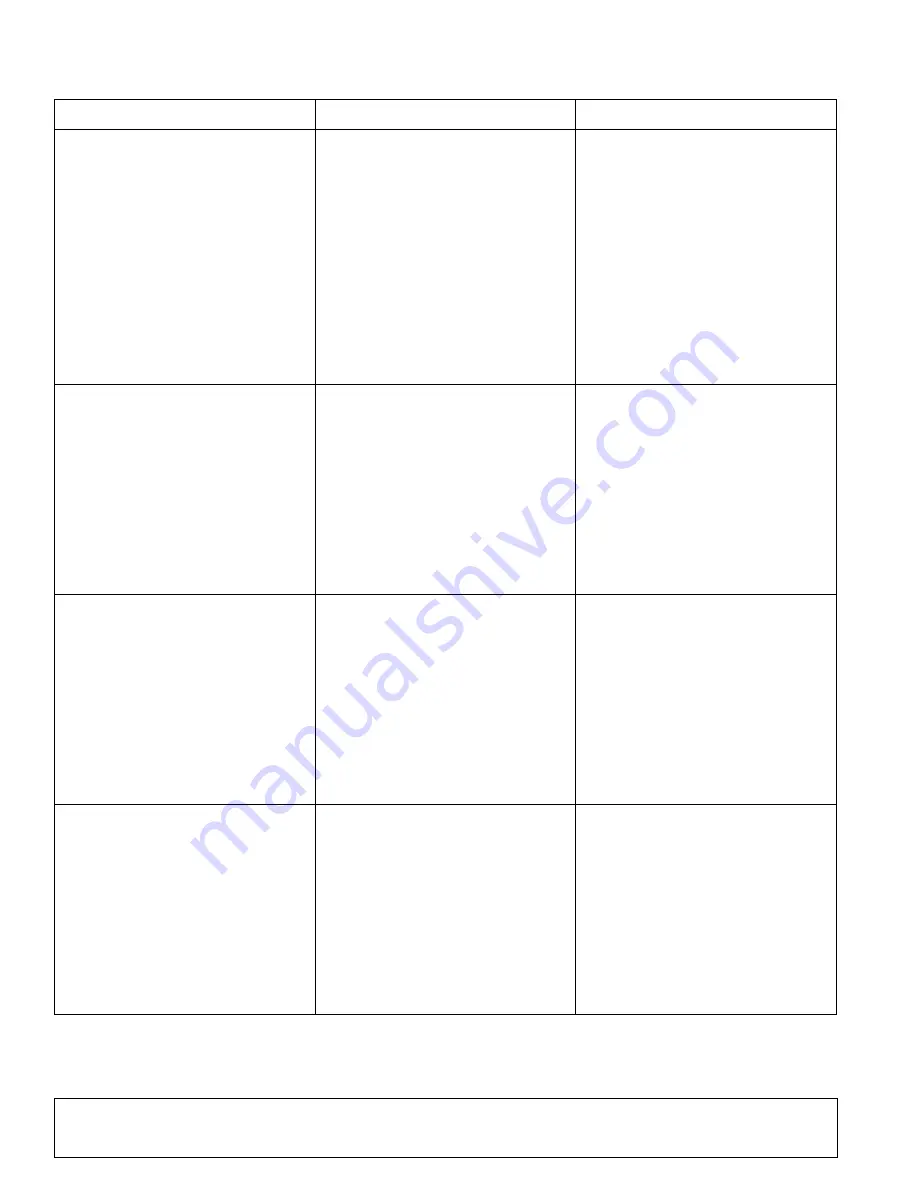
14
Troubleshooting
MPS9 (Rev. 4/20/2007)
TROUBLESHOOTING
PROBLEM
POSSIBLE CAUSE
SOLUTION
Cutting wheel does not operate.
Auxiliary hoses are not hooked up to
skid steer.
Inspect connections visually (make
sure QDs are fully engaged).
The diverter valve is in the sideshift
position (MD model only).
Make sure diverter valve is pushed
inward as far as possible.
There is an obstruction in one or
both of the auxiliary hoses.
Remove and inspect hoses visually.
One or more seals on the motor has
failed.
Contact dealer.
Motor shaft key has failed.
Remove and visually inspect motor.
Skid steer auxiliary hydraulics are
not operating properly.
Refer to skid steer owner’s manual.
Cutting wheel rotates sluggishly or
insufficient cutting power.
The diverter valve is not fully shifted
to the saw position (MD only).
Insufficient hydraulic flow from the
skid steer.
Make sure diverter valve is pushed
inward as far as possible.
The hydraulic oil filter on the skid
steer is dirty.
Refer to skid steer owner’s manual.
Relief valve on the skid steer is not
set properly.
Refer to skid steer owner’s manual.
One or more seals on the motor
have failed.
Contact dealer.
Oil is leaking from the motor area.
One or more seals on the motor
have failed.
Contact dealer.
O-rings on fittings are damaged.
Visually inspect O-rings and replace
as needed.
O-ring between planetary and motor
has failed.
Verify condition of O-ring and
replace as needed.
Fittings are loose or damaged.
Tighten or replace as needed.
Hydraulic hoses are loose or
damaged.
Tighten or replace as needed.
Excessive oil temperature (more
than 180° F).
Obstruction in one or both auxiliary
hydraulic hoses.
Remove and visually inspect hoses.
Replace as needed.
Hydraulic oil level on skid steer is
low.
Refer to skid steer owner’s manual.
Hydraulic oil in skid steer is dirty.
Refer to skid steer owner’s manual.
Hydraulic oil filter on skid steer is
dirty or clogged.
Refer to skid steer owner’s manual.
Relief valve on skid steer is not set
properly.
Refer to skid steer owner’s manual.